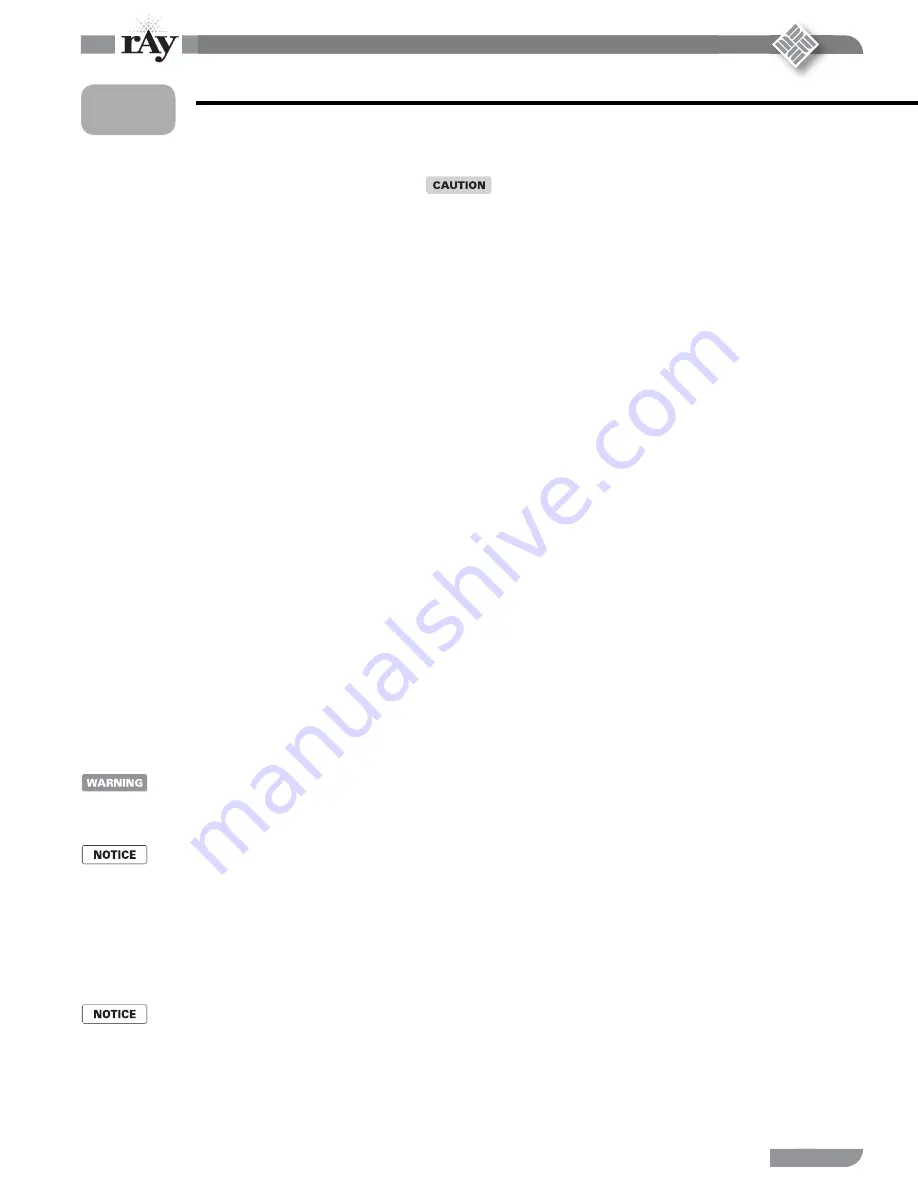
11
P/N 42-9470 11/07 Copyright 2007 Mestek, Inc.
Cast iron condensing boiler
Cast iron condensing boiler
— Installation and operation manual
Water piping
Th e
200i
boiler requires a continuous minimum water fl ow for proper
operation. Th e circulator for the boiler must be sized to overcome the
head loss of the boiler and the heating system in order to achieve the
required temperature rise. If the system contains hydronic antifreeze
this must be considered when sizing the pump. Th e temperature rise
across the boiler must never exceed 100°F (55.6°C).
Boiler pressure drop
Assume a pressure drop of:
1.9 feet w.c. (0.7 meter) for a fl ow rate of up to 18 GPM (68 LPM).
7.5 feet w.c. (2.3 meters) for a fl ow rate of up to 36 GPM (136 LPM).
Maintain boiler fl ow rate between 2 GPM and 36 GPM (7.6 to 136 LPM).
Boiler and system circulators
See the following pages for suggested piping for
200i
boilers. All circulators are sup-
plied by the installer, except the factory-installed postpurge circulator.
Boiler circulator
— the circulator that fl ows water through the boiler.
System circulator
— the circulator that fl ows water through the system, but not
through the boiler.
Boiler/system circulator
— a circulator that fl ows water through the boiler and
the system.
Circulator activation
See section 7 of this manual and the
200i
Control manual for instructions on wiring
boiler and system circulators.
Th
e
200i
SmartCycle Control provides an isolated contact to operate the
boiler circulator
(or boiler/system circulator).
Th e
system circulator
must be activated by a relay supplied by the installer. Th is relay
is usually activated by the system control or thermostat.
Additional controls
Local codes or job specifi cations may require the use of additional controls, such as low
water cut-off s, fl ow switches, and high limit controls. Refer to the
200i
Control manual
for electrical connections for auxiliary controls.
Follow the guidelines below to install typical controls in the piping.
Low water cut-off
When the boiler is installed above terminal units, or when required by applicable
codes, install a low water cut-off in the piping above the boiler. See suggested piping in
the diagrams in this section.
Use a probe-type control when possible.
Flow switch
When a fl ow switch is required, install the switch in a section of the piping that will
ensure enough fl ow to operate the switch.
Additional high limit controls
For ASME CSD-1 or Canadian applications, or when required by applicable codes,
install an additional high limit control in the supply piping above the boiler.
Make sure the limit control is set at least 20 °F above the highest operating temperature
of the
200i
boiler.
•
•
Boiler piping connections
Th e boiler supply and return connections are shown in Figure 4.
Both connections are 1¼-inch NPT.
Size piping for the fl ow required. Piping connections to the
200i
boiler should generally be 1¼-inch NPT.
System design
Design options
Th
e
200i
boiler works well in a single or multiple-boiler application
for any type of system. Th e following pages include suggested
piping diagrams for the following system options:
Single boiler, zoning with zone valves (page 13).
Single boiler, zoning with circulators (page 14).
Multiple boilers, primary/secondary piping (page 15).
Multiple boilers, parallel piping, reverse-return (page 16).
Guidelines for chilled water systems (page 17).
All of the piping diagrams show the suggested piping for optional
indirect-fi red DHW tanks. Follow the DHW tank manufacturer’s
instructions for installation and piping. Make sure to size the
DHW circulator and piping to provide the fl ow needed for the
required recovery capacity.
Pipe sizing
Generally install 1¼-inch piping in the boiler circuit. Size system
and other circuit piping based on a 20 °F temperature drop
through the zones. For water-source heat pump systems, the
primary circuit fl ow rate will usually be based on a 5°F temperature
drop. Such high fl ow systems must be piped with the boiler on
a separate loop.
Piping guidelines
Support the piping
— All piping and
components must be supported such that no loads
or stresses are applied to the boiler. Allow for thermal
expansion in the piping design and passageways.
Th e piping diagrams in this manual omit piping
components such as unions. Always install unions
where needed to simplify piping and improve
serviceability.
Circulator requirements
Boiler postpurge circulator
Th e
postpurge circulator
supplied with the
200i
(Figure 4), factory piped between the boiler
supply and return connections, is
NOT
intended
for use in the system. It must remain connected as
supplied. Th e postpurge circulator is only used by
the
200i
for postpurge fl ow to remove residual heat
in the combustion zone. Th e postpurge circulator
includes an integral check valve to prevent by-pass
fl ow during operation.
•
•
•
•
•
5