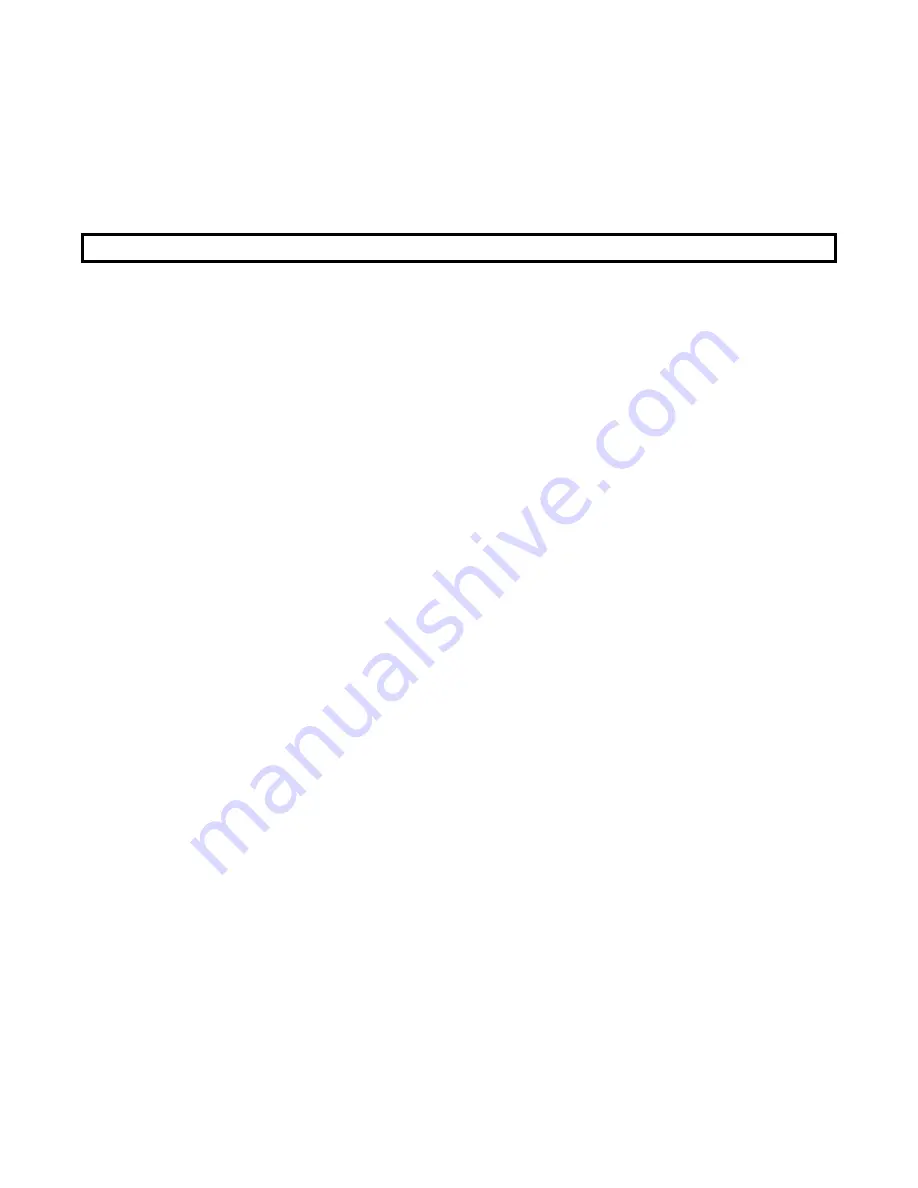
28
8)
Verify that each boom valve operates and that no nozzles are plugged by operating
the BOOM ON/OFF switches.
9)
Place all BOOM ON/OFF switches to ON.
10)
Hold the FLOW CONTROL switch to INC position for approximately 12 seconds. This
assures motorized Control Valve is fully closed. (Pressure gauge is not supplied).
NOTE:
A pressure gauge MUST be installed to properly adjust the system.
11)
Adjust agitator line hand valve for desired agitation.
12)
Close the main line hand valve, if necessary, to set the desired maximum
operating pressure. Maximum pressure should be approximately 10 psi [70 kPa] above
normal spraying pressure.
EXAMPLE:
If normal spraying pressure is 30 psi [210kPa], set maximum pressure at
approximately 40 psi [280 kPa].
13)
Hold the FLOW CONTROL switch to DEC position for approximately 12 seconds. This
assures motorized Control Valve is fully open.
14)
Close by-pass #1 hand valve to set the desired minimum operating pressure. Minimum
pressure should be approximately one half the normal spraying pressure.
EXAMPLE:
If normal spraying pressure is 30 psi [210 kPa], set minimum pressure
at approximately 15 psi [105 kPa].
15)
Verify maximum and minimum pressures and RATE by repeating Steps 10 and 13.
INITIAL SYSTEM FIELD TEST
1)
Drive down field or road at target speed with sprayer booms OFF, to verify SPEED
readout on Console.
2)
Turn on sprayer and booms and place the OFF/MAN/AUTO switch to AUTO. Increase
or decrease speed by one (1) MPH [2 km/h]. The system should automatically correct
to the target application rate.
3)
If for any reason, the system is unable to correct to the desired RATE, check for
an empty tank, a plugged line, a malfunctioning pump, improper vehicle speed or
a defect in the system.
4)
If the system does not appear to be correcting properly, first review INITIAL
SYSTEM SET-UP, then refer to TROUBLESHOOTING GUIDE.
5)
At the end of each row, switch the MASTER ON/OFF switch to OFF to shut off flow.
This also shuts off the area totalizer.
6)
Verify area covered and volume used.