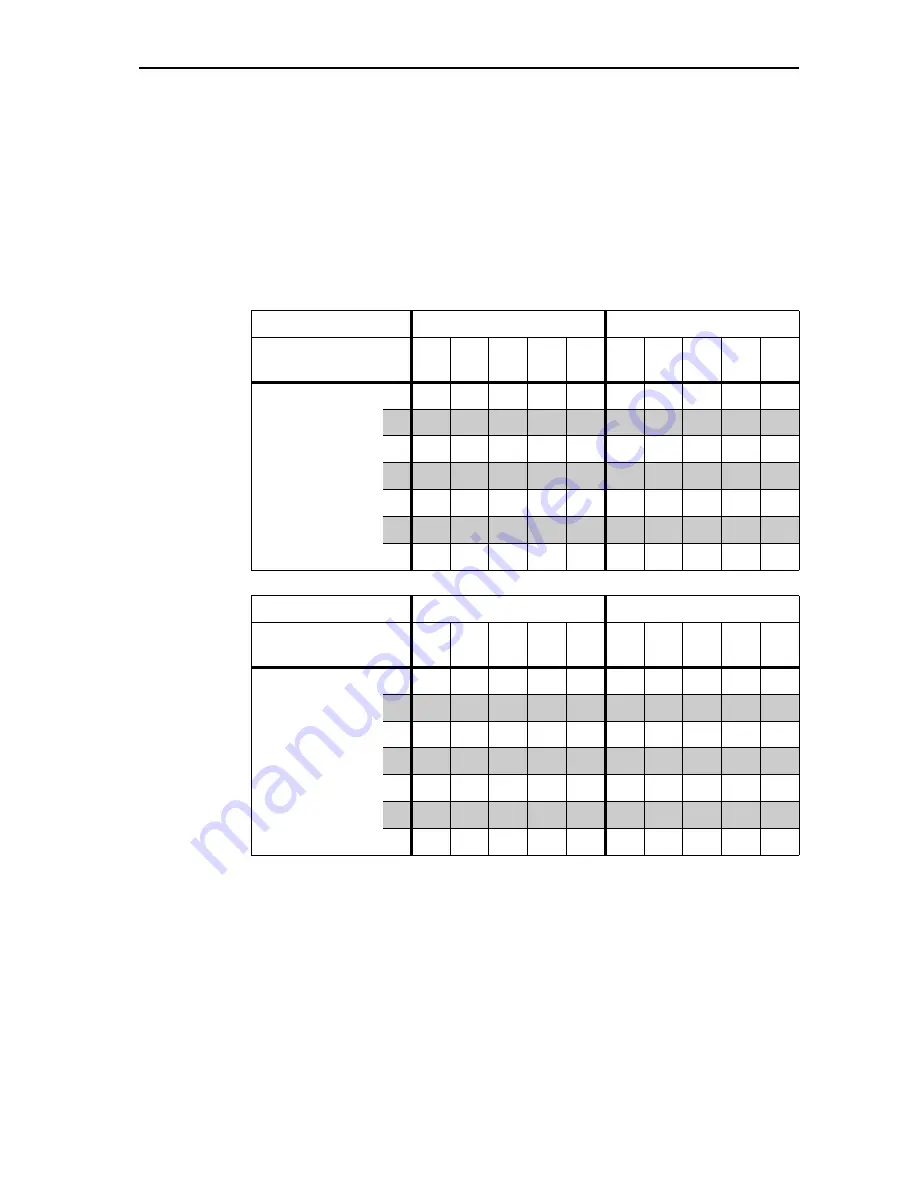
Machine adjustments
59
7
7.7.4
Fertiliser chart for rock salt
Adjustment values for the
metering slider end stop
:
PTO speed: n =
540
rpm
Spreading disc speed: 230 rpm
Drop point
F
Flow factor: 1.22
Hopper height:
B = 33
cm
Agitator type: RWK AX 220
One-sided delivery slider:
0
Spreading width [m]
1
2
Spreading density
[g/m
2
]
5
10
20
30
40
5
10
20
30
40
Speed [km/h]
3
–
–
–
–
–
–
–
–
–
10
6
–
–
–
–
10
–
–
10 10,5 11,5
10
–
–
9
10,5 11,5
–
–
11,5 12,5 13,5
15
–
–
10 11,5 12,5
–
10 12,5 14,5 16
20
–
–
11 12,5 13,5
–
11 13,5 16
18
25
–
10,5 11,5 13,5 15 10,5 11,5 15 17,5 20
30
–
11 12,5 14,5 16
11 12,5 16
19
22
Spreading width [m]
3
4
Spreading density
[g/m
2
]
5
10
20
30
40
5
10
20
30
40
Speed [km/h]
3
–
–
–
10,5 11
–
–
10
11 11,5
6
–
–
10,5 12 13,5
–
10 11,5 13,5 15
10
–
10,5 12,5 14,5 16
–
11,5 13,5 16
18
15 10 11,5 14,5 17
19
10 12,5 16
19
22
20 10,5 12,5 16
19
22
11 13,5 18
22 25,5
25 11 13,5 17,5 21
25 11,5 15
20
25 27,5
30 11,5 14,5 19
23 26,5 12,5 16
22 26,5 29,5
Summary of Contents for 18.1
Page 30: ...Machine data 4 24...
Page 32: ...Transport without tractor 5 26...
Page 108: ...Service and maintenance 9 102...