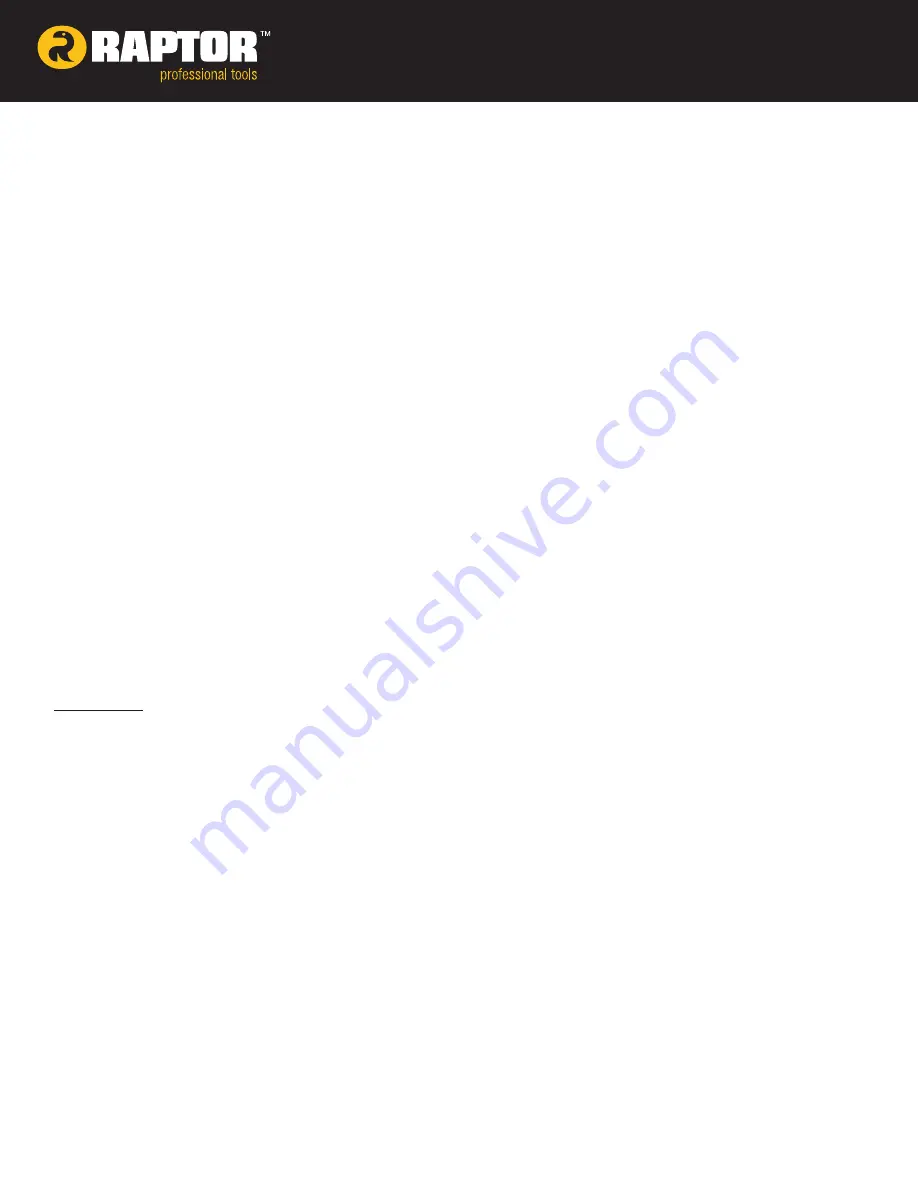
The display will ask for the welding cable to be connected to the fitting. When this has been done it will show the data logging options (if
selected). Enter the information as required.
(Optional extended traceabililty) If selected, the unit will prompt for the extended traceability codes to be read from the fitting. Up to five codes
can be read from fittings, pipes and accessories. When complete, press the A Quick-Key to continue.
The display will ask for the fusion bar code to be read. When this has been done the display will show the set welding parameters.
Press Start to begin welding. During the weld, the display will show the set welding time, the remaining welding time, the set welding voltage
and the welding power generated in the fitting. The unit will also monitor the welding to make sure it does not go out of limits. Any faults that
are detected will terminate the welding and cause an error message to be displayed. These are listed later on in this manual.
(Optional cooling time) At the end of the weld the cooling time will be shown. This counts upwards from zero and will continue until stopped
by the operator. This is shown as an aid to the operator to allow them to know how long it was since the weld finished. Press any key to
continue.
The display will ask for the welding cable to be disconnected from the fitting. Doing this will reset the unit back to the welding menu.
FUsIOn OPERATOR bADgE
To allow full traceability of the operator, and stop untrained people using the equipment, an Operator Badge system is available.
Using an approved training centre, the operator is trained on the correct use of the equipment and then issued with an operator badge that
has his details encoded on it. When the welding unit is switched on, the operator badge must be read with the bar code pen (or scanner) to
unlock the unit and allow welding to take place. Details from the operator badge are recorded in the data log memory.
Three standard modes of operation are available:
1. Every Day.
The first time the welding unit is used every day, the operator badge must be read. This will unlock the unit for use all day and will
then automatically relock at midnight (even if the unit is not powered on). It can also be relocked by reading the operator badge again.
2. Every Power.
Every time the welding unit is switched on, the operator badge must be read to unlock the unit. It will remain unlocked until switched off.
3. Every Weld.
Every time a weld is carried out, the operator badge must be read to unlock the unit This is required even if the unit is not powered off.
To activate these modes of operation, please contact your approved service agent.
Friatec Fittings.
This unit is approved to weld the Friatec Large Diameter couplers, manufactured by Friatec, only when used with the Friatec Operator Badge
system.
To maintain the Friatec warranty, the installer must be trained by an authorized agent and be issued with a Friatec Operator Badge. Only
trained operators should install these fittings.
gPs lOCATIOn
The welding unit has the ability to record the GPS satellite location of the weld. This is stored as Northing’s and Easting’s and entered into
the data log along with an optional depth.
Using a hand held GPS device, the location of the weld can be found, and then this is entered into the data log memory along with the
operator name, location and information
To activate these modes of operation, please contact your approved service agent.
lOW TEMPERATURE OPERATIOn
The welding unit has an extended temperature range option, which allows it to work down to -40°F. This unit has special supply and welding
cables that remain flexible at extremely low temperatures. It also has an internal case heater to warm the electronics to an acceptable
working temperature.
When the temperature inside the unit is below 5°F, the following operation will apply:
8