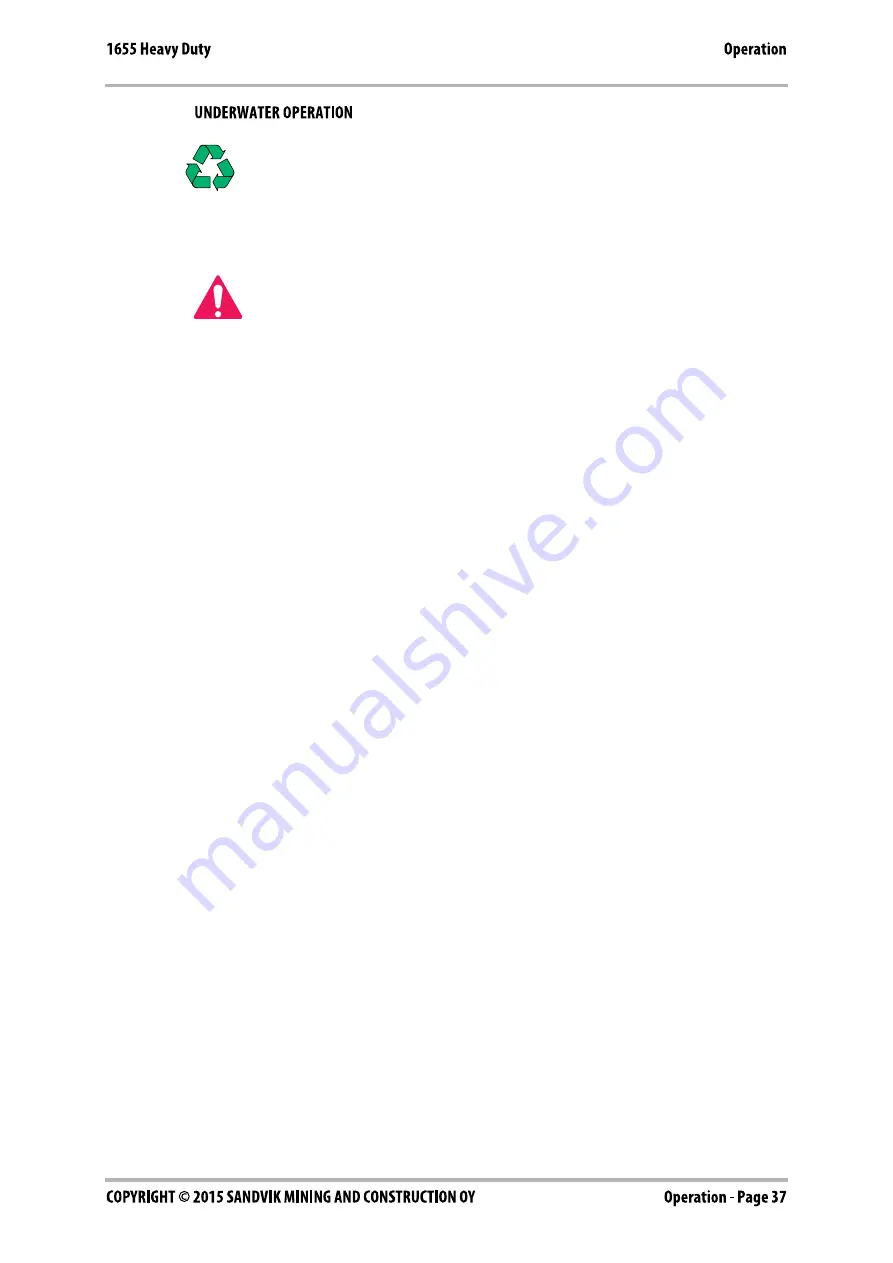
Use environmental friendly oil and tool grease when you are using the hammer
under water.
Warning! If you are using the hammer under water, protect yourself and your
surroundings against compressed water/air spray and possible broken
compressed air hoses.
Warning! If you are using the hammer under water, check the stability of the
carrier and the hammer. Water gets inside the hammer, causing it to weigh
more. Due to the added water weight, lift the hammer carefully out of the
water.
The hammer as a standard assembly, must not be used under water. If water
fills the space where the piston strikes the tool, a strong pressure wave is
generated and the hammer may be damaged.
The latest hammer models can be modified for underwater operations for only short
periods. The operating principle in underwater hammering is to conduct pressurized
air through a built-in channel to the spaces above and below the piston. The air
pressure prevents water entering the hammer. The hammer as a standard assembly,
must not be used under water. If water fills the space where the piston strikes the
tool, a strong pressure wave is generated and the hammer may be damaged.
The wear resistance of the hammer parts is considerably lower under water than in
normal use. This is caused by corrosion and by the abrasive effect of mud in water.
After starting underwater hammering, the hammer must be inspected regularly, for
example after every half hour operation. Adapt the inspection intervals to the
working conditions. See “Maintenance intervals in underwater use” on page 54.
In underwater applications, the productivity of a hydraulic hammer is considerably
lower than in normal work. This is caused by:
1. The breaking object is not visible to the operator. This causes misalignment
between the tool and the object and unnecessary idle strokes.
2. The hammer must be inspected and greased more often than in normal
situations.
3. The hammer must always be completely serviced after working on underwater
job sites.