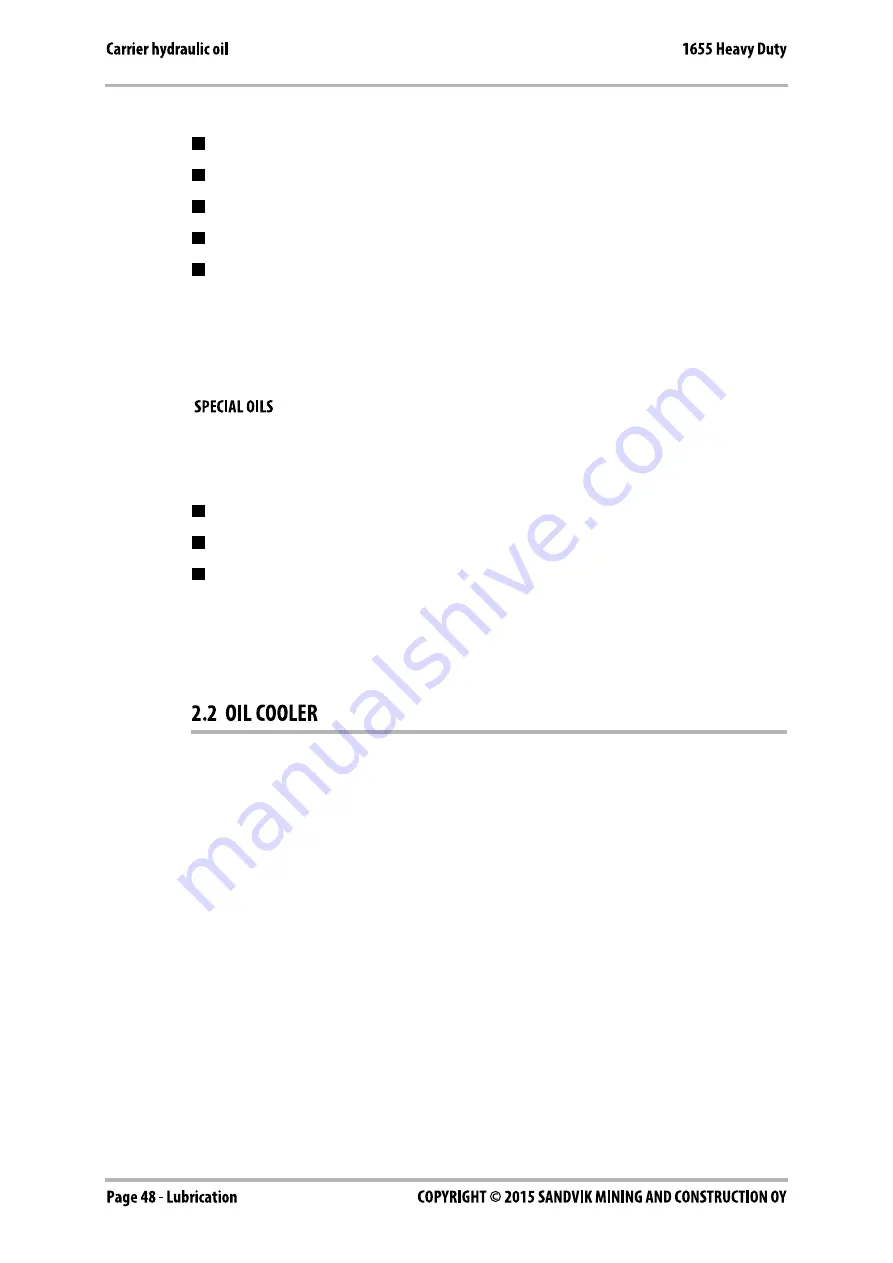
Oil too thin
Efficiency losses (internal leaks)
Damage to gaskets and seals, leaks
Accelerated wearing of parts, because of decreased lubrication efficiency
Hammer strikes irregularly and slowly
Danger of cavitation in pumps and in the hydraulic hammer
Note: We strongly recommend the use of different hydraulic oils in the summer and
in the winter if there is an average temperature difference of more than 35 °C (63
°F). The correct hydraulic oil viscosity is thus ensured.
In some cases special oils (for example biological oils and non-inflammable oils)
can be used with hydraulic hammers. Observe the following aspects when
considering the use of special oils:
The viscosity range in the special oil must be in the given range (20-1000 cSt)
The lubrication properties must be sufficient
The corrosion resistance properties must be good enough
Note: Although a special oil could be used in the carrier, always check its suitability
with the hammer due to high piston speed of the hammer. Contact the oil
manufacturer or your local dealer for more information about special oils.
The correct place to connect the hammer return line is between the oil cooler and
the main filters. The hammer return line should not be connected before the oil
cooler. Routing the hammer return flow through the cooler, might damage either the
cooler, due to pulsating flow, or the hammer, due to increased back pressure.
The carrier hydraulic system must be able to maintain the temperature within an
acceptable level during the hammer operation. This is for two reasons.
1. Seals, wipers, membranes and other parts manufactured from the corresponding
materials can normally stand temperatures up to 80 °C (176 °F).
2. The higher the temperature is, the less viscous the oil gets thus losing its
capability to lubricate.