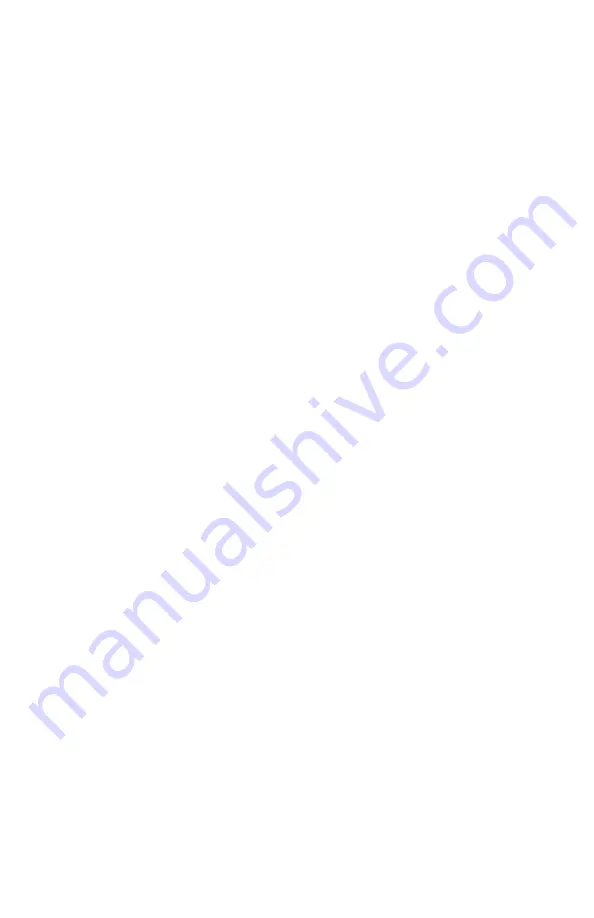
————————————————————
#1 SANITATION AND FILTER
CHANGE PROCEDURE
To sterilize the boiler and chiller system
and change filter at service intervals use
the following procedure.
NOTE:
Should tests for micro-organisms
reveal high colony counts from the chiller,
run this santisation application whenever
required, at all service intervals and with
every installation. For installers you may
to choose to chlorinate Chillers before
delivery to site for additional contact time
thereby eliminating bug counts.
Isolate the water running to the 553-B
Run chilled and boiling water at the
tap to ensure no water is coming out
Unscrew stainless steel filter housing
taking care not to spill the water as it
comes loose. (use a cloth) Carefully
unscrew the filter attached inside by
unscrewing the plastic rim.
Pour out the water and remove the
filter – then add some water and add
a capful or two of Milton sterilising
fluid or chlorine so that you have a
5ppm dilution approx.
Refit the housing to the system and
activate the water supply.
Run the water through the boiling
chilled and sparkling function until
you can smell chlorine in the water.
Isolate water, runoff pressure through
chilled / boiling function then remove
the stainless housing again.
Half-empty the water and insert the
F-PRO Block carbon filter (remove
wrapper) into the housing so it bobs
up and sticks out of the top.
Offer the housing back up to the
filter head so that the filter lines up
with the internal thread.
Holding the filter by the top rim only
(not the carbon) carefully screw it up
into its socket and tighten using
fingers only
Now refit the filter housing carefully
until hand tight.
Ideally you will leave the chlorine in
the chiller unit for a good 15 minutes
before flushing through
When ready switch the water supply
back on and run off a few glasses
through the chiller until it clears.
Repeat with the boiler and carbonator.
A residual taste isn’t a bad thing – it
will disappear after a few glasses of
water but will maintain a sanitising
effect
1
2
3
4
5
6
7
8
9
10
11
12
13
14
15
S A N I T A T I O N A N D F I L T E R