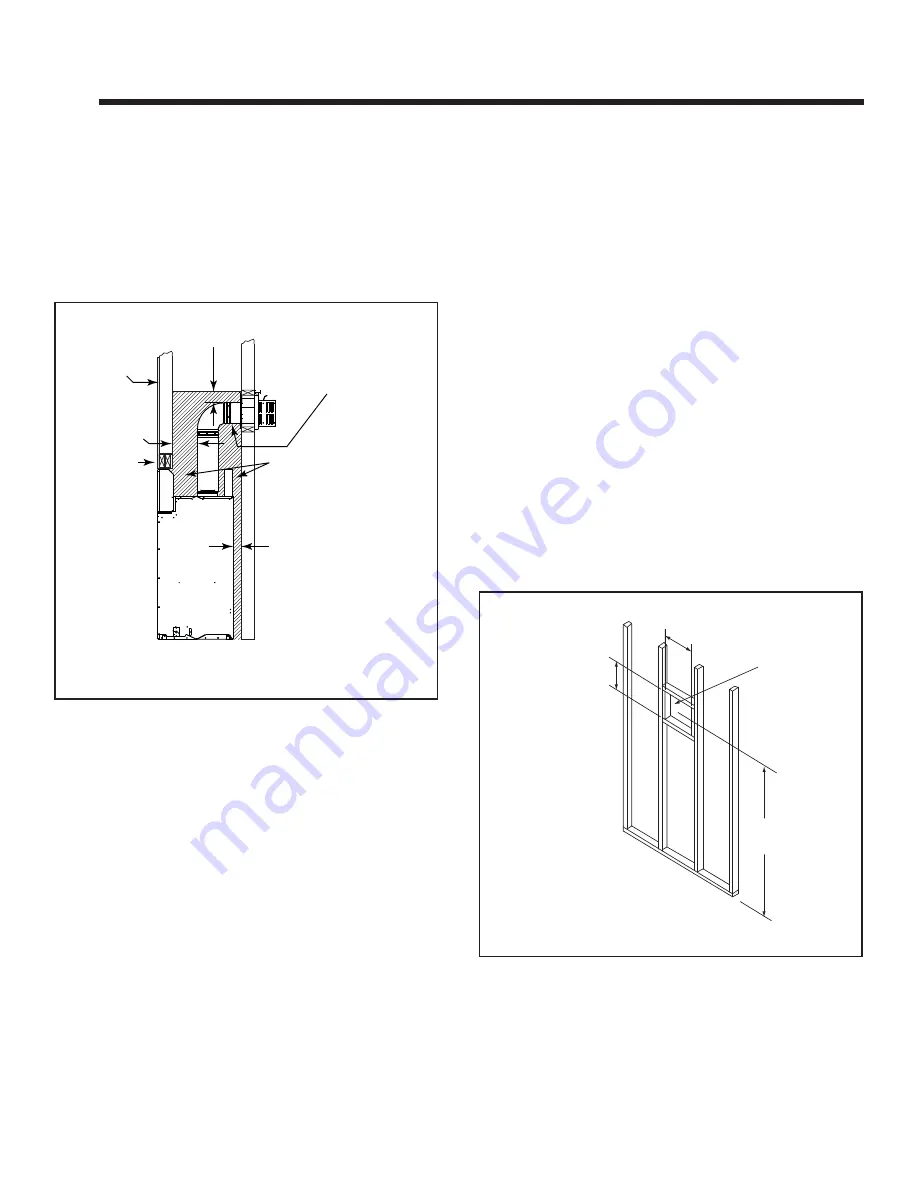
Quadra-Fire • QFP44 • 4051-300 • Rev. U • 4/11
33
No combustible
framing to be
located within
shaded area.
1-1/2 in. (13 mm)
minimum to
perpendicular
wall.
WA
L
L
2 x 4 or
2 x 6
header
Drywall
3 in.
(76 mm)
1 in. (25 mm)
minimum
Air space clearance to
bottom and sides of
horizontal pipe must be
at least 1 in. (25 mm)
Framing should be
constructed of 2 X 4
lumber or heavier.
The center of the
framing hole is
1 in. [25 mm] above
the center of the
horizontal vent pipe.
Vent
framing
hole.
102-1/2 in.
(2604 mm)*
* Center of pipe
10 in.
(254 mm)
12 in.
(305 mm)
A. Pipe Clearances to Combustibles
WARNING! Risk of Fire!
Maintain air space clearance to
vent. DO NOT pack insulation or other combustibles:
• Between
ceiling
fi restops
• Between wall shield fi restops
• Around vent system
Failure to keep insulation or other material away from
vent pipe may cause over heating and fi re.
8
8
Vent Clearances and Framing
B. Wall Penetration Framing
Combustible Wall Penetration
Whenever a combustible wall is penetrated, you must
frame a hole for the wall shield fi restop(s). The wall shield
fi restop maintains minimum clearances and prevents cold
air infi ltration.
• The opening must be framed on all four sides using the
same size framing materials as those used in the wall
construction.
• A wall shield fi restop is required on one side only on
interior walls. If your local inspector requires a wall shield
fi restop on both sides, then both wall shield fi restops
must have a heat shield attached to them.
• See Section 10.I. for information for regarding the
installation of a horizontal termination cap.
Figure 8.2 Wall Penetration
Figure 8.1 Horizontal Venting Clearances To Combustible Materi-
als
Non-Combustible Wall Penetration
If the hole being penetrated is surrounded by non-combus-
tible materials such as concrete, a hole with diameter one
inch greater than the pipe is acceptable.
Whenever a non-combustible wall is penetrated, the wall
shield fi restop is only required on one side and no heat
shield is necessary.