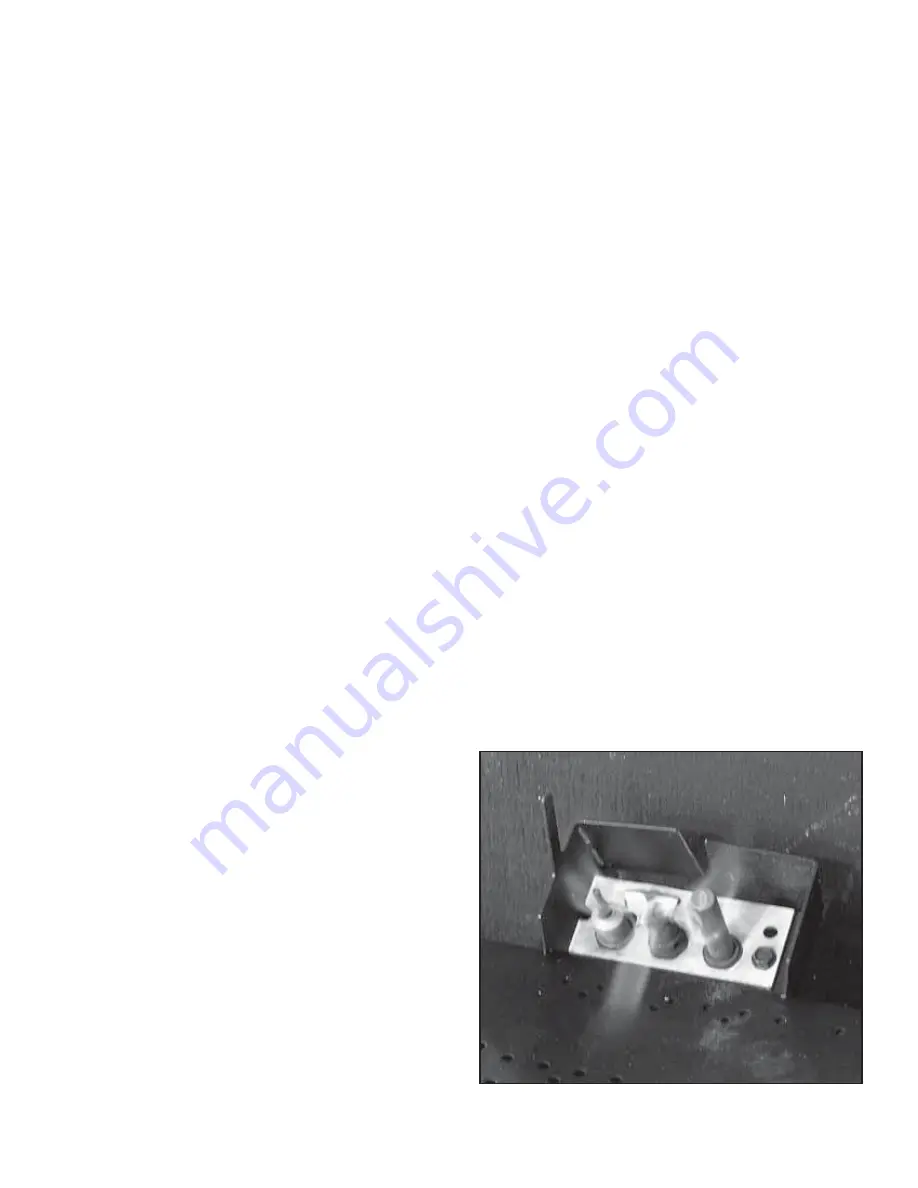
Quadra-Fire • QFP44 • 4051-300 • Rev. U • 4/11
20
Control Compartment and Firebox Top
Frequency:
Annually
By:
Qualifi ed Service Technician
Tools
needed
: Protective gloves, vacuum cleaner, dust
cloths
• Vacuum and wipe out dust, cobwebs, debris or pet hair.
Use caution when cleaning these areas. Screw tips that
have penetrated the sheet metal are sharp and should
be avoided.
• Remove all foreign objects.
• Verify unobstructed air circulation.
B. Maintenance Tasks-Qualifi ed Service
Technician
The following tasks must be performed by a qualifi ed
service technician.
Logs
Frequency:
Annually
By:
Qualifi ed Service Technician
Tools
needed
: Protective gloves.
• Inspect for damaged or missing logs. Replace as
necessary. Refer to Section 15.F. for log placement
instructions.
• Verify correct log placement and no fl ame impingement
causing sooting. Correct as necessary.
Firebox
Frequency:
Annually
By:
Qualifi ed Service Technician
Tools
needed
: Protective gloves, sandpaper, steel wool,
cloths, mineral spirits, primer and touch-up paint.
• Inspect for paint condition, warped surfaces, corrosion
or perforation. Sand and repaint as necessary.
• Replace
fi replace if fi rebox has been perforated.
Gasket Seal and Glass Assembly Inspection
Frequency:
Annually
By:
Qualifi ed Service Technician
Tools
needed
: Protective gloves, drop cloth and a stable
work surface.
• Inspect gasket seal and its condition.
• Inspect
fi xed glass assembly for scratches and nicks
that can lead to breakage when exposed to heat.
• Confi rm there is no damage to glass or glass frame.
Replace as necessary.
• Verify
that
fi xed glass assembly is properly retained and
attachment components are intact and not damaged.
Replace as necessary.
Burner Ignition and Operation
Frequency:
Annually
By:
Qualifi ed Service Technician
Tools
needed
: Protective gloves, vacuum cleaner, whisk
broom, fl ashlight, voltmeter, indexed drill bit set, and a
manometer.
• Verify burner is properly secured and aligned with pilot
or igniter.
•
Clean off burner top, inspect for plugged ports, corrosion
or deterioration. Replace burner if necessary.
• Replace rockwool with new dime-size pieces. DO NOT
block ports or obstruct lighting paths. Refer to Section
15.F. for proper rockwool placement.
• Verify batteries have been removed from battery back-
up IPI systems to prevent premature battery failure or
leaking.
• Check for smooth lighting and ignition carryover to all
ports. Verify that there is no ignition delay.
• Inspect for lifting or other fl ame problems.
• Verify air shutter setting is correct. See Section 14.D.
for required air shutter setting. Verify air shutter is clear
of dust and debris.
• Inspect
orifi ce for soot, dirt and corrosion. Verify orifi ce
size is correct. See Service Parts List for proper orifi ce
sizing.
• Verify manifold and inlet pressures. Adjust regulator as
required.
• Inspect
pilot
fl ame pattern and strength. See Figure 3.1
for proper pilot fl ame pattern. Clean or replace orifi ce
spud as necessary.
• Inspect thermocouple/thermopile or IPI fl ame sensing
rod for soot, corrosion and deterioration. Clean with
emery cloth or replace as required.
• Verify thermocouple/thermopile or IPI millivolt output.
Replace as necessary.
Figure 3.1 Standing Pilot Flame Patterns