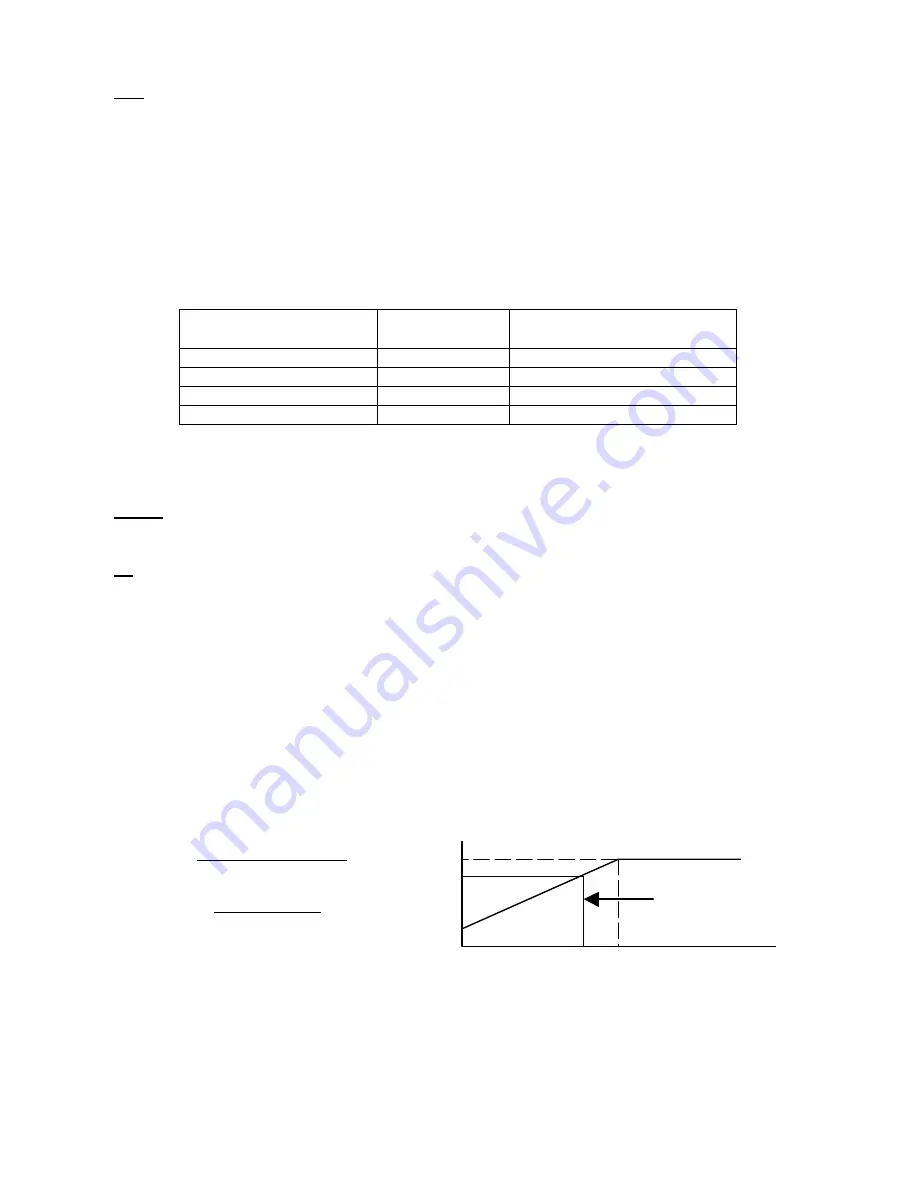
RD3-
RD3 (restart delay three/dry-well recovery timer) can be set from 2-500 minutes or to “A”
to enable the Automatic Dry-Well Recovery Calculator. The RD3 timer causes a restart
delay after an underload (LPR) trip. Setting RD3 to 0 will require a manual reset when
there is a LPR trip.
The Automatic Dry-Well Recovery Calculator allows the Model 777-AccuPower to
automatically select a restart delay based on the run time of the last run cycle. Table 2
shows the next restart delay vs. run time. In general, a longer run time produces a shorter
restart delay. This feature allows the Model 777-AccuPower to optimize running and rest
times automatically.
Run Time
Next Restart
Delay (min)
Starts/Hr
> 1 hr
6
10
30 min. – 59.99 min.
15
4
15 min. – 29.99 min.
30
2
< 15 min.
60
1
Table 2. Automatic Dry-Well Recovery Timer
COMM
- COMM (communications) can be set to OP1 to use the 4-20 mA module or to set the
Modbus address: A01-A99.
FS
-
20 mA
16 mA
4 mA
0 kW
.6
FS (.8)
Example if motor is
running at .6 kW,
Desired mA output - 4
20-4
= X
Running hp/kW
X
= FS
Output
FS (full scale) setting is required when utilizing a 4-20 mA module. PWS should
already be set according to the correct hp/kW operating range of the motor; this will
automatically establish the range for FS. Set FS according to the desired mA output.
The module output, 4-20 mA, is directly proportional to the shaft power of the motor.
A 4 mA output is always given when shaft power is zero and 20 mA when shaft
power equals FS.
If a motor is running at .6 kW, PWS should be 1 (0.01-0.99 kW). To give 20 mA
output when the motor is running at .6 kW, set FS to .6. The relationship of shaft
power to output current is linear until the FS setpoint; shaft power usage above FS
will give 20 mA. If, for example, a 16 mA typical output is desired (to give up to 20
mA if the motor is running at higher kW), set FS to .8
.
Phone: 800.894.0412 - Fax: 888.723.4773 - Web: www.clrwtr.com - Email: [email protected]