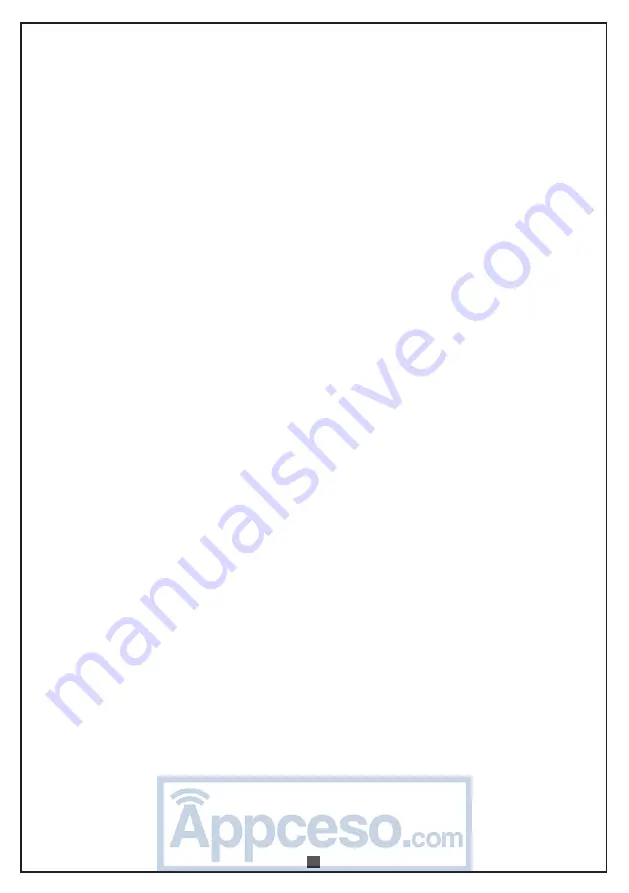
automatismos
pujol
winner DC
english
11
ATTENTION
This actuator can only be installed over drums made of 220 mm pulleys and two bumpers located on the lower area of the
shutter (Image 2)
Junior DC 24 frame model is a special DC frame for this actuator.
Conditions of use:
The Winner DC actuator is intended to be installed on shutter systems that are operated by qualified staff.
The Winner DC actuator has been designed and built to be installed on spring-compensated roll-up shutters according to
the weight limits that are shown on the table of technical specifications. The actuator should not be used on installations
different from the above mentioned ones.
Applicable regulations:
The Winner DC actuator complies with the following European regulations:
Directive CEE/CEEA/CE 23 of 19/02/1973
Directive CEE/CEEA/CE 336 of 03/05/1989
Directive CEE/CEEA/CE 93/68 of 22/07/1993
Besides, the design and manufacture have been made according the following technical standards:
EN 292, parts 1 and 2: Safety of machinery - Basic concepts, general principles for design Basic terminology, methodology.
EN 294: Safety of machinery - Safety distances to prevent danger zones being reached by the upper limbs.
EN 60335-2: Specification of household and similar electrical appliances.
CE marking of Winner DC only refers to the actuator and not to the whole system (actuator, shutter, frames, etc) The installer
is responsible for the CE compliance of the shutter-actuator assembly.
Chapter: Guidelines to avoid accidents during installation:
Connection of the actuator to the power supply should not be performed unless the installation operations described below
are finished. Connection of the actuator should only be done for the sense of rotation test and end of stroke programming
test. The sense of rotation and end of stroke programming tests should be performed with the installer far from the dange-
rous area, keeping a safety distance from the fold zone of the shutter.
Installation specifications
The actuator must be installed in a protected hole so that disassembling would not be possible without special tools. The
protection should prevent contact with the fold zone of the shutter.
The protection is not necessary in installations are higher than 2,7 m. In the case of a man handle drive, the manoeuvre
control should be installed, near to the shutter in such a position that allows its direct and complete view.
In the case of shutters with no element, you must assure there are no fixed structures near to the door that can cause cras-
hing areas.
Photocells or belts will be installed when the current regulation states it.The use of photocells or sensors is mandatory when
two or more centralised driven shutters are installed. Photocells or sensors are also mandatory when the shutter drive is
installed in places where movement area is not under control.
Chapter: Guidelines to avoid accidents during maintenance:
Maintenance must be done only after the reducer is put on safety mode. This is achieved opening the all-pole switch on the
start-up control and ensuring that it cannot be reset during the maintenance operation (closed with key, signals, etc.)
Note for the user: Maintenance or verification of the reducer must be done by qualified staff.
SERIES EQUIPMENT
220 mm pulley plastic cover.Ø 48 mm (or Ø 42 mm) adjustment supplements.Wire, cover and manual release knob.
2 electrical wires joined with a connector. One electrical wire for power and the other one for manoeuvres.
ASSEMBLY INSTRUCTIONS (Images 3, 4, and 5)
The actuator should be installed centred on the shaft, taking into account the position of the engine and the wires output
(Image 3)
Drill 3 holes on the central shaft tube according to image 3), one hole (Ø10.5 mm) is to prevent rotation, another hole (Ø15
mm) for the wires and the last hole (Ø10 mm) for the electro-brake wire and cover.
The pulley is fixed with 2 M8x25 screws. Remove the screws to move the pulley (Image 4) using a 6mm Allen key.
Remove the roller bearing with care and put it into a clean area.
There are 4 screws. Tight the screws to separate the flange support. Use a 6 mm Allen key.
Couple the engine body to the tube of the door and tight the screws to put the flange support again.
If the tube diameter is different from Ø 60 mm, use the Ø 48 (ó Ø 42) mm adapter.
Fully screw the M10x40 hexagonal screw to make it enter in the Ø 10.5 mm hole drilled as indicated in the above steps. Insert
the bearing in its housing.
Couple the pieces again to put the pulley. Tight the screws firmly.
Make sure the supplement of the drum is properly located.
Screw the M10x40 screw until the tube is pressed. Screw the nut to lock it.The actuator should be properly fixed and aligned.
In order to assemble the manual unlocking device, insert the cover and unlocking cable into the door’s tube through the Ø
10 mm hole. The wire should not have steep curves.
https://appceso.com