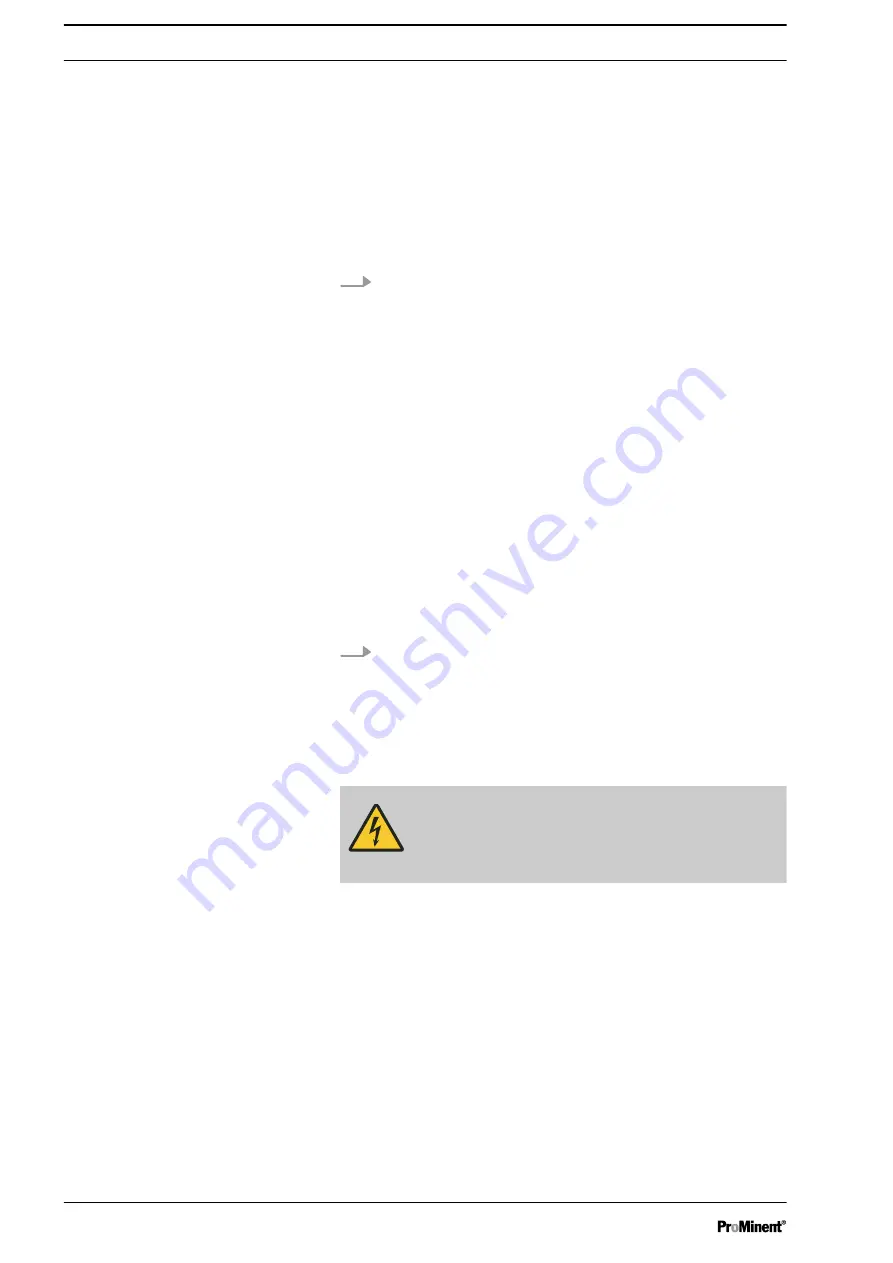
The relays alarm 1 and alarm 2 are mechanical relays with a nom‐
inal voltage of 120 ... 240 V AC 2 A.
Note that the relays are labelled NO (Normally Open), NC (Nor‐
mally Closed) and C (Common).
In its normal status, the DULCO turb C is supplied with power and
does not trigger an alarm. The operation of these alarms is handed
in the “Alarms” chapter
The connectors are labelled under the large terminal strip. These
connectors are located in the top row.
To open the connector, insert a 3 mm (1/8 inch) slotted head
screwdriver into the slot directly above the electrical con‐
nector.
Open the terminal block connection by gently lifting the
screwdriver upwards. The connection is tightened by pulling
out the screwdriver.
The digital RS-485 half-duplex interface (2-core) works with differ‐
ential levels which are insensitive to electrical faults. Cable lengths
of up to 900 metres (3000 ft.) are possible.
The last device on each bus must be connected with a 120 Ohm
resistor to avoid signal reflections on the line.
Do not route the RS-485 cable in the same cable duct as the
power supply.
Make sure that the power supply is disconnected before making
the connections to avoid damage to the device.
The connectors are labelled under the large terminal block. These
connectors are located on the left side in the bottom row.
To open the connector, insert a 3 mm (1/8 inch) slotted head
screwdriver into the slot directly above the electrical con‐
nector.
Open the terminal block connection by gently lifting the
screwdriver upwards. The connection is tightened by pulling
out the screwdriver.
DANGER!
Make sure that the DULCO turb C is disconnected
and de-energised before connecting the 4 ... 20
mA cable.
The 4 ... 20 mA output is fed by a 24 V DC current source and can
control loads of up to 1000 Ohms.
This 4 ... 20 mA output is insulated from the supply voltage and the
earth wire.
Do not route 4 ... 20 mA cables in the same cable duct as the
power supply.
The connectors are labelled under the large terminal block. These
connectors are located on the right side in the bottom row.
Alarm and I/O connectors.
RS-485/Modbus connector
4 ... 20 mA connector
Assembly and installation
22