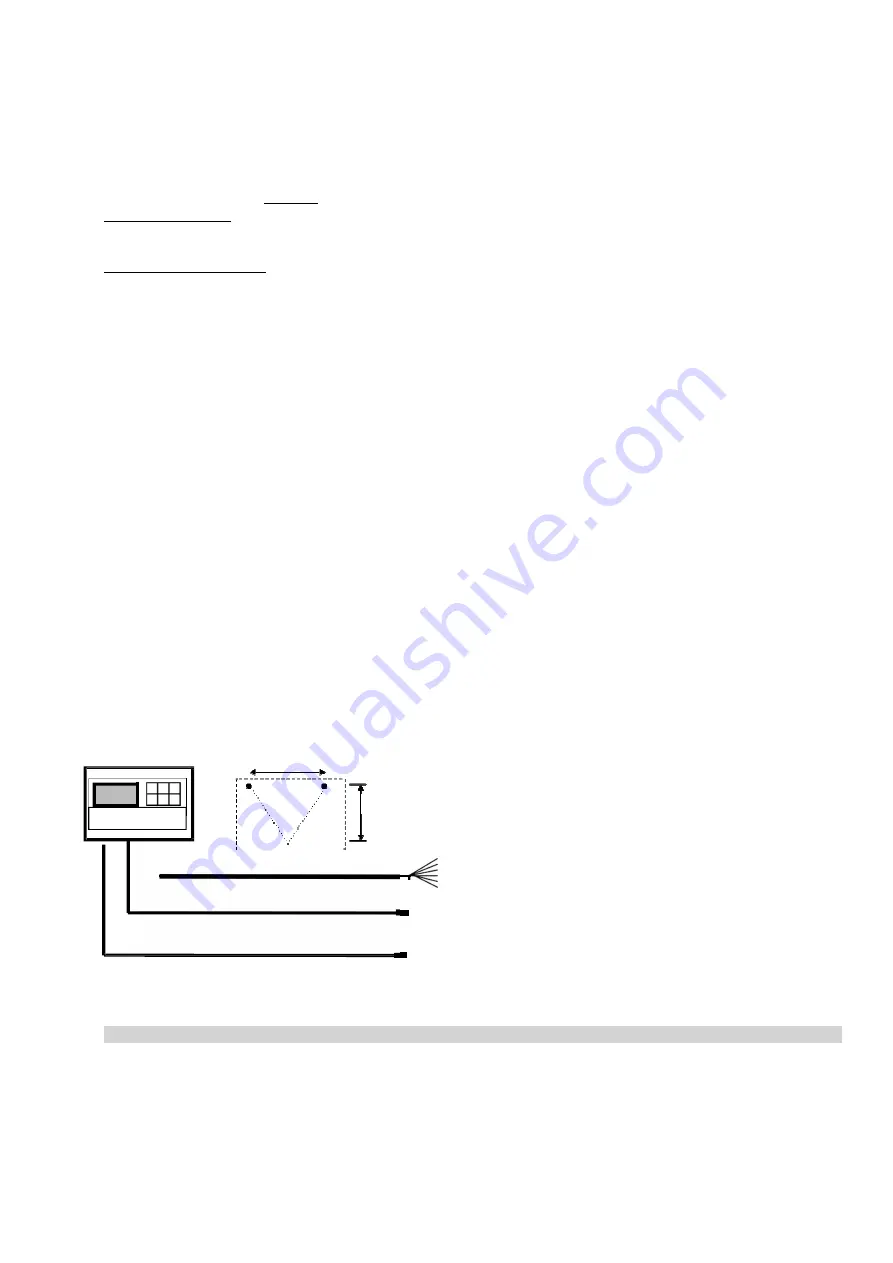
27/61
-
power
circuit:
400V/3/50Hz
+
Earth
-
control
circuit:
230V/1/50Hz
(pressure
switches
–
crankcase
heaters).
Neutral
is
not
compulsory,
as
230V
voltage
is
produced
with
the
400V/230V
transformer.
Electrical
motor
wiring
Electrical
motors for compressors
These
are
designed
for
a
direct
start.
The
compressor
motors
are
fitted
with
an
anti-short
cycle
mechanism
allowing
a
maximum
of
6
start-ups
per
hour.
Electrical motors of condenser
Models
equipped
with
355,
450
and
500
mm
diameter
fan-motors
(plastic
fans)
The
motors
fitted
in
the
condenser
are
triple
phase.
These
must
be
coupled
in
STAR
formation
at
400V
Motor
applications
:
-
Ambient
temperature
-40°C
to
+50°C
-
Hygrometry
from
60
to
98
%
with
purging
holes
-
Insulation
class
F
-
Protection
factor
IP
54
(purging
holes
blocked)
-
Nominal
current
400V
The
motor
protections
must
conform
to
legal
standards
and
calibrated
to
the
nominal
current.
ADDITIONAL
SAFETY
CONTROLS
Safety
Features
The
safety
switches
fitted
to
the
compressors
(HP/LP
pressure
switch
cut
off
the
compressor.
An
internal
Klixon
in
the
star
centre
of
the
motor
stops
it
if
the
coil
temperature
is
too
high;
independently
of
the
control.
Crankcase
heater
These
must
have
a
continuous
power
supply
(self-regulating
PTC
heater)
for
devices
through
to
the
160
model.
Remote
control
The
power
supply
for
the
remote
control
and
crankcase
heaters
is
provided
through
a
transformer.
This
transformer
is
designed
in
the
standard
use
to
supply
the
components
specified
in
the
electrical
diagrams.
Standard
control
The
evaporating
pressure
is
controlled
by
an
LP
pressure
switch
which
acts
on
the
compressor.
ELECTRONIC
REMOTE
CONTROL
Remote
control
for
unit
with
electronic
room
control.
120
100
Cable
12x1.5mm2
Length
6m
Connector
cable
to
condensor
unit
Defrost
sensor
to
be
placed
in
the
evaporator
coil
Temperature
control
sensor
to
be
placed
on
the
air
inlet
of
the
evaporator.
-
START-UP OPERATIONS
PRELIMINARY
CHECKS
AND
OPERATIONS
General
information
Ensure
that
all
the
threads
are
fully
tightened
on
connection
flanges,
flexible
connections
and
cables
as
jolting
during
transport
could
cause
screws
and
bolts
to
loosen.
Check
also,
for
same
reasons,
if
there
are
any
breaks
in
the
piping.
Ensure
that
the
flexible
connections
are
not
in
contact
with
metal
parts.
Vibrations
from
the
compressor
can
cause
wear
in
these
until
they
rupture
at
the
point
of
friction.