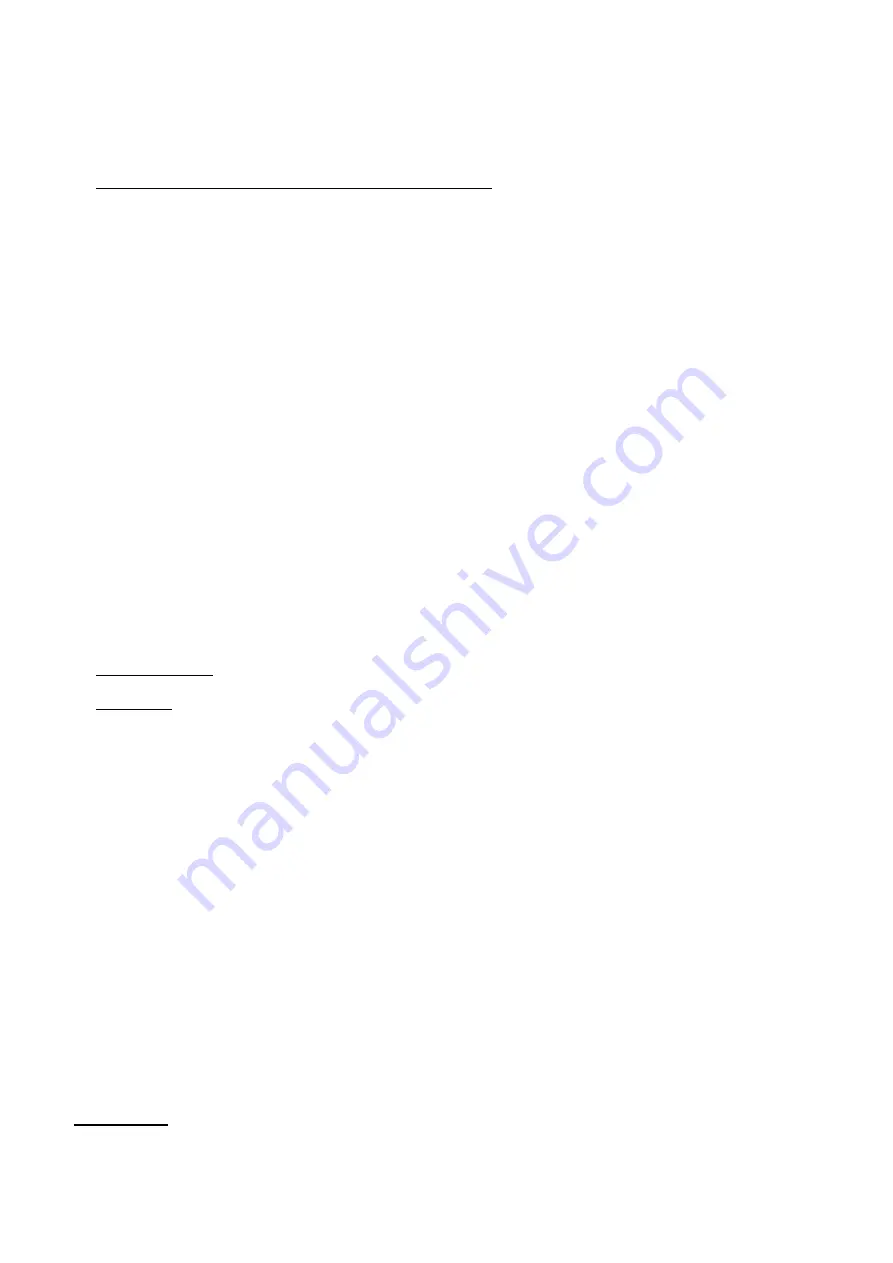
18/21
The charging bottle must remain connected to this valve permanently during the whole start-up period to enable instant adjustment
while charging the installation.
Pre-Setting And Checking of SafetySystems
Test the oil level monitoring type OLCK1 (for compressors fitted with)
Check the time delay :
After compressor start: 90s
In operation 5s
Check the actual cut-off if oil pressure drops.
To carry out this test, remove the compressor safety fuses and switch the Stop-Start switch on the compressor to the Start or
ON position at 230V with zero oil pressure (compressor stopped). Cut off electrical supply for reset.
Pre-set the LP (Low Pressure) pressure switches (following application guideline from manufacturer of compressor) and test
manually. Do not set these below atmospheric pressure.
Pre-Setting And Checking of control systems
Pre-set the LP and HP pressure switches and test manually.
Start-up
of
compressors
-
Open all the valves (compressor suction and discharge in liquid bottle)
-
Place an ammeter on one phase of the compressor
-
Close the power circuit-breaker or the fan motor cut-outs.
-
Start up compressor by switching the on/off switch to on.
The current increases to maximum and must decrease very rapidly. If this does not happen, stop the compressor to check and
find the fault.
Repeat these operations for each compressor.
Remainder of charge
Fill up with the remainder very quickly.
An incomplete charge of fluid will cause considerable superheat and so abnormally high discharge temperatures.
Fan checks
Direction of rotation
Check that the fans are rotating in the correct direction, i.e. drawing on the coil.
Fan operation
The fans cut in/out from the collectors towards the end of the coil.
OPERATING CHECKS
Shortly after start-up, the operating conditions of the equipment must be checked.
The compressor must operate within its acceptable limits
Check on each compressor (with the others shut down):
.
Discharge pressure
.
Oil pressure
.
Measure suction temperature
.
Measure discharge temperature
.
Measure oil temperature on entry into the compressor
The intake superheat must not exceed 20K and should not fall below 11K. Therefore adjust the thermostatic expansion valve and
ensure that the charge in the condensing unit is correct.
The discharge conditions on the discharge tube (with cylinder head fan off) must be within the following range:
. R404
70°C < T° discharge < 100°C
-
The crankcase temperature must not fall below 40°/45°C
-
The maximum temperature of crankcase must not exceed 93°C.
Condenser
Check the voltage absorbed for each fan motor.
Very important:
There is no need to add oil over and above the required quantity during start-up.
Excess oil generally leads to oil slugs on the condensing unit which causes damage to the compressors.