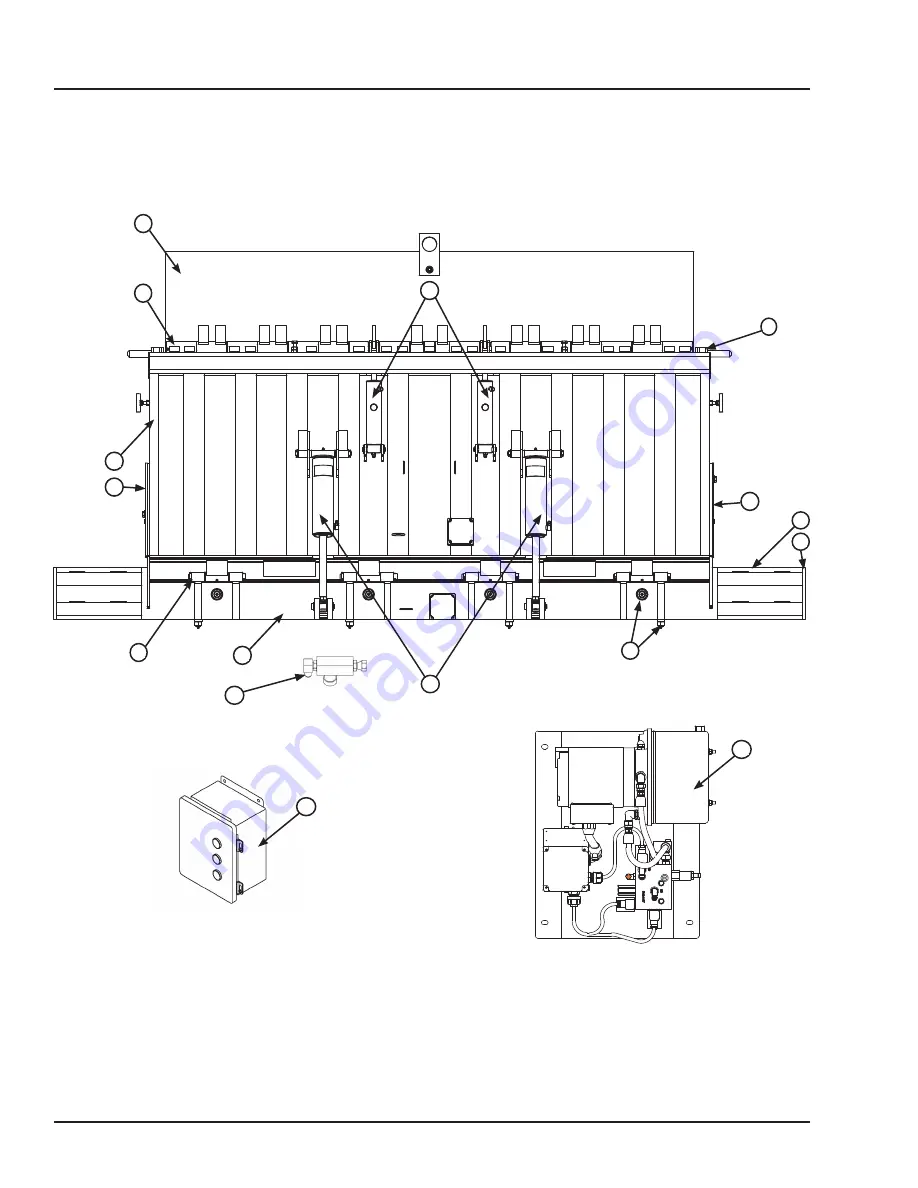
10
4111-0044 — June 2021
© 2021 Systems, LLC
A — Lip
B — Platform
C — Lip Cylinder(s)*
D — Flow Control Valve
E — Platform Cylinder(s)*
F — Lip Hinge Pin
G — Maintenance Props
H — Carriage
J — Cam Followers (bearings)
K — Roller Track
L — Platform Hinge Pin
M — Roller Track Stops
N — Side End Load Support
P — Control Box
Q — Powerpack**
Figure 5
INTRODUCTION
* Models may be equipped with 1 or 2 cylinders.
**Powerpack may be mounted on underside of leveler or remotely. Remote unit shown, see pages 46-48 for Powerpack options.
Component Identification (RCR w/Manual Side Shift)
Inspect package and all components. Report any missing or damaged items immediately
and note on the shipping Bill Of Lading (BOL).
P
TOLERANCES
(UNLESS OTHERWISE NOTED)
FRACTIONAL:
1/32"
DECIMAL:
.00 =
.01"
.000 =
.005"
ANGULAR:
1
MATERIAL
DRAWN BY
CHECKED BY
DRAWING NO.
DATE
MarkS
9/23/2020
170381-ZD0
Side Shift RCR
FINAL ASSEMBLY, RAIL RAMP
P O W E R A M P
M C G U I R E
D L M
S Y S T E M S
L o a d i n g D o c k E q u i p m e n t
This print is the property of Systems, LLC and represents a proprietary article in which Systems, LLC retains any and all
patent and other rights, including exclusive rights of use and/or manufacture and/or sale. Possession of this print does
not convey any permission to reproduce, print or manufacture the article or articles shown therein, such permission to be
granted only by written authorization signed by an officer or other authorized agent of Systems, LLC thereof.
STOCK NO.
EASTERDAY FARMS, 50K
REV A - ECN 18-066
A
B
D
F
G
K
H
M
N
J
L
Q
BILL OF MATERIAL
SIZE
DESCRIPTION
PART NO.
QTY
ITEM
5/16-18 UNC X 3
HEX HEAD CAP SCREW
2101-0077
2
1
8-32 UNC X 3/4
RHMS - SLOTTED
2101-0102
4
2
5/16" DIA
WASHER - FLAT - ZINC PLATED
2101-0163
6
3
5/16-18 UNC X 1
HHCS - GRADE 5
2101-0187
4
4
NUT,FLNG TOP L/N, 5/16-18
2101-0214
6
5
5 X 5 X 3
J-BOX - FIBERGLASS
2751-0042
1
6
CANFIELD CONNECTORS
CABLE ASSY,24"OAL,2 COIL
4305-0264
1
7
CANFIELD CONNECTORS
CABLE ASSY,24"OAL,1 COIL
4305-0306
1
8
1-12G,1-12BK,1-12W
CONDUIT ASSY,4.5"OAL,3,90-90
4305-0601
1
9
3-14BK,1-14G
CONDUIT ASSY,4.5"OAL,4,90-90
4305-0602
1
1-12G,2-12BK
CONDUIT ASSY,4.5"OAL,3,90-90
4305-0603
1
DELTA #39670035,NUT #36202020
COIL,115VAC,DHC-11
8581-0004
3
10
REMOTE-MOUNTED PUMP/MOTOR
VALVE ASSY,VS/RR,RV FLOAT
8585-0103
1
11
& W J-BOX MTG
PPAC MTG WLDT, VS REMOTE W/ VALVE
9394-0049
1
12
1PH,115/230V,1.5HP
PPAC,REM,WALL,2GPM,2.1 GAL
9395-0351
1
13
1PH,115/230V,1.5HP,WASHDOWN
PPAC,REM,WALL,2GPM,2.1 GAL
9395-0352
1
1PH,208V,1.5HP
PPAC,REM,WALL,2GPM,2.1 GAL
9395-0353
1
1PH,208V,1.5HP,WASHDOWN
PPAC,REM,WALL,2GPM,2.1 GAL
9395-0354
1
3PH,460V,1.5HP
PPAC,REM,WALL,2GPM,2.1 GAL
9395-0355
1
3PH,460V,1.5HP,WASHDOWN
PPAC,REM,WALL,2GPM,2.1 GAL
9395-0356
1
3PH,575V,1.5HP
PPAC,REM,WALL,2GPM,2.1 GAL
9395-0357
1
3PH,575V,1.5HP,WASHDOWN
PPAC,REM,WALL,2GPM,2.1 GAL
9395-0358
1
#8 JICF SWIVEL BOTH ENDS
HYD HOSE,3/8"100R17,17.50 LG
9904-0090
2
14
TOLERANCES
(UNLESS OTHERWISE NOTED)
FRACTIONAL:
1/32"
DECIMAL:
.00 =
.01"
.000 =
.005"
ANGULAR:
1
DRAWN BY
CHECKED BY
DRAWING NO.
DATE
JCS
6/10/2020
9396-0051
page 9
PPAC ASSY,VS REM,2 GPM,2.1 GAL
S Y S T E M S, I N C.
L o a d i n g D o c k E q u i p m e n t
P O W E R A M P
M C G U I R E
D L M
This print is the property of Systems, Inc. and represents a proprietary article in which Systems, Inc. retains any and all patent and other rights, including exclusive rights
of use and/or manufacture and/or sale. Possession of this print does not convey any permission to reproduce, print or manufacture the article or articles shown therein,
such permission to be granted only by written authorization signed by an officer or other authorized agent of Systems,Inc. thereof.
WALL MTG,W/ RV FLOAT
- 20-022 6/10/2020
INITIAL RELEASE
NOTES:
1.
ENSURE HYDRAULIC HOSES AND ELECTRICAL
CONDUITS ARE PROPERLY ROUTED TO MEET
THE MINIMUM BEND RADIUS REQUIREMENTS
SPECIFIED BY THE MANUFACTURER. FITTING
POSITION AND HOSE ROUTING MAY DIFFER
FROM WHAT IS SHOWN TO ACCOUNT FOR
THE MINIMUM BEND RADIUS.
C
G
E
Summary of Contents for RCR Series
Page 25: ...23 4111 0044 June 2021 2021 Systems LLC OPERATION This page intentionally left blank ...
Page 38: ...36 4111 0044 June 2021 2021 Systems LLC PARTS Platform Hydraulic Hoses C A G F E D B H ...
Page 58: ...56 4111 0044 June 2021 2021 Systems LLC This page intentionally left blank MISCELLANEOUS ...