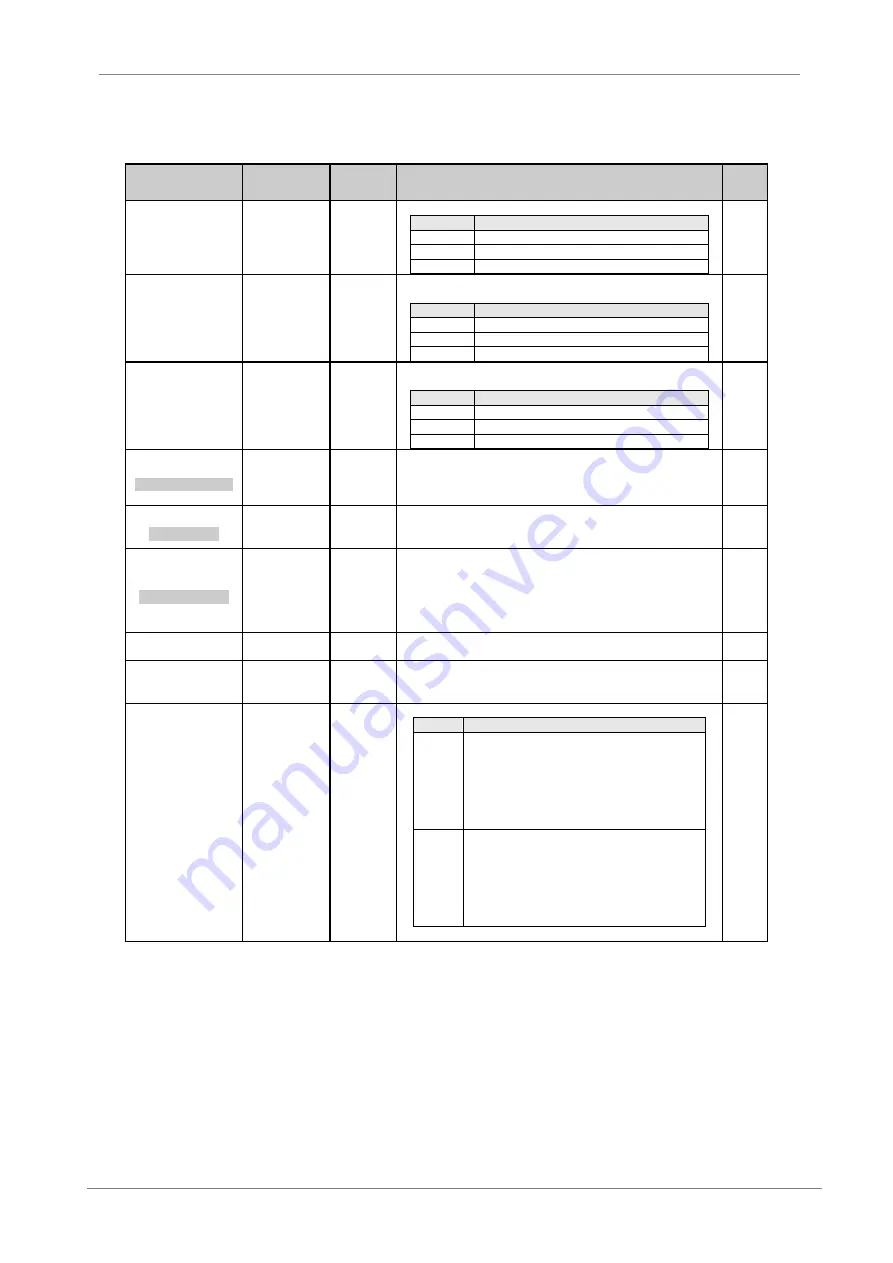
SD700
POWER ELECTRONICS
28
DESCRIPTION OF PROGRAMMING PARAMETERS
3.6.8.
Subgroup 25.2 – S25.2: PID Setting
Parameter
Name /
Description
Range
Function
Set on
RUN
1 PID SETP=LOCAL
G25.2.1
/ PID
setpoint source
LOCAL
AI1
AI2
Selects the input source for the PID setpoint. See the following table:
OPT.
FUNCTION
LOCAL
Reference signal from keypad.
AI1
Reference signal from Analogue Input 1.
AI2
Reference signal from Analogue Input 2.
NO
2 PID aSTP=LOCAL
G25.2.2
/
Alternative PID
setpoint source
LOCAL
AI1
AI2
Selects the input source to introduce the alternative PID setpoint. See the
following table:
OPT.
FUNCTION
LOCAL
Reference signal from keypad.
AI1
Reference signal from Analogue Input 1.
AI2
Reference signal from Analogue Input 2.
NO
3 PID FBK=AI2
G25.2.3
/ PID
feedback source
AI1
AI2
PULSE
Selects the input source for the system feedback signal. See the following
table:
OPT.
FUNCTION
AI1
Feedback signal from Analogue Input 1.
AI2
Feedback signal from Analogue Input 2.
PULSE
Pulses from programmable digital input.
NO
4 PID Kc=1.0
PROPORTIONAL PID
G25.2.4
/
Proportional gain
of PID regulator
0.1 – 20
Allows the user to set the proportional gain value of the PID. If it is
necessary to have a higher control response, then increase this value.
Note:
If this value is increased too much, a higher instability can be
introduced in the system.
NO
5 PID It=5.0s
INTEGRAL PID
G25.2.5
/ Integral
time of PID
regulator
0.1 – 999.9s,
Max.
Allows the user to set the integral time of the PID. If you need a higher
accuracy you should increase this value.
Note:
As this value is increased the system response will slow.
YES
6 PID Dt=0.0s
DIFFERENTIAL PID
G25.2.6
/
Derivation time of
PID regulator
0.0 – 250s
Allows the user to set the derivative time of the PID. A higher system
response can be achieved by increasing this value.
Note:
If this value is increased too much accuracy can be reduced
slightly.
Note:
We recommend do not modify this value since the default setting is
suitable for most pump applications.
YES
7 PID ERR=+xx.x%
G25.2.7
/ Error of
PID regulator
+0 to +100% Displays the difference between the setpoint 'G25.2.1 PID SETP' and the
process feedback signal 'G25.2.3 PID FBK' in percentage.
-
8 ERR=+xx.xxkPa
G25.2.8
/ Error of
PID regulator in
engineering units
+0.0 to +3276
Engin. Units
Displays the difference between the reference 'G25.2.1 PID SETP' and
the process feedback signal 'G25.2.3 PID FBK' in engineering units (Bar,
kPa, m³/s, etc.)
-
9 PID INVERT=N
G25.2.9
/ PID
output inversion
N
Y
It is possible to get an inverse operation of the drive output in PID mode:
OPT.
FUNCTION
N=NO
In this case, the PID response if the feedback
decreases is an increasing of the output speed.
This is the standard setting when the PID is used
for an application of constant pressure control. If
the pressure decreases (feedback) due to a higher
demand, it is required to increase the pump speed
to keep constant the pressure in the system.
Y=YES
In this case, the PID response when the feedback
signal is falling down is a reduction of the output
speed. For example, this operation is typical for a
temperature control by means of PID mode. A
reduction of the temperature (feedback) due to a
lower demand requires that the speed of the fan is
reduced to keep the temperature.
YES
Summary of Contents for SD700 Series
Page 1: ...Variable Speed Drive Application Manual PUMPS...
Page 2: ......
Page 3: ...Variable Speed Drive Application Manual PUMPS Edition March 2011 SD70MTAP01BI Rev B...
Page 4: ...SD700 POWER ELECTRONICS 2...
Page 8: ...SD700 POWER ELECTRONICS 6 INDEX...
Page 61: ......
Page 63: ...www power electronics com...