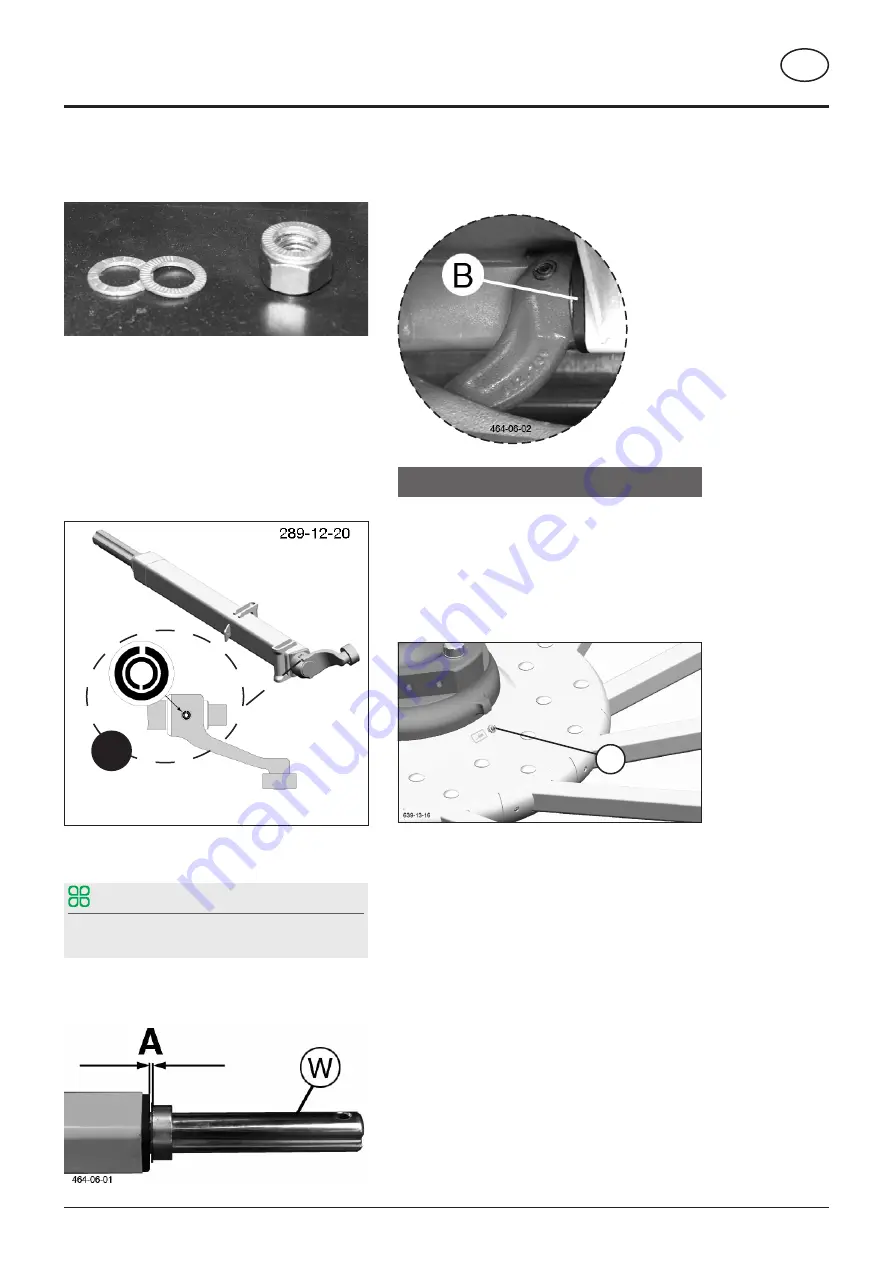
- 42 -
1902-GB Maintenance_2740
mainTenance
EN
- Re-tighten bolts M12x110 with 1x nut and 2x Nordlock
washers (see illus.)
(Tightening torque: 140 Nm)
Lay the Nordlock washers with rough internal milling
on top of one another. This means that both washers
have the fine milling outside.
- Attach cover to the new tine arm, fit it between the
covers and tighten the screw. Tighten all the loosened
bolts (1) for the covers.
- Check the tightness of the bolts and nuts after approx.
50 hours of operation and re-tighten if necessary.
- Pay attention to the position of the dowel pins in relation
to each other. see picture below - Detail B
B
Changing the bearing bush of the tine arms
TIP
Check the shaft (W) at least once a year at distance (A)
from the shaft.
• The distance (A) should be approx. 1 mm in normal
operation. If the shaft (W) clearance is greater, then it
can be corrected with shims.
• If the distance (A) is greater than 4 mm then the bushes
(B) on the inside of the tine arms are to changed.
Otherwise subsequent damage may occur to the
machine.
Rotor unit
lubricating the cam track:
Interval: 50 h
Implementation:
- Put the grease gun on the grease nipple (1)
- Turn the rotor 3-4 times so that the grease is evenly
distributed.
- Pump the grease gun 3-4 times during each rotation
1
Drive of the rotor unit Refill grease
1. Interval:
if needed
The drive of the rotor unit is lubricated for life.
Nevertheless, check once a year whether the cogs still
are covered.
2. Implementation:
1. Open oil filling screw (1). The crown wheel toothing
is easily visible when the filling screw is open.
2. Pour fluid grease in through the filling plug (1) until
the crown wheel is almost completely covered.
3. Close filling screw (1)
4. Distribute the grease by turning on the pto.
5. Check the oil level with the drain plug open. The
crown wheel should be almost completely covered.
6. Continue filling with liquid grease if appropriate, or
reduce the amount of liquid grease via the drain plug
(2).