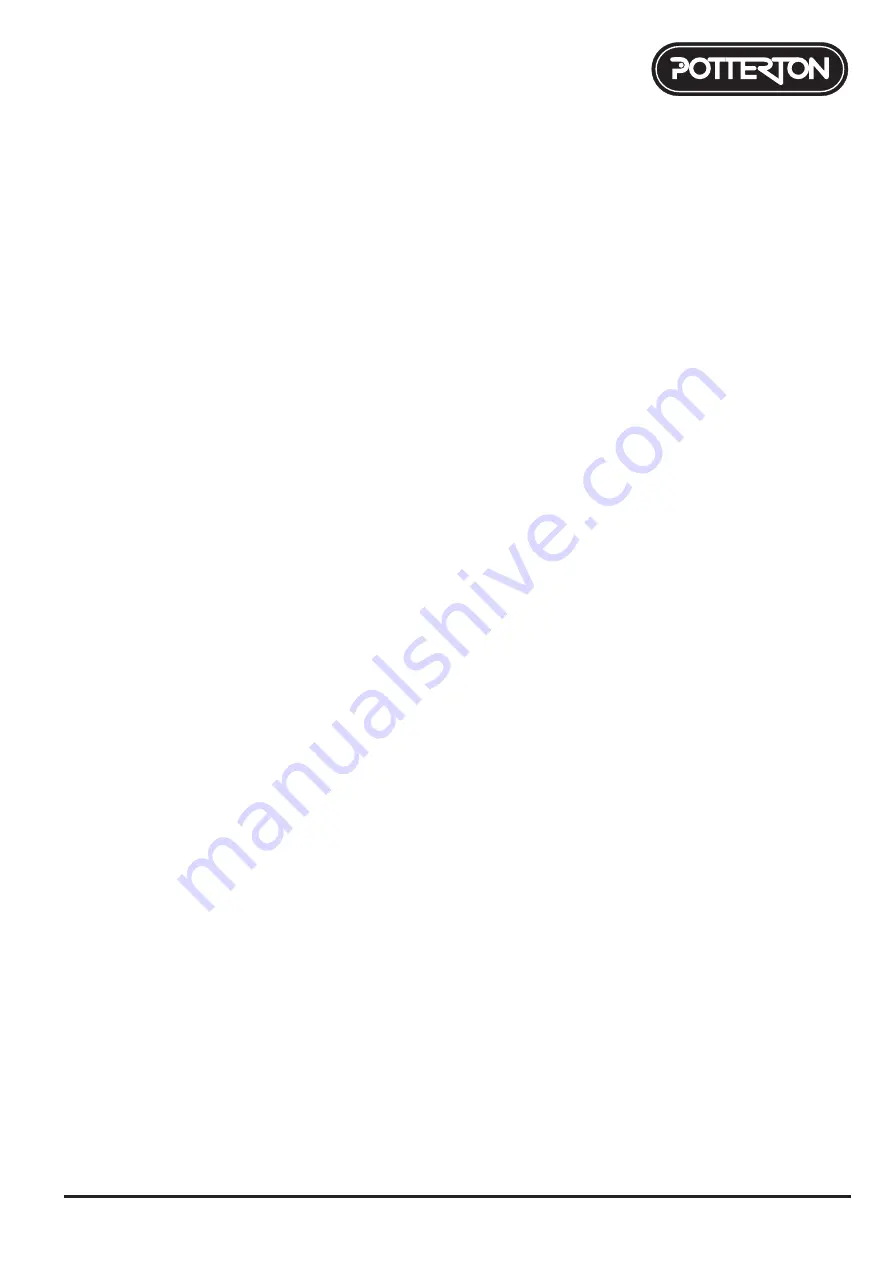
Publication No. 5106228
7
User’s Instructions
Basic Troubleshooting
Boiler not working
•
Are all the gas and water supplies turned on at
the main supply ?
•
Is the electricity supply on and is the amber neon
lit underneath the Boiler On/Off Switch ?
•
Is the programmer set to an ‘On’ period for central
heating and are any other controls such as room
thermostat and thermostatic radiator valves set
to their maximum on settings ?
Programmer not working
•
No Display (boiler switched 'On')
- Check the
mains electricity supply to the boiler is ON (the
amber neon underneath the Boiler On/Off Switch
will be lit). If not, check the fuse at the plug or
switched socket.
•
Display only shows Clock
- Has your installer
fitted a programmer away from the boiler, if so, the
built in programmer will be disabled and only
display the clock. Refer to Page 21 of the
Installation & Servicing Instructions.
MAX0055C
DISPLAY
INFORMATION / FAULT
ACTION
FURTHER ACTIONS
P 0.1 - 0.4
bar Loss of pressure in heating system
Replenish CH system & purge air
Find leak(s) and repair
P 0.5 - 0.9
bar Water pressure in CH system low
Replenish CH system & purge air
Find leak(s) and repair
P 1.0 - 2.9
bar Normal pressure, system warm/hot
O.K.
P 3.0 - 3.5
bar Pressure too high, boiler off
Reduce CH system pressure
* Check/replace expansion vessel
U 60
DHW temperature selected (by knob)
c 80
Indicative flow temperature to CH
O.K. Scroll to pressure display "P"
Press RESET button to scroll display
t 80
Indicative flow temperature to DHW
O.K. Scroll to pressure display "P"
Press RESET button to scroll display
b 52
Indicative cylinder temperature
O.K. Cylinder being re-heated
Press RESET button to scroll display
0 00
Boiler in standby mode
O.K.
A 01
Burner failed to light
Check gas is on, Press RESET button
Check condensate outlet is not blocked
A 02
System response fault
Open radiator valves if shut, press RESET
If repeated, call Powermax service
A 03
Over temperature lock-out
Switch off boiler for 10 minutes
Check/replenish system pressure & purge air
A 04
Overheat 'stat open/gas valve failure
Press RESET button
* Check system pressure & gas valve operation
A 05
Relay failure (control)
Switch electricity off - on. Press RESET
If repeated, call Powermax service
A 07
Heat exchanger response fault
Check gas is on, Press RESET button
If repeated, call Powermax service
A 09-12
Internal boiler control failure
Switch electricity off - on. Press RESET
If repeated, call Powermax service
A 15
Loss of pressure in system
Check/replenish system pressure
Find leak(s) and repair. Press RESET
A 18
Control / sensor failure
Switch off boiler
Call Powermax service
A 19
Flame detection / gas valve fault
Switch off boiler
* Check/replace gasvalve, press RESET
A 20
Flame detected with closed gasvalve
Switch boiler off - on. Press RESET
If repeated, call Powermax service
A 33
Fan speed incorrect
Switch boiler off - on. Press RESET
If repeated, call Powermax service
A 40
System response fault
Open radiator valves if shut, press RESET
If repeated, call Powermax service
E 03
Flow temperature abnormally high
Switch off boiler for 10 minutes
Check / replenish system pressure & purge air
E 04
Flow sensor open circuit
Check connections at control
* If repeated, renew sensor/cable
E 06
Flow sensor short circuit
Check wires not damaged
* If repeated, renew sensor/cable
E 07
DHW sensor open circuit
Check connections at control
If repeated, renew DHW sensor/cable
E 08
DHW sensor short circuit
Check wires not damaged
If repeated, renew DHW sensor/cable
E 13/16/19
Internal boiler control error
Switch electricity off - on. Try re-starting
If repeated, call Powermax service
E 20
Premature flame signal
Switch off boiler for 10 minutes
Check condensate outlet not blocked
E 21
Live & Neutral supply reversed
Correct the electrical supply
E 22
Electrical supply not 50Hz
Correct the electrical supply
E 29
Boiler circuit fault
Switch electricity off - on. Try re-starting
If repeated, call Powermax service
E 40
Return sensor open circuit
Check sensor connections
* If repeated, renew sensor or cable
E 41
Return sensor short circuit
Check wires not damaged
* If repeated, renew sensor or cable
E 42
Internal boiler control error
Switch electricity off - on. Try re-starting
If repeated, call Powermax service
* Work to be performed by Baxi Potterton/Corgi technician only
Adjust if required - 55¡ C recommended
Range: 65¡ C (winter) / 45¡ C (summer)
•
No Central Heating or Hot Water
- Is the
programmer set correctly for current time, day,
programme times etc ? For central heating, are
any room thermostats or thermostatic radiator
valves in the system calling for heat ?
•
Incorrect Time & Day Displayed
- Set the
correct time and day as shown on Page 6.
•
ADVANCE Button Not Working
- ADVANCE
Button will not function if central heating is set to
OFF.
Above are the basic items you the user can check
and remedy, if you call out a Potterton service
engineer and the fault is one of those listed above
you will be charged for the visit.
C.H. System Pressure
• Even a very small leak of water from the heating
circuit will cause the status display to
flash
‘P 0.9’.
If left and the pressure drops below 0.5 bar, the
boiler will shut down as a safety precaution and
the status display will show ‘P 0.4’ or 'A 15'.
•
If the pressure indicated at normal working
temperatures (80 °C) shows ‘P 3.1 or higher,
switch off the boiler and contact your service
engineer.