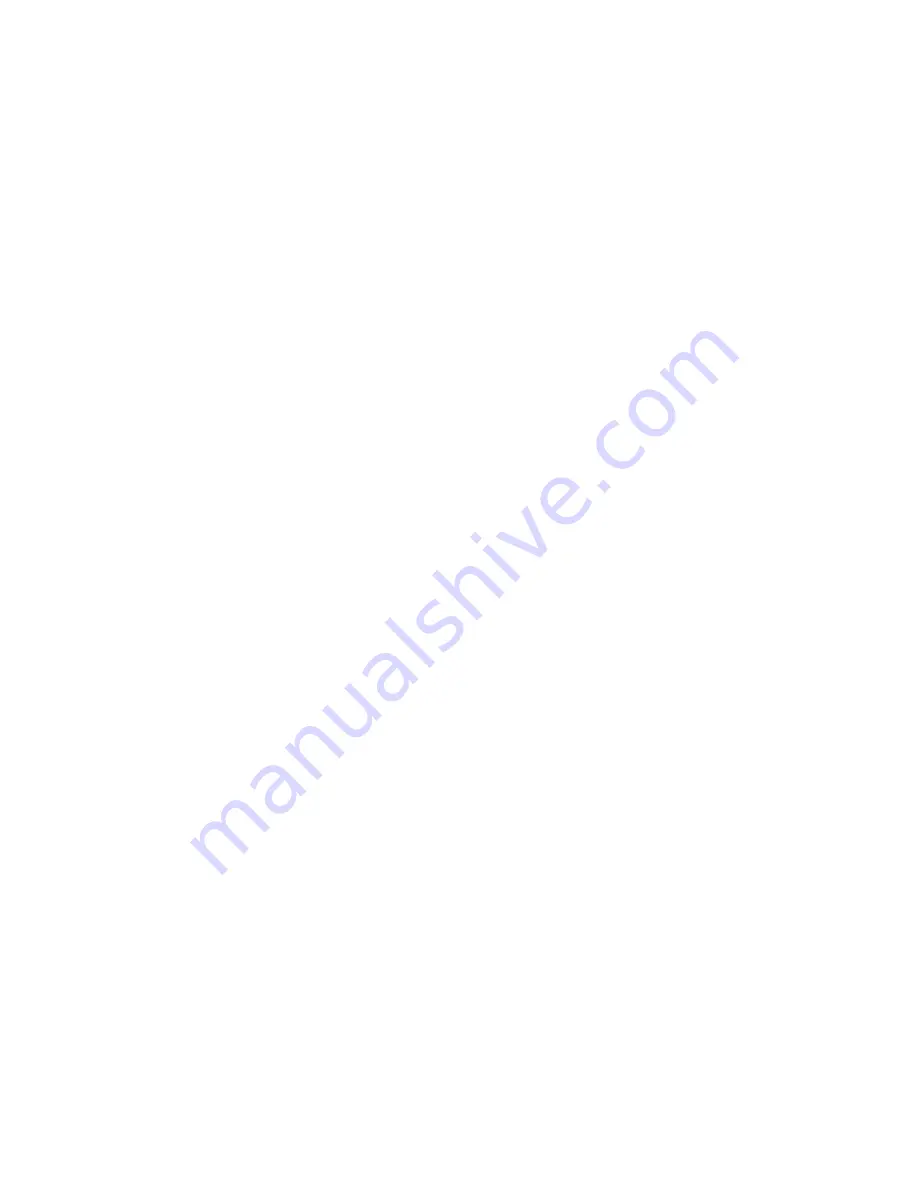
6
The boilers are suitable for operating pressures up to 3 bar. Normal sealed systems operate at 1 to 1.5
bar. Ensure a safety pressure relief valve is fitted to all sealed systems. With open vented installations,
ensure there is a sufficient head of water for the pump to supply the full flow through the boiler of
at least 1½ metres between the bottom of the feed & expansion tank and the top of the boiler.
NOTE: TO COMPLY WITH BUILDING REGULATIONS, PART L (PART J IN SCOTLAND), WHEN THE ELECTRIC
BOILER IS USED FOR CENTRAL HEATING PURPOSES, A ROOM THERMOSTAT MUST BE FITTED TO
CONTROL THE BOILER (SEE PAGE 15).
Do not fit thermostatic radiator valves to the room with the control thermostat, other rooms may be
fitted with thermostatic radiator valves.
DO NOT OPERATE UNDER THERMOSTATIC RADIATOR VALVES ONLY.
Use standard pumps, controls, room thermostat, valves, etc. The main electrical power (high current)
must be routed directly to the boiler via an MCB and RCD, not through the controls. Only a control
signal to the boiler comes from the programmer. The switching of the high power current is done
inside the boiler.
For installations with more than one boiler, mount the boilers side-by-side with a minimum of 50mm
gap between each boiler, output flow tails at the top and the returns at the bottom. ‘Tee’ in the
flows together, increasing in pipe size at each boiler to ensure full flow to each boiler. E.g. for 3 x
12kW boilers, first boiler use a 22mm elbow to the second boiler. Second boiler tee 22mm in from
first boiler, 22mm branch to second boiler, 28mm to third boiler. Third boiler tee 28mm in from
second boiler, 22mm branch to third boiler, 35mm away to heating circuit. Repeat for the return
connections. Single pump in the 35mm flow line, ensure sufficient flow for all 3 boilers, i.e. (for 3
x 12kW boilers requires 3 x 12 l/m = 36 litres/minute minimum). Do not reduce pipework before
‘teeing’. See figure four on page 8.
When filling the system check for leaks. THE WARRANTY WILL BE INVALIDATED IF WATER LEAKS INTO
THE BOILER. ENSURE ALL JOINTS ABOVE THE BOILER ARE SOUND.
After installation the system must first be flushed out in accordance with BS 7593:1992 before
adding the inhibitor. Fernox “Superfloc”, or BetzDearborn Setinel X300 or X400 are ideal flushing
agents for new and existing systems. After flushing the correct amount of inhibitor must be added
before use. Fernox “Superconcentrate”, or MB-1, or BetzDearborn Sentinel X100 can be used for most
water areas, however we recommend you should check with your local water authority to ensure
suitability. Check the inhibitor concentration after installation and periodically thereafter to ensure
correct protection.
FAILURE TO FLUSH PROPERLY OR INADEQUATE INHIBITOR IN THE SYSTEM WILL INVALIDATE THE
WARRANTY.