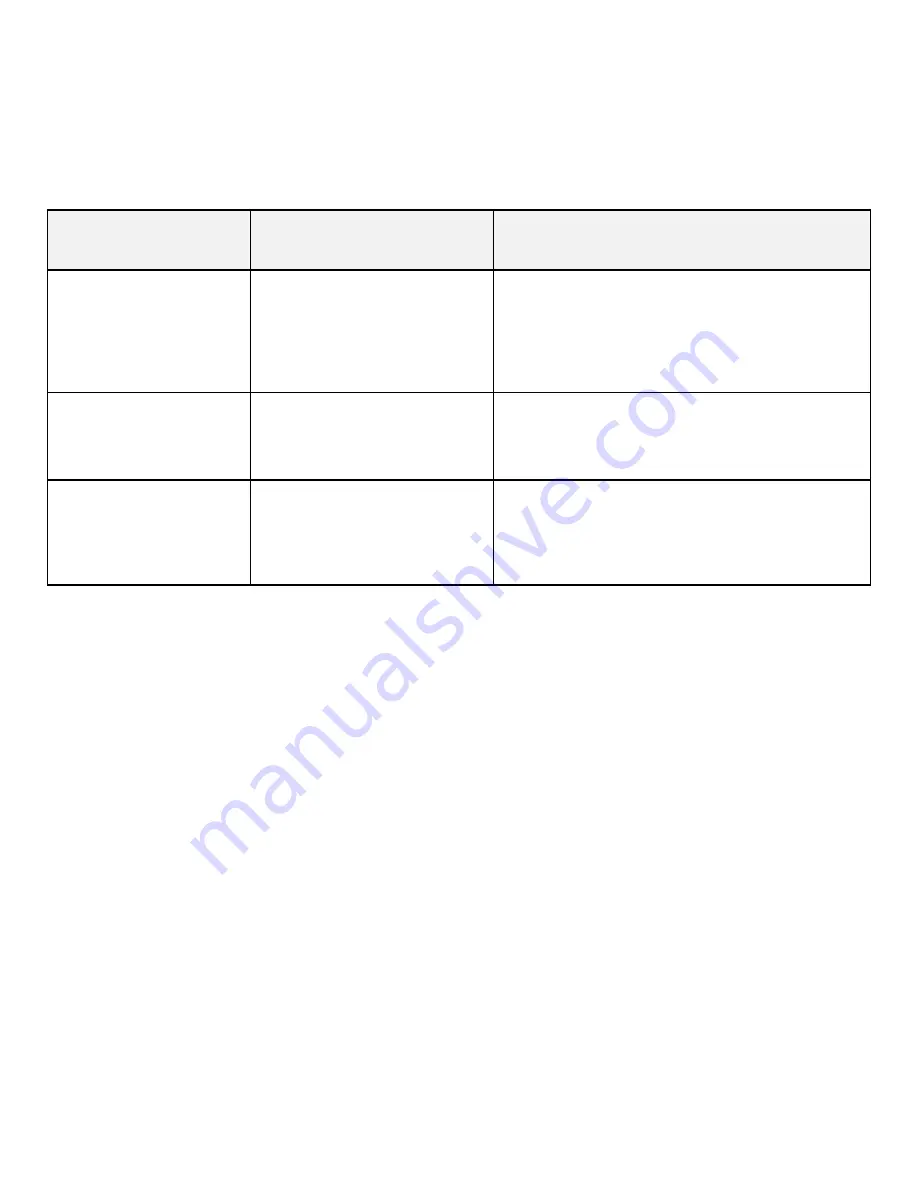
Page 27
PROBLEM
CAUSE
REMEDY
5.
Unit does not stop at the
proper elevation above
floor (in the DOWN
position).
Down limit switch not adjusted
properly.
Refer to installation instruction No. 15, Figure O.
Proper down limit switch adjustment sets load bar to
the level position. If load bar is not level after
actuating both down limit switches, one or both down
limit switches require adjustment.
6.
Motor overload relay in
Mat Mover
®
control panel
keeps tripping.
Incorrect voltage.
Wire not terminated properly, or
broken.
Contact the electrician or consult the factory.
7.
Pulleys at load bar are
squeaking.
Pulleys require lubrication.
Contact your
Porter
dealer. The load bar will need to
be supported or lowered to the floor, pulley housings
disassembled and sheave to be lubricated via the
grease fitting.
Summary of Contents for 91101-100
Page 4: ......
Page 18: ...Page 14 FIGURE J POWER SOURCE ...
Page 19: ...Page 15 FIGURE K BEFORE ...