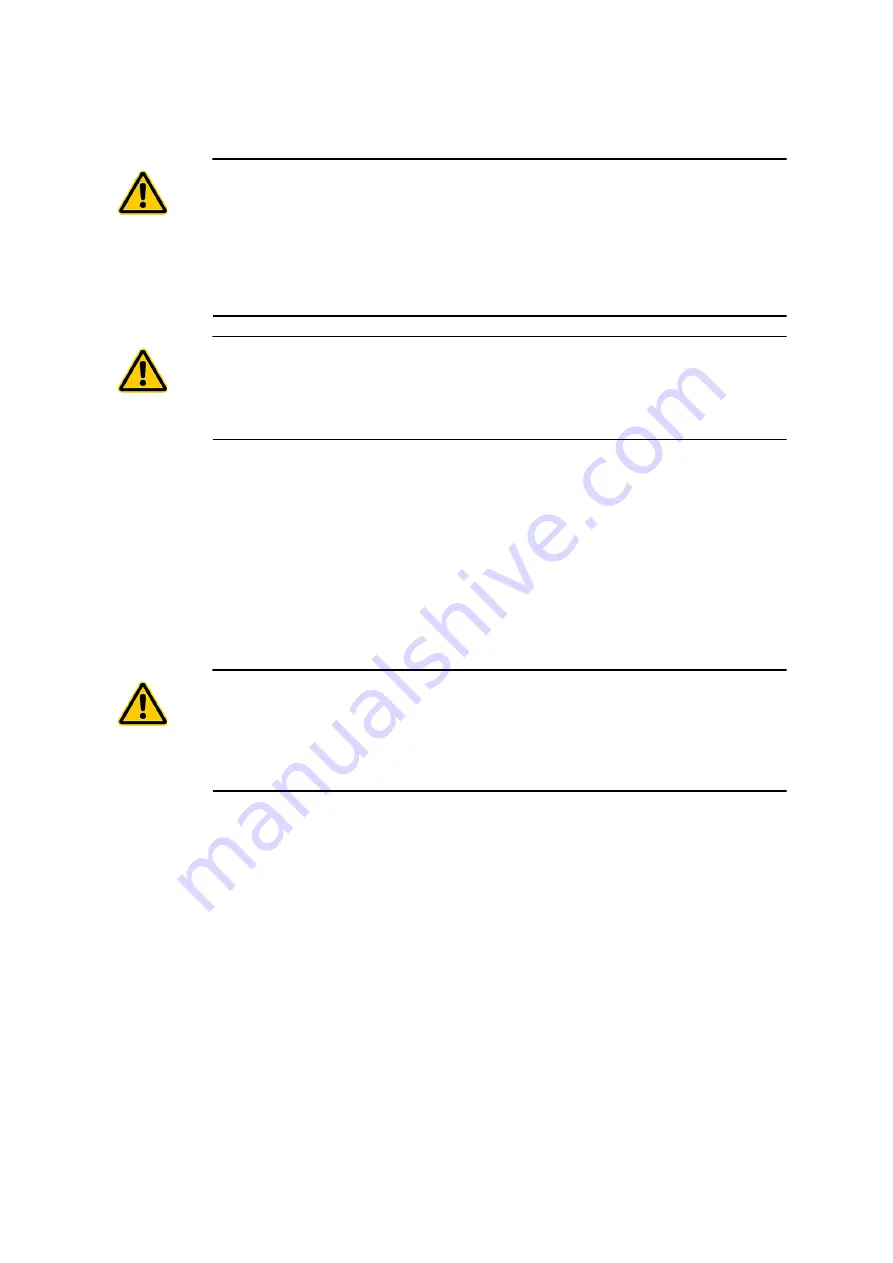
1-4
1 Safety Information
1.2.8
Installing other Components
ATTENTION!
Impairment of the system caused by installing third-party hardware or
software components !
Off-system hardware or software components could damage the system or
impair the function of the software.
» If you want to install components which have not been distributed by
Polytec, please contact Polytec first.
ATTENTION!
Damage of the devices caused by wrong combination of devices!
The individual devices are synchronized.
» Always combine only synchronized devices
1.2.9
Disposal
Instrument
Unless otherwise specified, defective or no longer required instruments and
their components must be properly disposed in accordance with the
applicable legal provisions.
1.3
Lamp Safety
1.3.1
Important Warning Notices
WARNING!
Damage to eyes caused by high light intensity !
» Do not look directly into the illumination module.
» Do not use any operating or calibrating equipment other than specified
here.
1.3.2
Applicable Standards and Directives
Polytec instruments generally comply with the standards of IEC and
EN 62471 (Photobiological Safety of Lamps and Lamp Systems).
Summary of Contents for TMS-350 TopMap In.Line
Page 12: ...1 8 1 Safety Information...
Page 36: ...4 6 4 Measuring...
Page 54: ...B 2 B Declaration of Conformity...
Page 58: ...iv...