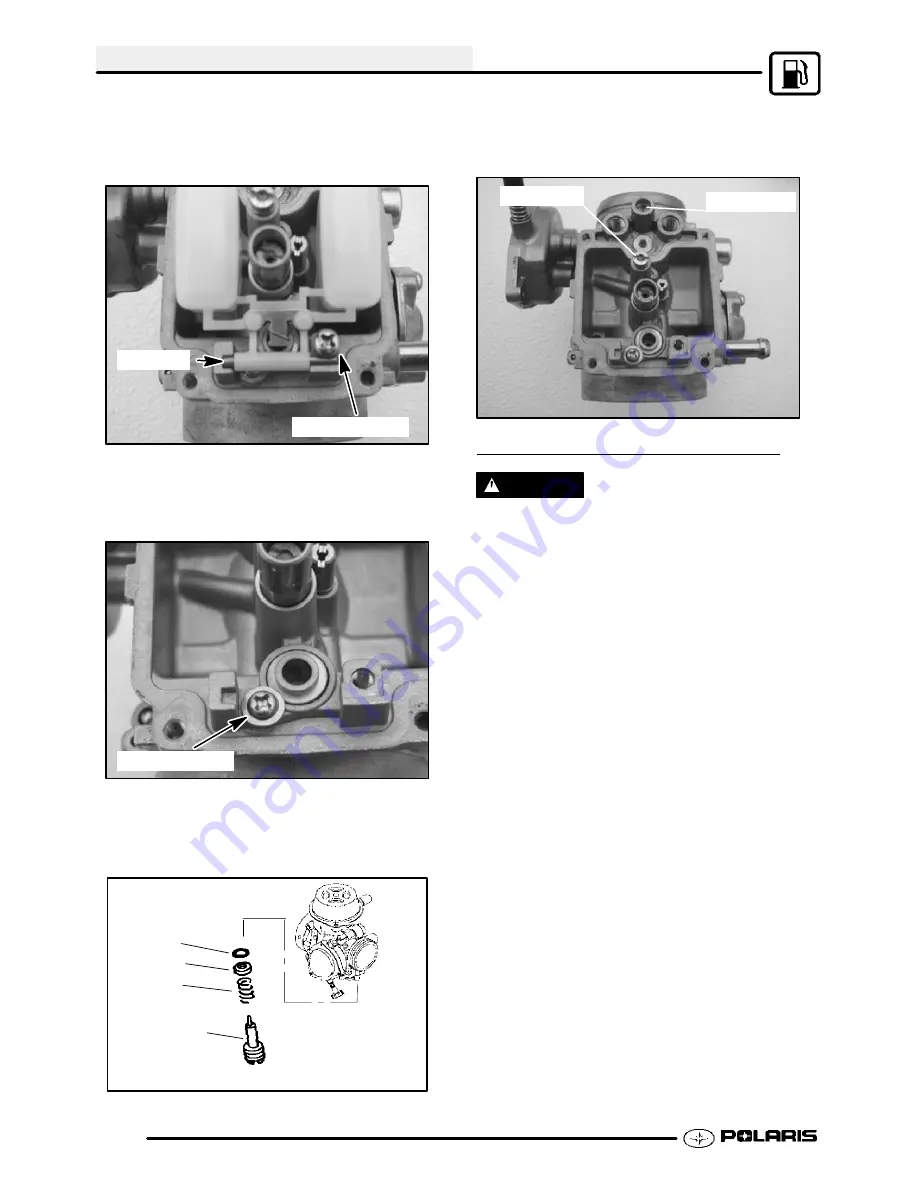
FUEL SYSTEM/CARBURETION
4.8
CARBURETOR DISASSEMBLY CONT’D
2. Remove float bowl. Remove the float pin screw.
The float and float pin can be removed.
Remove Screw
Float Pin
3. Remove inlet needle seat retaining screw along
with plate, and carefully remove needle seat.
NOTE:
Do not use a pliers to remove the seat or
permanent damage may occur.
Remove Screw
4. Remove the pilot mixture screw, spring, flat
washer, and O-Ring. If an anti-tamper plug is
installed over the pilot screw cavity, it must be
removed for access.
O-Ring
Washer
Spring
Pilot Screw
NOTE:
The starter jet is removeable. Upon
disassembly, place the parts in a container for safe
keeping.
Starter Jet
Pilot Screw
CARBURETOR CLEANING
WARNING
Protect eyes from contact with cleaner.
Take
appropriate
safety
measures
during
these
procedures. Safety glasses and chemical resistant
gloves are required. Should you get cleaner in your
eyes or if you swallow cleaner, seek medical attention
immediately.
Carburetor cleaners can be extremely caustic.
Extended periods of soaking can loosen the adhesive
sealer on the passage drill-way plugs.
Do not
soak
rubber or plastic components (such as the vacuum
slide diaphragm, needle seat screen, or O-Rings in
caustic cleaning solutions. Irreparable damage may
occur. Do not use agitator--type carburetor cleaning
equipment. Rubber parts must be cleaned with mild
detergent and hot water only.
1. Thoroughly clean the carburetor body, jets, and
all passages with carburetor cleaner or electrical
contact cleaner.
2. If the carburetor is extremely dirty or
contaminated with fuel residue and varnish, soak
for short periods only in carburetor cleaner, and
rinse in hot water.
3. Replace the jets if they have a buildup of fuel
residue or bacterial growth that cannot be
removed. Even a small amount of residue will
reduce the flow characteristics of the jet.
4. Verify all passages and jets are unobstructed by
spraying electrical contact cleaner through the
passages.
CAUTION:
Do not use wire or welding
tip cleaners as the orifice size may be altered.
5. Use low pressure air to dry carburetor body and
all components.
Enfocus Software - Customer Support
Summary of Contents for PREDATOR 2003
Page 1: ...2003 PREDATOR SERVICE MANUAL 2003 PREDATOR SERVICE MANUAL PN 9918062 PN 9918062...
Page 5: ......
Page 9: ...GENERAL INFORMATION 1 4 PREDATOR MODELS PREDATOR 500 PREDATOR 500 TROY LEE LIMITED EDITION...
Page 15: ...GENERAL INFORMATION 1 10 NOTES...
Page 43: ...MAINTENANCE 2 28 NOTES...
Page 89: ...ENGINE 3 46 NOTES...
Page 167: ...BRAKES 6 22 NOTES...
Page 188: ...ELECTRICAL 7 21 WIRING DIAGRAM 2003 PREDATOR No Neutral Light Neutral Start Lost if failed...
Page 193: ...PN 9918062 PN 9918062 Printed in the USA Printed in the USA...