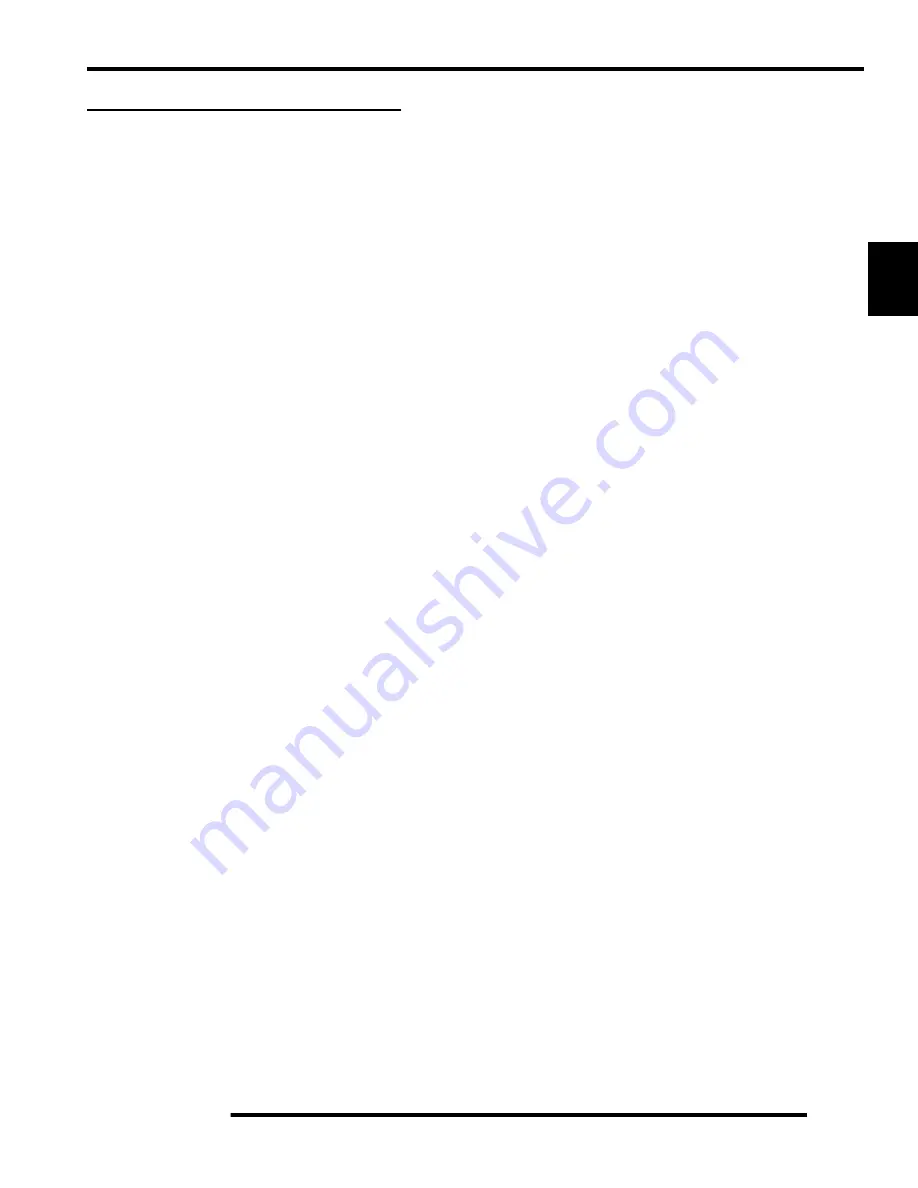
3.9
ELECTRONIC FUEL INJECTION
3
ELECTRONIC FUEL INJECTION
General Information
The Electronic Fuel Injection (EFI) system is a complete engine
fuel and ignition management design. This system includes the
following principal components:
• Fuel Pump / Fuel Filters / Pressure Regulator
• Fuel Line
• Fuel Rail
• Fuel Injectors
• Throttle Body / lntegrated Air Fuel Manifold (IAFM)
• Electronic Control Unit (ECU)
• Ignition Coil
• Engine Coolant Temperature Sensor (ECT)
• Throttle Position Sensor (TPS)
• Crankshaft Position Sensor (CPS)
• Intake Air Temperature / Manifold Absolute
Pressure Sensor (T-MAP)
• Idle Air Control (IAC)
• Wire Harness Assembly
EFI Operation Overview
The EFI system is designed to provide peak engine performance
with optimum fuel efficiency and lowest possible emissions.
The ignition and injection functions are electronically
controlled, monitored and continually corrected during
operation to maintain peak performance.
The central component of the system is the Bosch Engine
Control Unit (ECU) which manages system operation,
determining the best combination of fuel mixture and ignition
timing for the current operating conditions.
An in-tank electric fuel pump is used to move fuel from the tank,
through the fuel line, to the fuel rail. The in-tank fuel pressure
regulator maintains a system operating pressure of 43 psi and
returns any excess fuel to the tank. At the engine, fuel is fed
through the fuel rail and into the injectors, which inject into the
intake ports. The ECU controls the amount of fuel by varying the
length of time that the injectors are "on." This can range from
1.5-8.0 milliseconds depending on fuel requirements. The
controlled injection of the fuel occurs every other crankshaft
revolution, or once for each 4-stroke cycle. The total amount of
fuel needed for one firing of a cylinder is injected during each
cycle. When the intake valve opens, the fuel/air mixture is
drawn into the combustion chamber, ignited and burned.
The ECU controls the amount of fuel being injected and the
ignition timing by monitoring the primary sensor signals for
intake air temperature, manifold absolute pressure (load),
engine temperature, speed (RPM), and throttle position. These
primary signals are compared to the programming in the ECU
computer chip, and the ECU adjusts the fuel delivery and
ignition timing to match the values.
During operation the ECU has the ability to re-adjust
temporarily, providing compensation for changes in overall
engine condition and operating environment, so it will be able
to maintain the ideal air/fuel ratio.
During certain operating periods such as cold starts, warm up,
acceleration, etc., a richer air / fuel ratio is automatically
calculated by the ECU.
Initial Priming / Starting Procedure
NOTE: The injection system must be purged of all
air prior to the initial start up, and / or any time the
system has been disassembled.
If the EFI system is completely empty of fuel or has been
disassembled and repaired:
1.
Cycle the key switch from “OFF” to “ON” 6 times,
waiting for approximately 3 seconds at each “ON” cycle to
allow the fuel pump to cycle and shut down.
2.
Once step 1 is completed, turn the key switch to “START”
until the engine starts or 5 seconds has passed.
3.
If the engine failed to start, repeat step 1 for 2 more cycles
and attempt to start the engine.
If the engine fails to start, a problem may still exist, and should
be diagnosed.
NOTE: Accurate testing of EFI components is
recommended utilizing the Digital Wrench™
Diagnostic Software (dealer only).
PartShark.com
877-999-5686
Summary of Contents for 2009 Sportsman XP 850
Page 10: ...NOTES GENERAL INFORMATION 1 10 P a r t S h a r k c o m 8 7 7 9 9 9 5 6 8 6 ...
Page 44: ...NOTES MAINTENANCE 2 34 P a r t S h a r k c o m 8 7 7 9 9 9 5 6 8 6 ...
Page 148: ...5 56 ENGINE Balance Shaft Timing P a r t S h a r k c o m 8 7 7 9 9 9 5 6 8 6 ...
Page 154: ...NOTES ENGINE 5 62 P a r t S h a r k c o m 8 7 7 9 9 9 5 6 8 6 ...
Page 202: ...NOTES CLUTCHING PVT 7 30 P a r t S h a r k c o m 8 7 7 9 9 9 5 6 8 6 ...
Page 256: ...NOTES BODY FRAME 9 10 P a r t S h a r k c o m 8 7 7 9 9 9 5 6 8 6 ...
Page 323: ...12 31 ELECTRICAL 12 Instrument Cluster Circuit P a r t S h a r k c o m 8 7 7 9 9 9 5 6 8 6 ...
Page 327: ...12 35 ELECTRICAL 12 Battery Charging Circuits P a r t S h a r k c o m 8 7 7 9 9 9 5 6 8 6 ...
Page 329: ...12 37 ELECTRICAL 12 Constant Power Circuits P a r t S h a r k c o m 8 7 7 9 9 9 5 6 8 6 ...
Page 335: ...12 43 ELECTRICAL 12 Engine Start Command Circuits P a r t S h a r k c o m 8 7 7 9 9 9 5 6 8 6 ...
Page 338: ...12 46 ELECTRICAL AWD ADC Circuits P a r t S h a r k c o m 8 7 7 9 9 9 5 6 8 6 ...
Page 341: ...12 49 ELECTRICAL 12 Radiator Fan Circuit P a r t S h a r k c o m 8 7 7 9 9 9 5 6 8 6 ...
Page 343: ...12 51 ELECTRICAL 12 Gear Selector Switch Circuit P a r t S h a r k c o m 8 7 7 9 9 9 5 6 8 6 ...
Page 356: ...WD 20 WIRE DIAGRAM 2009 SPORTSMAN XP 850 INTL EFI P a r t S h a r k c o m 8 7 7 9 9 9 5 6 8 6 ...
Page 358: ...WD 24 WIRE DIAGRAM 2009 SPORTSMAN XP 850 INTL EPS P a r t S h a r k c o m 8 7 7 9 9 9 5 6 8 6 ...
Page 367: ...WD 5 WIRE DIAGRAM 2009 SPORTSMAN XP 850 AWD ADC P a r t S h a r k c o m 8 7 7 9 9 9 5 6 8 6 ...
Page 374: ...WD 19 WIRE DIAGRAM 2009 SPORTSMAN XP 850 EFI P a r t S h a r k c o m 8 7 7 9 9 9 5 6 8 6 ...
Page 376: ...WD 23 WIRE DIAGRAM 2009 SPORTSMAN XP 850 EPS P a r t S h a r k c o m 8 7 7 9 9 9 5 6 8 6 ...