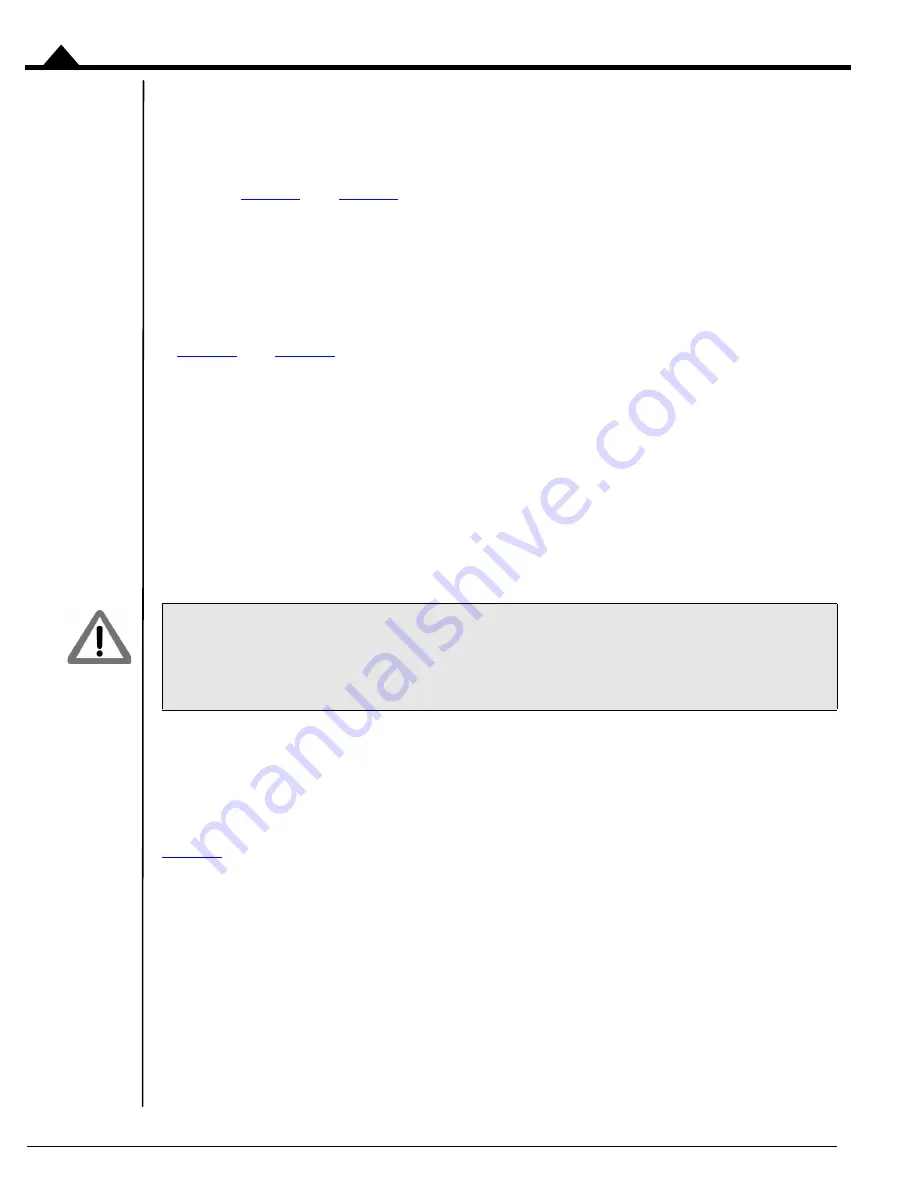
Functional Characteristics
20
Atlas
®
Digital Amplifier Complete Technical Reference
2
provide important recommendations and guidelines for the configuration, selection, placement, mounting method,
and installation procedure for Atlas amplifiers.
Choice of vertical or horizontal Atlas
. The horizontal configuration of Atlas is recommended for applications where the
Atlas is not mechanically mated to a supporting plate and where vibration or movement-related forces may be present.
When the Atlas unit is mechanically mated to a supporting plate, either the horizontal or the vertical configuration
may be used.
C and
D show the Atlas unit mechanically mated to a supporting plate.
Attaching Atlas to a supporting plate
. Some Atlas applications will utilize a supporting plate for heat removal or for
enhanced mechanical stability. For Atlas installations that may be subject to vibration or movement-related forces and
that utilize a supporting plate, special care should be taken to insure that there is no movement between the circuit
card that the Atlas is soldered or socketed to and the supporting plate which the Atlas is mechanically attached to. Such
movement could result in damage to the Atlas unit, the circuit card, or the supporting plate.
Attaching Atlas to a free-standing heatsink
. Some Atlas applications will utilize a free standing heat sink, such as is shown
in
B. Free standing heat sinks are recommended with horizontal Atlas units but are not
recommended for use with vertical Atlas units. When mounting Atlas units with free standing heat sinks special care
should be taken where vibration or movement-related forces may be present. These forces, acting on the additional
mass of the heat sink, may impart excessive mechanical stress on the Atlas resulting in damage to the Atlas unit, the
circuit card, or the heat sink. Depending on the nature and magnitude of the forces, in these applications mounting
the Atlas to a supporting plate may be preferred.
Choice of socket or solder connection to the circuit card
. For best electrical contact to the printed circuit board (PCB),
connection by soldering to the Atlas is generally recommended. This is particularly true for Atlas units that are not
mated to a supporting plate. When the Atlas unit is mounted to a supporting plate either solder or socket electrical
connections may be used, with solder connections recommended for applications benefitting from rigid connection
of the Atlas to the PCB, and sockets being recommended when greater mechanical isolation of the PCB from the
mechanical support is desired.
2.3.2
Thermal Transfer Materials
Thermal transfer materials in the form of thermal tape, pads, paste, or epoxy may be used to improve thermal transfer
between the Atlas’ metal plate and an attached heat sink or supporting plate. These materials improve thermal
conductivity by filling in air gaps that form when two metallic surfaces are mated.
shows a typical application of a thermal transfer material between the Atlas and a heat-removing metal
surface. The following guidelines may be helpful in selecting and sizing the thermal transfer material best-suited to
your application.
The capacity of thermal transfer materials to transfer heat (known as the bulk conductivity) is much lower than that
of metals such as aluminum or copper. Therefore, in general, the thinner the transfer material the better. Thickness of
the material is only precisely controllable for thermal pads and thermal tapes, with thermal pads providing the thinnest
available interfaces beginning at 5 mils (.127 mm) or even less. For use with Atlas amplifiers thermal transfer materials
that are thicker than 40 mils (1.0 mm) are not recommended regardless of the material used.
When using thermal paste or thermal epoxy glue the thickness should be carefully controlled via a silk screen or other
wet film application process. The Atlas unit itself should not be used to squeeze non-uniformly applied paste or epoxy
flat during installation. Doing so may result in damage to the Atlas.
Some of the electrical ratings of the Atlas may not be achievable when electrical connection to the Atlas is via
sockets rather than via soldering. It is the responsibility of the user to determine whether a particular motor out-
put current and voltage rating may be achieved with a given socket.