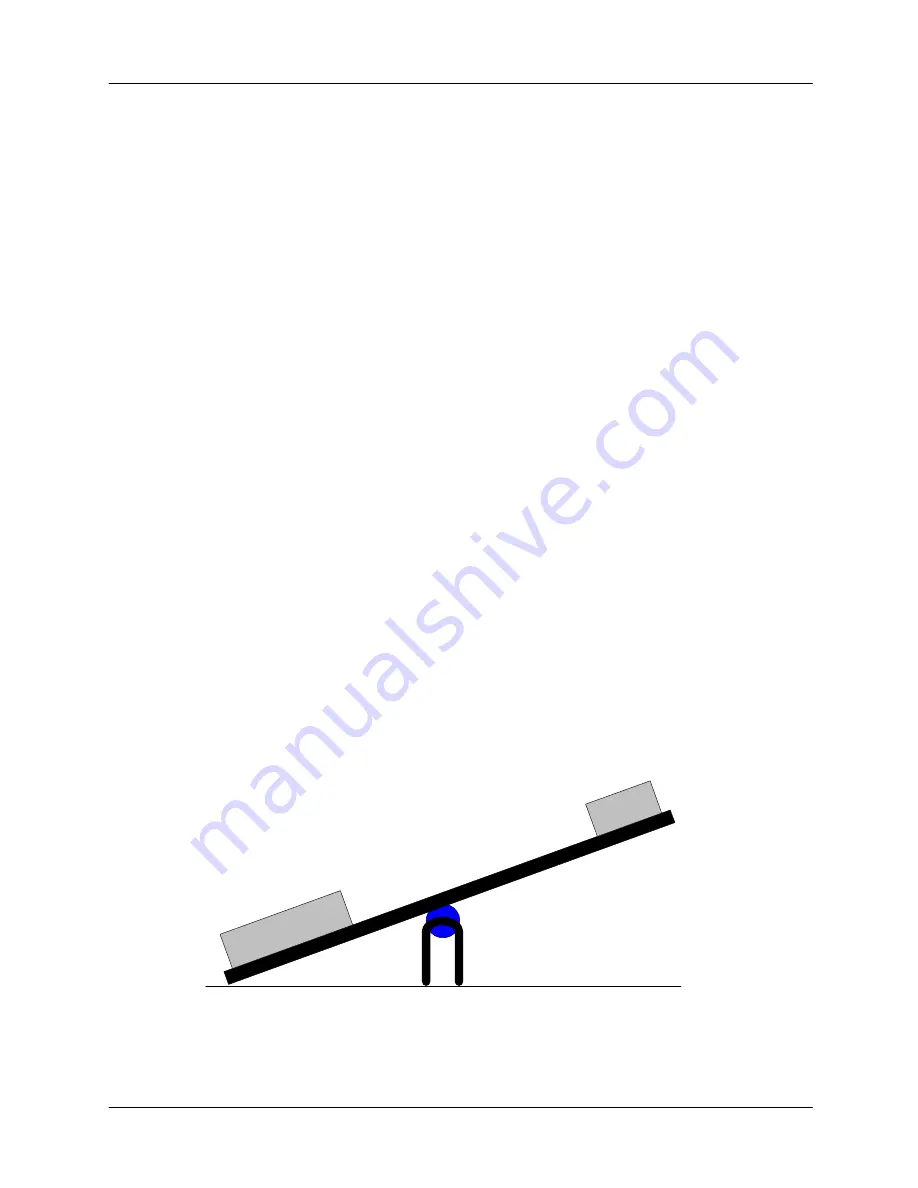
Motion Control Primer
Precision MicroControl Corp.
22
Why does a servo need to be tuned?
A servo is a closed loop system, which the dictionary describes as:
An automatic system in which the output is constantly compared with the input through some form of
feedback. The error (or difference) between the two quantities can be used to bring about the desired
amount of control.
In typical servo systems:
The output is a +/- 10 volt (torque or velocity) command that is applied as an input to a servo
amplifier
The input described in the dictionary definition comes from an encoder. An encoder is an opto
electric device that generates two pulse trains that are phase shifted by 90 degrees
In order for a servo system to perform properly, the difference (error) between the input and
output is multiplied by a set of gain values which results in a new output, bringing about the
desired amount of control
Servo tuning is the process in which the gain values are determined. From one servo axis to another the
gain values will change depending on differences between the motion controller, motor, encoder, and
load. When a user attempts to move an axis without first tuning the servo (determining the gain values)
the motion controller will not be able to calculate the
appropriate
output command to apply to the servo
amplifier. One of the following undesirable results will probably be observed:
The axis will not move at all
The axis moves in the direction of the target but stops well short of the target
The axis moves in the opposite direction of the commanded target
The axis towards the target but fails to 'settle', oscillation of one or more encoder counts is
detected
Imagine a seesaw, with the +/- 10 volt torque/velocity command on one side and the response of the
motor/load (feedback from an encoder) on the other side.
Ou
tpu
t
(co
mm
and
sig
nal
)
Inp
ut
(en
cod
er)
Artisan Technology Group - Quality Instrumentation ... Guaranteed | (888) 88-SOURCE | www.artisantg.com