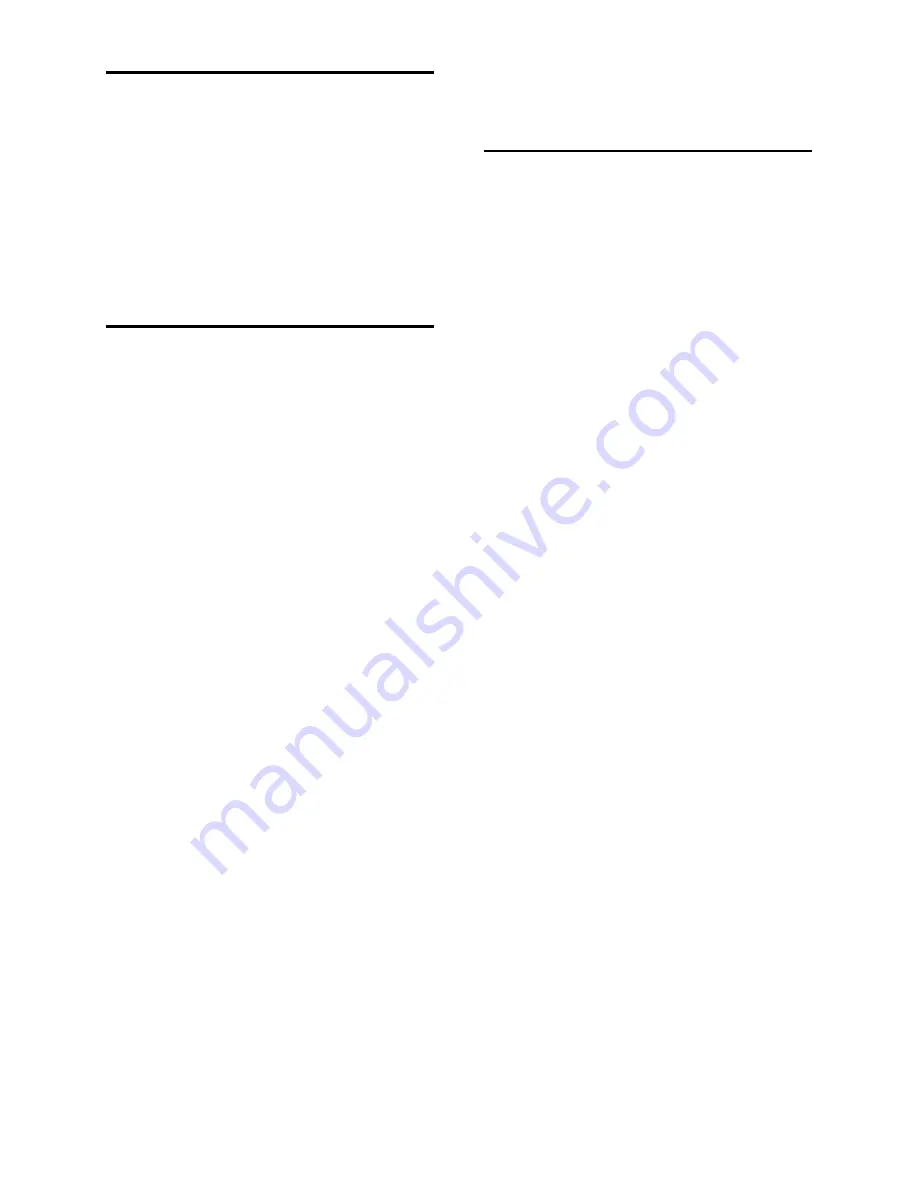
U
Update
firmware ........................................................44
User units
controller time base ....................................160
description ..................................................159
machine zero ..............................................161
output constant ...........................................162
part zero .....................................................161
setting .........................................................159
trajectory time .............................................160
user scale ...........................................159, 160
V
Vector acceleration ..........................................91
Vector deceleration ..........................................91
Vector velocity ..................................................91
Velocity
default units ..................................................86
disable ..........................................................42
restoring settings ................................122, 129
set too high ...................................................66
setting .................................................8, 37, 77
Velocity gain ...................................................162
Velocity mode
enable ...........................................................90
Velocity mode amplifier ....................................25
description ............................................71, 120
tuning ............................................................71
Velocity mode move
execution ......................................................90
setting the direction ......................................90
starting ..........................................................90
Velocity profiles
Contour mode motion ...................................91
Parabolic.......................................................88
S-curve .........................................................88
Trapezoidal...................................................88
Velocity, maximum
setting .....................................................67, 86
Version
firmware........................................................ 43
MCAPI .......................................................... 43
Visual Basic programming ............................... 33
W
Wait
for 'at target'................................................ 118
for trajectory complete................................ 117
Watchdog circuit
description .................................................. 163
Watchdog relay
contacts pin out .......................................... 189
wiring ............................................................ 64
Windows
registry, updating I/O configuring .............. 167
Wiring
+/- 10V command output.............................. 48
A/D inputs..................................................... 63
Anplifier Enable output ........................... 52, 54
Anplifier Fault input ...................................... 55
closed loop stepper ...................................... 80
Driver Disable output.............................. 53, 54
Driver Enable output .................................... 54
Driver Fault input .......................................... 55
encoder, differential...................................... 56
encoder, single ended.................................. 57
E-stop ......................................................... 125
home sensor............................................... 105
home sensor inputs ...................................... 60
Limit +/- inputs........................................ 58, 59
limit sensor ................................................. 102
Opto isolated inputs ......................... 58, 59, 60
Pulse command output ................................ 51
PWM command output................................. 49
servo, analog command......................... 48, 51
servo, pulse command ................................. 51
servo, PWM command................................. 49
stepper, pulse command.............................. 51
TTL digital inputs .......................................... 61
TTL digital outputs........................................ 62
watchdog relay ............................................. 64
Artisan Technology Group - Quality Instrumentation ... Guaranteed | (888) 88-SOURCE | www.artisantg.com