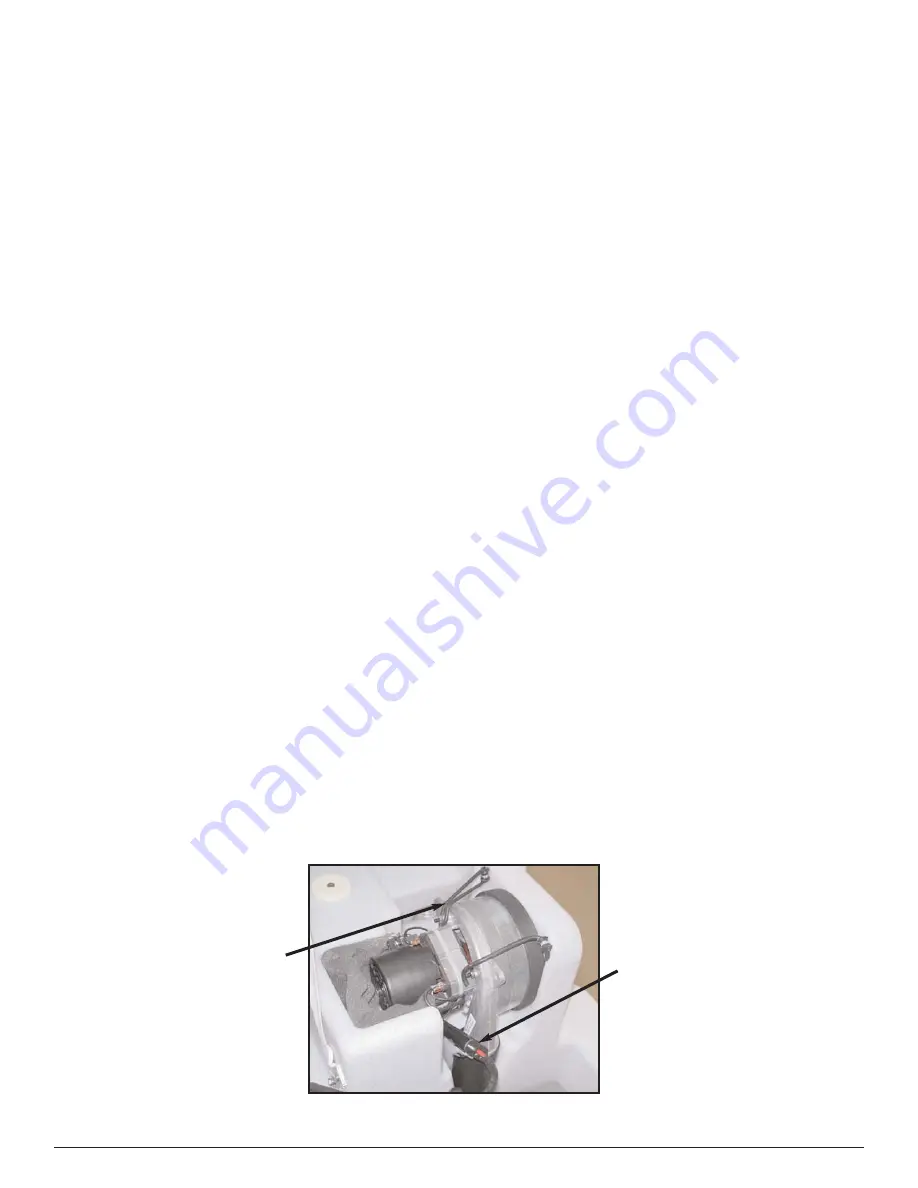
Inspection and Cleaning:
z
Keep batteries clean and dry from residue.
z
Check that all vent caps are tight.
z
Use a solution of baking soda and water to clean if there is acid residue on batteries or corrosion on the terminals.
DO NOT ALLOW ANY BAKING SODA SOLUTION TO ENTER THE BATTERIES.
z
Terminal protectors, protective spray, or petroleum jelly should be applied to terminals to reduce corrosion.
z
Replace any worn or damaged wires.
Watering:
z
Add distilled water, never acid to cells.
z
DO NOT OVERWATER!
z
Always keep battery caps on, except when adding water or taking hydrometer readings.
z
If the batteries are fully charged, add water to a level of 1/8” below bottom of fill well.
z
If the batteries are discharged, add water to a level just above the plates.
z
After watering, replace and tighten all vent caps.
Storage:
z
Batteries should be fully charged prior to and during storage.
z
Never store discharged batteries.
z
Store batteries in a cool, dry place.
z
Recharge batteries before putting them back into service.
Charge Limits:
z
It is not necessary to charge the batteries if the hydrometry, after a work day, is not under 1.240 (28 Be).
z
The maximum suggested temperature is 113° F (45° C).
z
If the electrolyte temperature exceeds more than 50° F (10° C) above the outside temperature, the batteries can
be overcharged.
Vacuum Motor Maintenance
The vacuum motors must be checked and cleaned. The brushes should be checked every six months and replaced if
necessary.
To maintain the vacuum motor, follow these instructions:
After removing the key from the dashboard, remove the vacuum motor by unhooking the rubber straps and unplug the
connection plug. Remove the sponge filter under the motor so that it can be cleaned and replaced. Check the suction
fan from the hole located in the front part of the vacuum motor. By a visual check, the fan should appear undamaged
and well cleaned. To check the brushes, first remove the plastic cap, then unscrew the screws and remove the two
plastic brush supports. Once checked, the brushes can be easily remounted by reassembling all elements.
Connection Plug
16
Rubber Straps
Summary of Contents for CleanStar 30M
Page 19: ...17 Tanks and Cover Group CleanStar 30 020507...
Page 21: ...19 Frame Group CleanStar 30 020507...
Page 23: ...21 Squeegee and Squeegee Lift Group CleanStar 30 020507...
Page 25: ...23 Scrub Deck Group CleanStar 30 020507...
Page 27: ...Scrub Deck Group Continued CleanStar 30 25 020507...
Page 29: ...27 Wiring Schematic CleanStar 30 Page 1 of 3 020507...
Page 30: ...28 Wiring Schematic CleanStar 30 Page 2 of 3 020507...
Page 31: ...29 Wiring Schematic CleanStar 30 Page 3 of 3 020507...
Page 34: ......