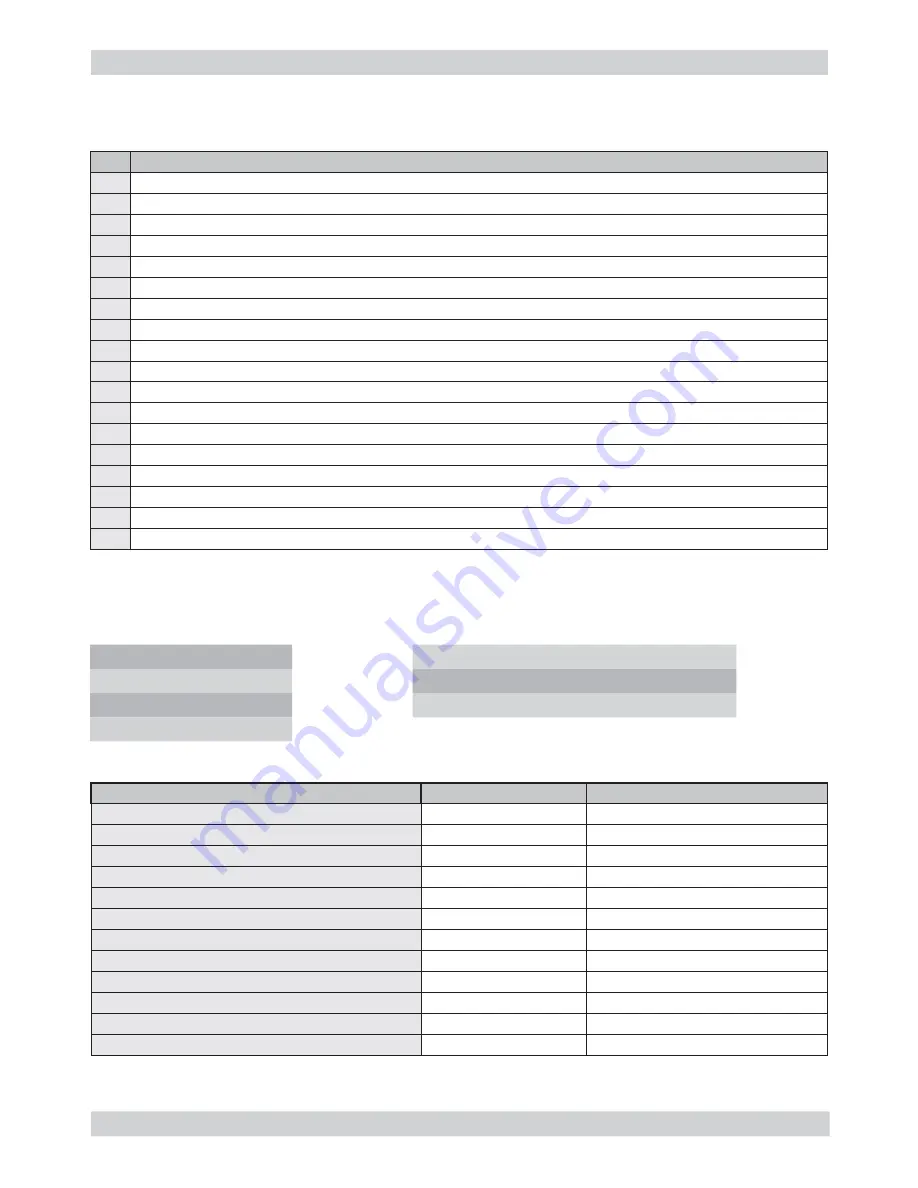
EXPRELIA 06 STANDARD CHECKS
Saeco International Group
Rev. 00 / June 2010
Page / 02
Action
1
Visual inspection (transport damage)
2
Machine data check (rating plate)
3
Operational check / problem analysis
4
Opening machine
5
Visual inspection
6
Operational tests
7
Repairing the faults encountered
8
Checking any modi
fi
cations (view info, new sw, etc.)
9
Service activities in accordance with the operating schedule
10
Internal cleaning
11
Operational test while the appliance is open
12
Assembly
13
Final inspection test
14
Draining the circuit (in winter)
15
External cleaning
16
Lubricating the brewing unit with suitable grease
17
Insulation test HG 701 (dielectric)
18
Documentation
S
Replacement
P
Cleaning
ES
Visual inspection
TR
Noise test
D
Descaling
R
Adjustment
CF
Operative check
Component
Action
Support/tool
Water
fi
lter:
P/S/CF
Water tank lip seal
S/CF
Boiler pin O-ring
S/CF
Brewing unit
ES/P/CF
Grease solvent / Grease
Hoses, attachments and Oetiker clamps
ES/CF
Coffee circuit pump
ES/TR/CF
Hot water/steam circuit pump
ES/TR/CF
Gearmotor:
ES/TR/CF
Coffee grinder
P/R/CF
Vacuum cleaner / brush
Water circuit
D/CF
Saeco descaler
Frothing valve assembly
ES/S/CF
Multi-way valve (solenoid pilot)
ES/S/CF
6.2.
Service
schedule
6.1.
Repair
schedule
01
Summary of Contents for Exprelia Series
Page 3: ...Saeco International Group Rev 00 June 2010 EXPRELIA CHAPTER 1 INTRODUCTION...
Page 8: ...Saeco International Group Rev 00 June 2010 EXPRELIA CHAPTER 2 TECHNICAL SPECIFICATIONS...
Page 18: ...Saeco International Group Rev 00 June 2010 EXPRELIA CHAPTER 4 OPERATING LOGIC...
Page 30: ...Saeco International Group Rev 00 June 2010 EXPRELIA CHAPTER 5 TROUBLESHOOTING...
Page 41: ...Saeco International Group Rev 00 June 2010 EXPRELIA CHAPTER 7 DISASSEMBLY...
Page 51: ...Saeco International Group Rev 00 June 2010 EXPRELIA CHAPTER 8 CHAPTER 8 NOTES NOTES...
Page 52: ...EXPRELIA 08 NOTES Saeco International Group Rev 00 June 2010 Page 01 01...
Page 54: ...EXPRELIA 09 WATER CIRCUIT DIAGRAM Saeco International Group Rev 00 June 2010 Page 01 01...
Page 56: ...EXPRELIA 10 WIRING DIAGRAM Saeco International Group Rev 00 June 2010 Page 01 01...