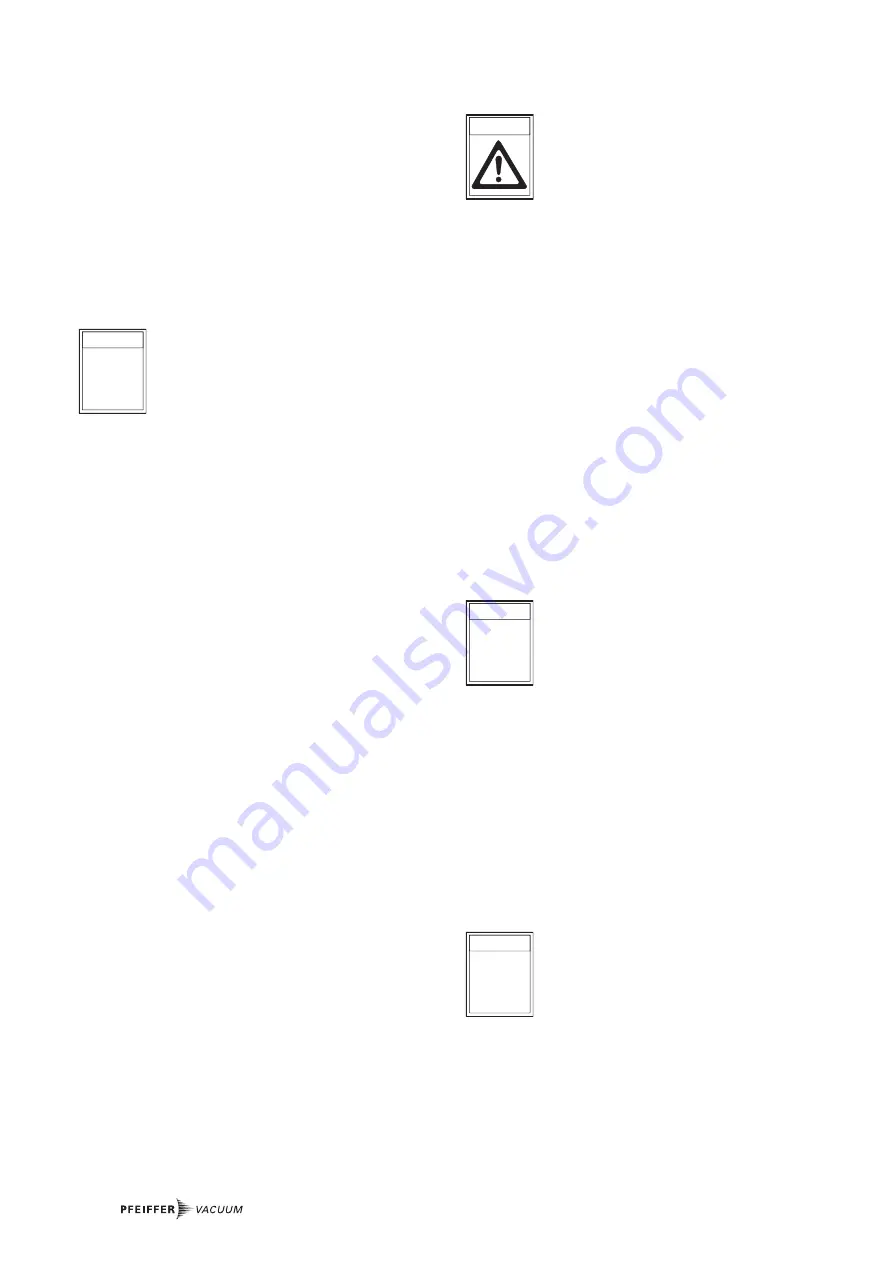
20
4.5. Circulatory Lubrication
The ball bearing on the fore-vacuum side is supplied with
lubricant via the lubricating pump.
The circulation of the lubricant is monitored via a switching
contact. If there is insufficient lubricant, the electronic drive
unit switches off the turbopump. Monitoring is active only
from 60% of the final rotation speed.
If, at a rotation speed of > 60% of the final rotation speed (for
example through the degassification of the lubricant), the
contact opens for
≥
2 minutes, the electronic drive unit
assumes a lubricant deficiency and switches off the
turbopump.
In rotation speed setting mode with set speed
below 60% of the rated rotation speed the
pump is first accelerated to 60% and then adju-
sted to the selected rotation speed.
➡
Check the filling level of the lubricant.
➡
Re-start the turbopump with switch S1 on the power
supply.
4.6. Switching OFF And Venting
To avoid contamination occurring when switching off, the
pump should be vented before shut-down.
➡
Switch off both turbopump and backing pump on the
power supply at the same time with switch S1.
Where corrosive gas processes are involved, the sealing
gas supply should be shut off at the earliest after
approximately 10 minutes and both turbo pump and
backing pump switched off with switch S1.
➡
Venting
There are three possibilities to vent turbopump:
– M
Ma
an
nu
ua
all vve
en
nttiin
ng
g with the use of the venting screw
(status on delivery).
– V
Ve
en
nttiin
ng
g w
wiitth
h tth
he
e V
Ve
en
nttiin
ng
g V
Va
allvve
e T
TV
VFF 000055 ((sse
ee
e S
Se
ec
cttiio
on
n 1111..))
which is selectable via the remote control (please
see Section 4.9.), or via the DCU or HPU (please refer to
the respective operating instructions.
– V
Ve
en
nttiin
ng
g iin
n ttw
wo
o sstta
ag
ge
ess when the vacuum chamber
should be vented as quickly as possible.
First stage: venting with a pressure increase rate of
15 mbar/s for 20 seconds.
Second stage: venting with an optionally large venting
valve.
The valve cross-section for a venting rate of 15 mbar/s
must be compatible with the size of the vacuum chamber.
Where small vacuum chambers are involved, the Pfeiffer
Vacuum Venting Valve TVF 005 can be used for first stage
venting.
➡
Shut off water supply.
☞
PLEASE NOTE
4.7. Shutting Down For Longer Periods
Vacuum pumps are sometimes used to pump
aggressive or hazardous gases. There is a
danger of personal injury resulting from coming
into contact with process gases. Before
removing a turbopump from the system, first:
– Vent the turbopump with a neutral gas or dry air.
– Ensure that there is no residual process gas in the system
nor in the feeder lines.
If the turbopump is to be shut down for more than a year:
➡
Remove turbopump from the system.
➡
Change the lubricant (see Section 8.1.).
➡
Close the high vacuum flange and evacuate the turbopump
via the fore-vacuum flange.
➡
Vent turbopump via the venting connection with nitrogen
or dry air.
➡
Close fore-vacuum and venting connection by blank
flanging.
➡
Place the pump vertically on its rubber feet.
➡
The pump must be stored in buildings within a temperature
range of -25 °C to +55 °C.
➡
In rooms with moist or aggressive atmospheres, the turbo-
pump must be air-sealed in a plastic bag together with a
bag of desiccant.
If the pump has been shut down for 44 yye
ea
arrss a
bearing change must be carried out (please
get in touch with Pfeiffer Vacuum Service).
Usability of the F3 lubricant is 4 years without
operation.
4.8. Operations With The DCU 001/DCU
600 or HPU 001
Operations with the DCU 001, DCU 600 or HPU 001 should be
carried out in accordance with the relevant Operating
Instructions:
– PM 0477 BN (DCU description),
– PM 0547 BN (Operating the pump with the DCU),
– PT 0101 BN (Display and Operating Unit HPU 001).
Operations with the DCU 001, DCU 600 and
HPU 001, the remote plug 8d (see Section 10.)
on the TC 750 should be disconnected.
☞
PLEASE NOTE
☞
PLEASE NOTE
WARNING