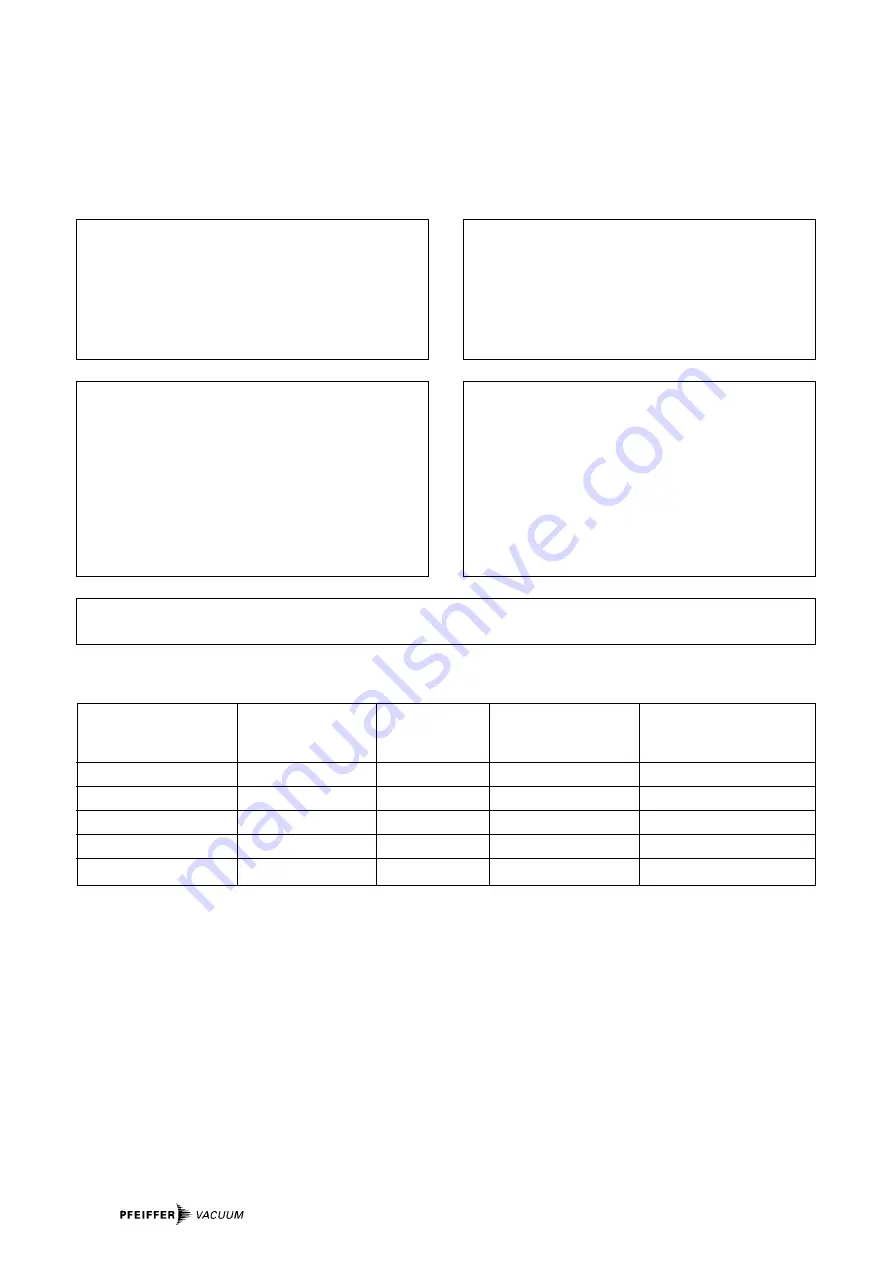
40
Tradename
Chemical name
Danger class
Precautions associated Action if spillage or human
Product name
(or Symbol)
with substance
contact
Manufacturer
1.
2.
3.
4.
5.
5.
Legally Binding Declaration
I hereby declare that the information supplied on this form is complete and accurate. The despatch of equipment will be in
accordance with the appropriate regulations covering Packaging, Transportation and Labelling of Dangerous Substances.
Name of Organisation: _______________________________________________________________________________
Address:
_____________________________________
Post code: _____________________________________
Tel.:
______________________________________________________________________________________
Fax:
_____________________________________
Telex: ________________________________________
Name:
______________________________________________________________________________________
Job title:
______________________________________________________________________________________
Date:
_____________________________________
Company stamp: ________________________________
Legally binding signature: _____________________________________________________________________________
Declaration of Contamination of Vacuum Equipment and Components
The repair and/or service of vacuum components will only be
carried out if a correctly completed declaration has been
submitted. Non-completion will result in delay.
The manufacturer could refuse to accept any equipment
without a declaration.
This declaration can only be completed and signed by authorised and qualified staff:
1. Description of component:
- Equipment type/model: _________________________
- Code No.:
__________________________
- Serial No.:
__________________________
- Invoice No.:
__________________________
- Delivery Date:
__________________________
3. Equipment condition
- Has the equipment been used?
yes
❐
no
❐
- What type of pump oil was used?
___________________________________________
- Is the eqipment free from potentially harmful
substances?
yes
❐
(go to section 5)
no
❐
(go to section 4)
4. Process related contamination
of equipment
- toxic
yes
❐
no
❐
- corrosive
yes
❐
no
❐
- microbiological hazard*)
yes
❐
no
❐
- explosive*)
yes
❐
no
❐
- radioactive*)
yes
❐
no
❐
- other harmful substances yes
❐
no
❐
*) We will not accept delivery of any equipment that has been radioactively or microbiologically contaminated without written
evidence of decontamination!
2. Reason for return:
_____________________________________________
_____________________________________________
_____________________________________________
_____________________________________________
_____________________________________________
Please list all substances, gases and by-products which may have come into contact with the equipment: