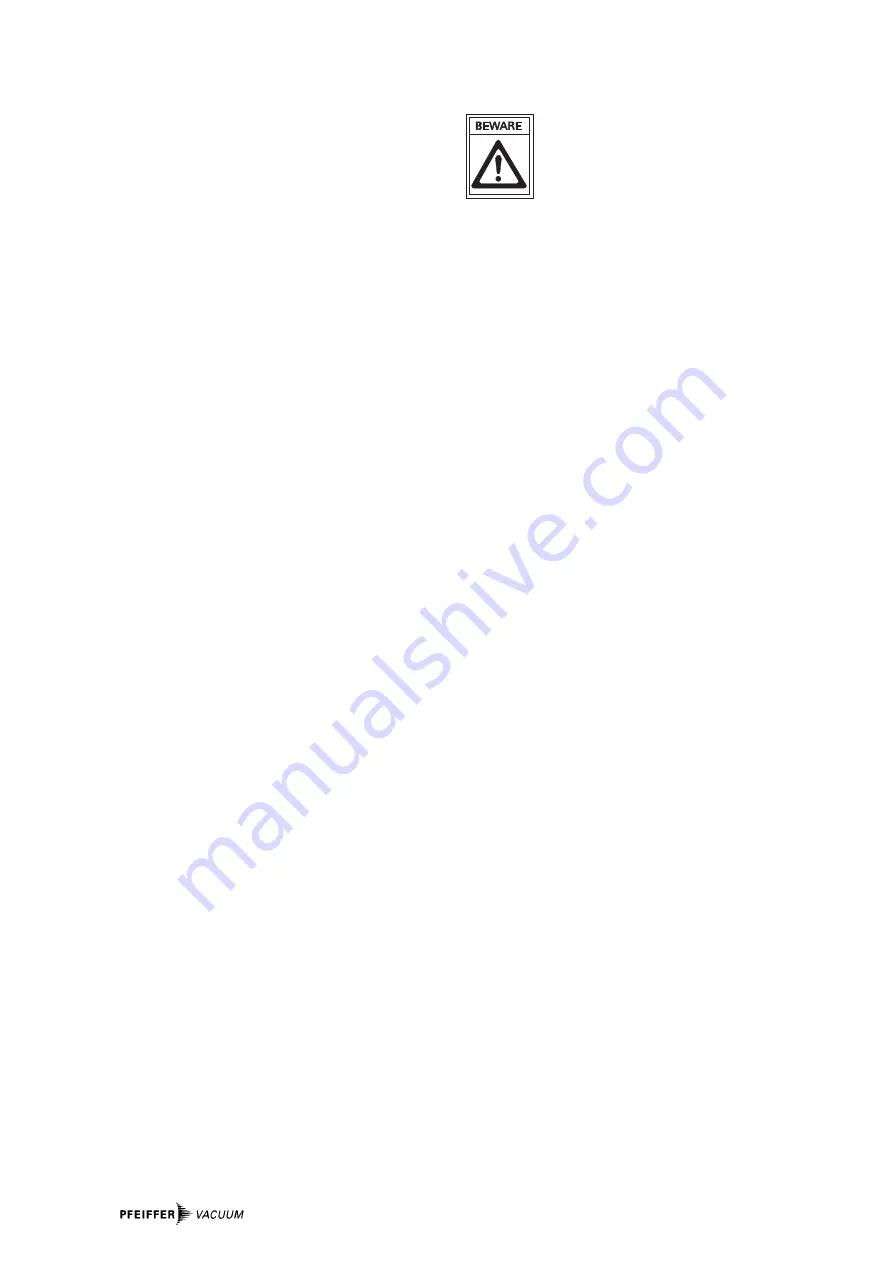
10
4.5. Circulatory Lubrication
The ball bearing on the fore-vacuum side is supplied by lubri-
cant via the lubricant pump. Lubricant circulation is
monitored by means of a contact which transmits signals to
the electronic drive unit which shuts down the turbopump in
the event of a lubricant deficiency. Monitoring is active from
45% of final rotation speed. If at rotation speeds of >45% of
final rotation speed (e.g. resulting from lubricant degassing)
the contact is open
≥
2 minutes, the electronic drive unit iden-
tifies lubricant deficiency and shuts down the turbopump.
➡
Check lubricant filling level.
➡
Re-start turbopump with "reset" (S3 on electronic drive
unit).
➡
Check lubricant pump function.
4.6. Switching Off And Venting
To avoid contamination occurring when switching off, the
pump should be vented before shut-down.
➡
Close vacuum safety valve in the fore-vacuum line.
➡
Operate turbopump at least a further 15 minutes with
sealing gas.
➡
Switch off both turbo pump and backing pump at the same
time with switch S1.
➡
Open locking screw or venting valve in venting connection.
(With PFEIFFER venting valves and respective control
units, venting proceeds automatically).
➡
Shut off water supply.
➡
Close sealing gas supply.
4.7. Shutting Down For Longer Periods
Vacuum pumps are sometimes used to pump
aggressive or hazardous gases. There is a
danger of personal injury resulting from coming
into contact with process gases.
Before removing a turbo pump from the system,
first:
– Vent the turbo pump with a neutral gas or dry air.
– Ensure that there is no residual process gas in the system
nor in the feeder lines.
If the turbo pump is to be shut down for more than a year:
➡
Remove turbo pump from the system.
➡
Replace lubricant (see Section 7.1.).
➡
Close high vacuum flange and evacuate pump via the
fore-vacuum flange.
➡
Vent turbo pump via the venting connection with nitrogen
or dry air.
➡
Close fore-vacuum and venting connections by blank
flanging.
➡
Place the pump vertically on its rubber feet.
➡
In rooms with moist or aggressive atmospheres, the turbo
pump must be air-sealed in a plastic bag together with a
bag of dessicant, e.g silicagel.