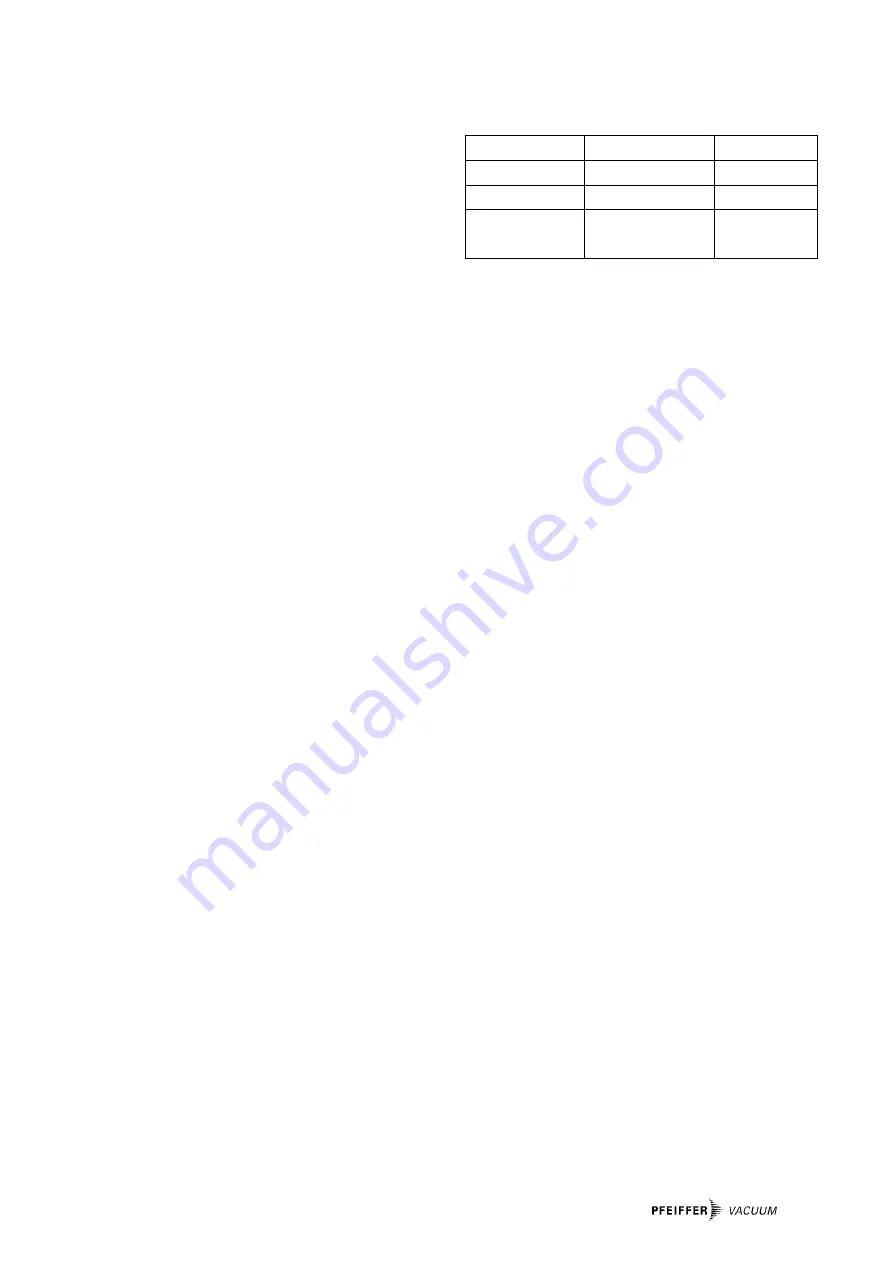
5
Feature
TMH 071
TMU 071
High vacuum flange
ISO-KF / ISO-K
CF-F
High vacuum seal
Elastomer
Metal
Attainable final
< 1 · 10-7 mbar
< 5 · 10-10 mbar
pressure
(without baking-out)
(with baking-out)
2.2. Differences Between The Pump
Types
Abbreviations on the rating plate of the turbopump
Suffix ””P
P””: Purge gas connection for the prevention of the
ingress of aggressive gases into the motor and
bearing arena (Sealing gas valve see
“Accessories”).
Suffix “Y”: Installation orientation in all positions possible.
2.3. Scope Of Delivery
Turbomolekular pump with:
- Electronic drive unit TC 600,
- protecting cover for high vacuum flange,
- protecting cover for fore vacuum flange,
- only DN 63 ISO-K: 2 bracket screws.
Proper Use
– The Turbomolecular Pumps TMH 071 / TMU 071 may only
be used for the purpose of generating vacuum.
– The turbopumps may only be used to pump those media
against which they are chemically resistant. For other
media the operator is required to qualify the pumps for the
processes involved.
– If the process produces dust, the maintenance intervals
must be specified accordingly and sealing gas must be
used.
– The turbopump must be connected to a backing pump in
accordance with Section 3.3.
– Only Pfeiffer Vacuum power units may be used to operate
the TC 600. The use of other power units requires the prior
agreement of the manufacturer and equalization with the
valid specification.
– The pumps may only be operated providing the ambient
conditions in compliance with Protection Type IP 30 are
observed.
– Sealing gas must be used to ensure rotor cooling, when
operate the pump with 50% of the maximum gas load.
Improper Use
The following is regarded, inter alia, as improper:
– The pumping of explosive or corrosive gases,
– Operating the pumps in explosive areas,
– The pumping of gases and vapours which attack the mate-
rials of the pumps,
– The pumping of radioactive media,
– The pumping of corrosive gases without sealing gas,
– The pumping of condensating vapours,
Operation involving impermissibly high levels of gas loads.
– Operation with improper gas modes.
– Operation involving too high levels of heat radiation power
(see Section ”Technical Data”).
– Operation without the use of cooling equipment.
– Operation without cover plate for the TC in environments
which require a protection class superior to IP 30.
– Installation in systems where the turbopumps are
subjected to impact-like stress and vibrations or the effect
of periodically occurring forces.
– The use of other power units or accessories which are not
named in this manual or which have not been agreed by
the manufacturer.
– The connection to power units with earthing of a direct
voltage pole.
Improper use will cause all claims for liability and guarantees
to be forfeited.