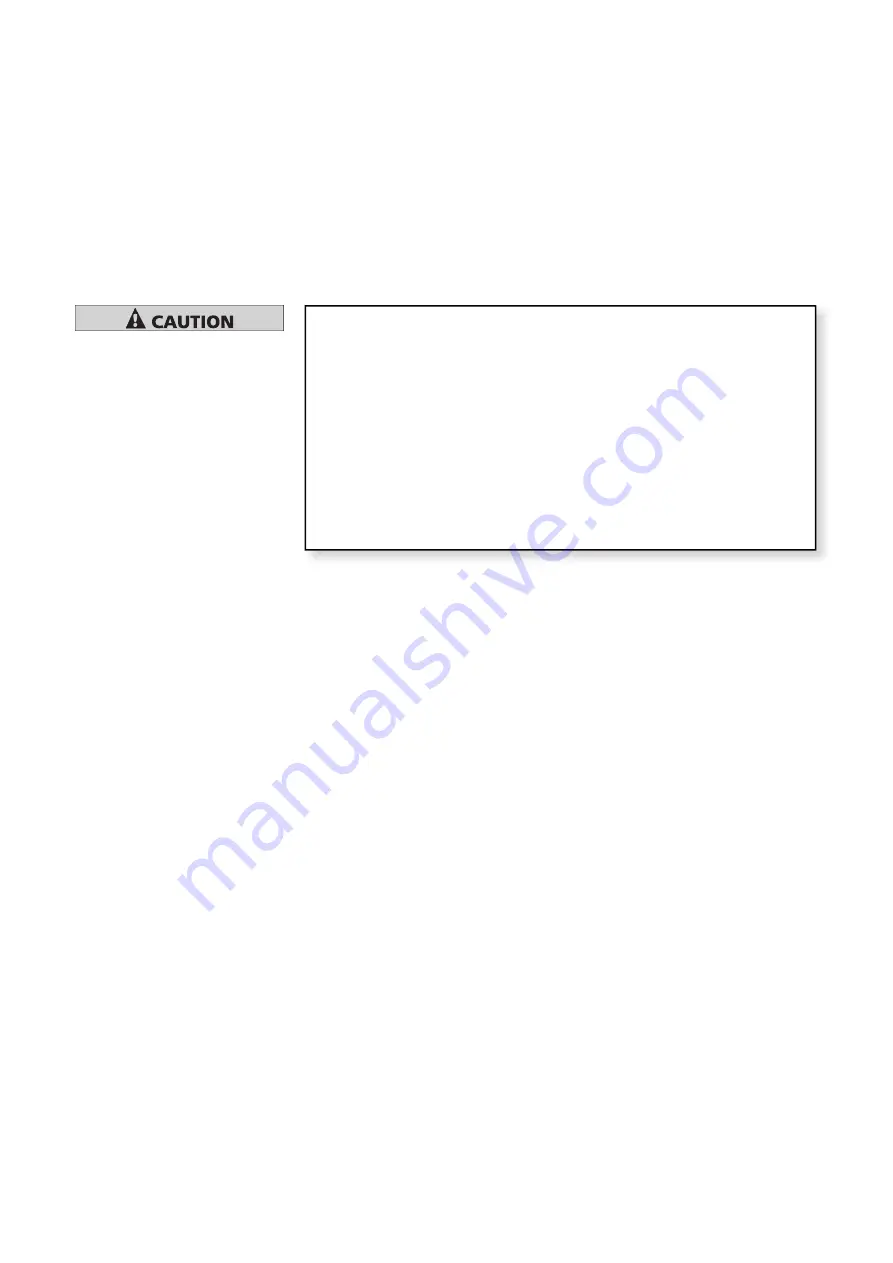
EN – 10
Gas ballast (cont’d)
Using the gas ballast increases the ultimate pressure of the pump as well
as the temperature.
The gas ballast control, located on the frame cannot be used to set the gas
injection flow rate.
When the gas ballast control is open, the pump is not tight when stopped.
To guarantee this tightness, install an automatic gas ballast.
The functioning in permanent regime with opened gas ballast draws away
important oil losses (mist) by exhaust: use an accessory OME 40 HP + ODK
(
see page 14
) or control the oil level very often.
C1 and C2 pump series:
Because of the danger present if the gas ballast (C1 series) or purge gas
ballast (C2 series) was to be opened to atmosphere, remove the plug and
connect the port to a neutral gas supply line (
see page 31
).