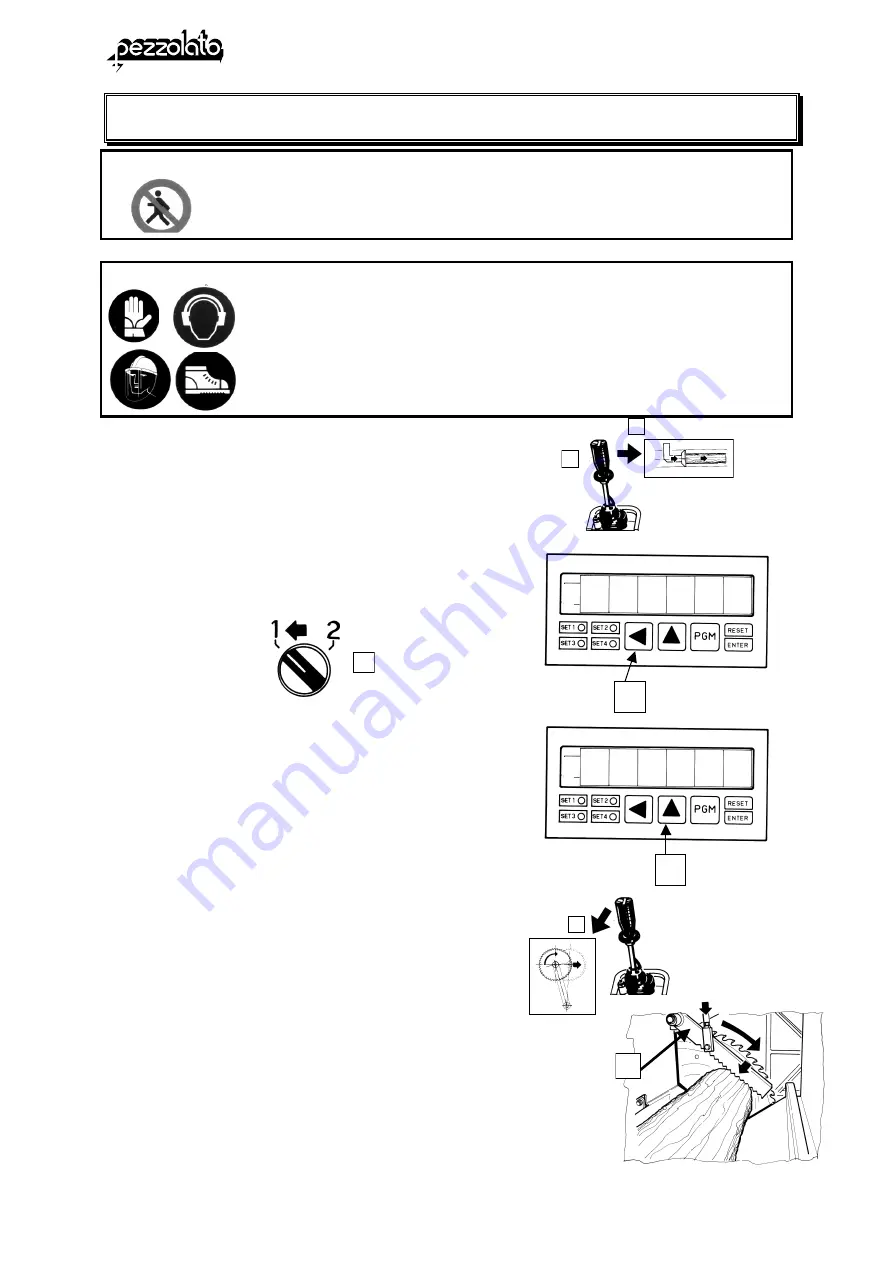
CIRCULAR SAW TLC 800/900/1000/1200 vertical
34
1
B
2 5 0
0 0 0
A
C
2
Chapter 13 (control unity for cut)
USE OF THE MACHINE
WARNING:
No one can pass near the machine’s working area with the
exception of the operator.
WARNING:
Danger of wounds
Wear protective gloves, glasses, caps and accident
prevention shoes.
Move the lever to the right for the
advancement of the small plate.
The log is pushed on the tunnel until the
position of the first cut and noted by the
photoelectric cell. The selector’s pilot light
S light up.
N.B. When the cutting selector’s pilot
light, pressing the key (B) on the
display appear the log length.
Pressing the key (A) on the
display appear the measure of
the cut piece.
N.B.: if the selector’s pilot light is
switched
off,
position
the
selector on the direction 2.
Push the lever to the position (1): you start
the cylinder for the descent of the arm
which block the log (B) and, then, the saw
disc advance.
Leave again the lever for the return of the
disc in the rest position.
Operate in the same way for the following
cuts for all the log length.
0 0 0
0 0 2
B
S
Summary of Contents for TLC 1000
Page 2: ......