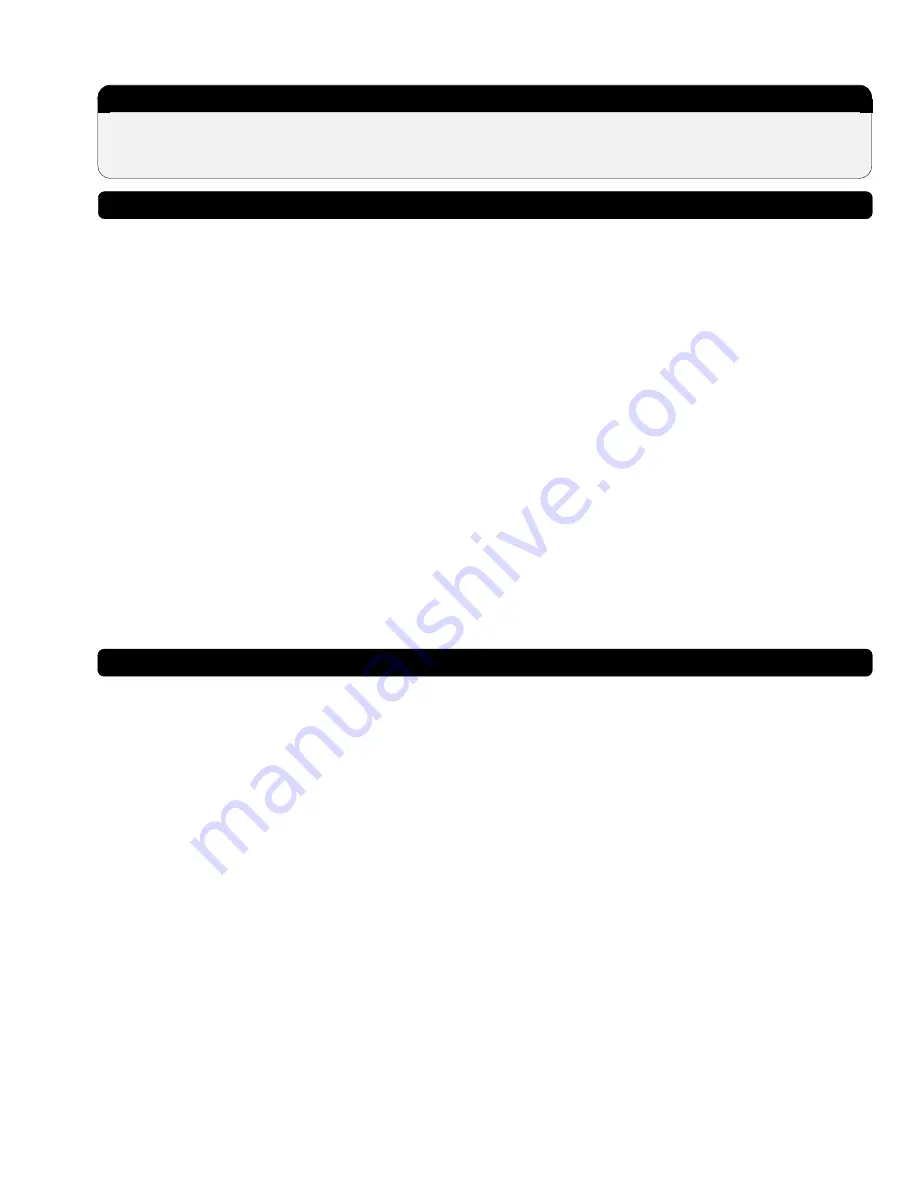
BEBCO EPS
Fuchs®Inc. • 1600 Enterprise Parkway • Twinsburg, Ohio 44087-2245 • www.bebcoeps.com
Telephone (330) 486-0002 • FAX (330) 425-4607 • E-Mail: [email protected]
13
Tubing Installation
System Supply Connections
1.
Select or install a protective gas supply header tap, fitted
with the proper tube size fitting and located within
twenty (20) feet of the enclosure protection system.
2.
If a service valve is placed between the protective gas
supply header and the enclosure protection system, it
must be installed in close proximity of the protected
enclosure and be labeled in accordance with NFPA 496.
3.
Select the appropriate fittings required to connect the
protective gas supply to the protection system regulator
as determined on page 12, “Pneumatic Connection
Requirements”.
4.
Determine appropriate tubing route from the protective
gas supply header to the protection system regulator.
5.
Bend tubing using industrial grade benders, check tubing
fit to ensure proper seating between the tubing and
fittings. Fully ream all tubing ends.
6.
Install tubing and tighten all fittings to fitting
manufacturer’s specifications. Secure tubing to
appropriate structural supports as required.
Enclosure Bulkhead Fittings
1.
Select the fittings required to install the System Supply,
System Supply Bulkhead Fitting and Atmospheric
Reference Bulkhead Fitting, (see page 12, “Pneumatic
Tubing Requirements”).
2.
Choose location for the system supply bulkhead fitting.
This fitting allows the protective gas supply to pass
through the wall of a protected enclosure to the protection
system’s regulator supply inlet connection.
3.
Choose location for the atmospheric reference bulkhead
fitting. This fitting allows the enclosure pressure gauge
to reference atmospheric pressure.
4.
Drill and deburr system supply and reference bulkhead
fitting holes in the protected enclosure. Mount the
fittings.
Enclosure Supply & Reference Connections
1.
Choose location for the enclosure supply connection(s)
based on the requirements on page 7, “Getting Started”.
2.
Place the enclosure reference connection fitting directly
behind the enclosure protection system whenever
possible. For systems protecting multiple enclosures in
series, the enclosure reference connection fitting
must be placed on the last enclosure in the series.
(see page 7, “Getting Started”)
3.
Drill and deburr enclosure supply and reference fitting
holes on the protected enclosure. Mount the fittings.
4.
Determine appropriate route for the enclosure supply
and reference tubing.
5.
Bend tubing using industrial grade benders, check tubing
fit to ensure proper seating between the tubing and
fittings. Fully ream all tubing ends.
6.
Install tubing and tighten all fittings to fitting
manufacturer’s specifications. Secure tubing to
appropriate structural supports as required.
System Supply & Reference Connections
1.
Select or install a protective gas supply header tap, fitted
with the proper tube size fitting and located within
twenty (20) feet of the enclosure protection system.
2.
If a service valve is placed between the protective gas
supply header and the protection system, it must be in
close proximity of the protected enclosure and labeled
in accordance with the NFPA 496.
3.
Determine appropriate tubing route from the protective
gas supply header to the system supply bulkhead fitting.
4.
Determine appropriate tubing route from the system
supply bulkhead fitting to the protection system regulator.
5.
Determine appropriate tubing route from the atmospheric
reference bulkhead fitting to the enclosure pressure
gauge’s reference inlet connection.
6.
Bend tubing using industrial grade benders, check tubing
fit to ensure proper seating between the tubing and
fittings. Fully ream all tubing ends.
7.
Install tubing and tighten all fittings to fitting
manufacturer’s specifications. Secure tubing as required.
Tubing PM Configurations
HELPFUL HINTS
Tubing LH, RH, TM, BM, WM & FM Configurations
All work must be performed by technicians qualified in pneumatic tubing and electrical conduit installation.
Fuchs recommends the use of .035" wall thickness, welded or seamless stainless steel tubing.
If flexible tubing is used, it must be installed in a manner which will protect it from damage and corrosion.
ISC * 877-602-0010 * www.iscenclosurecooling.com