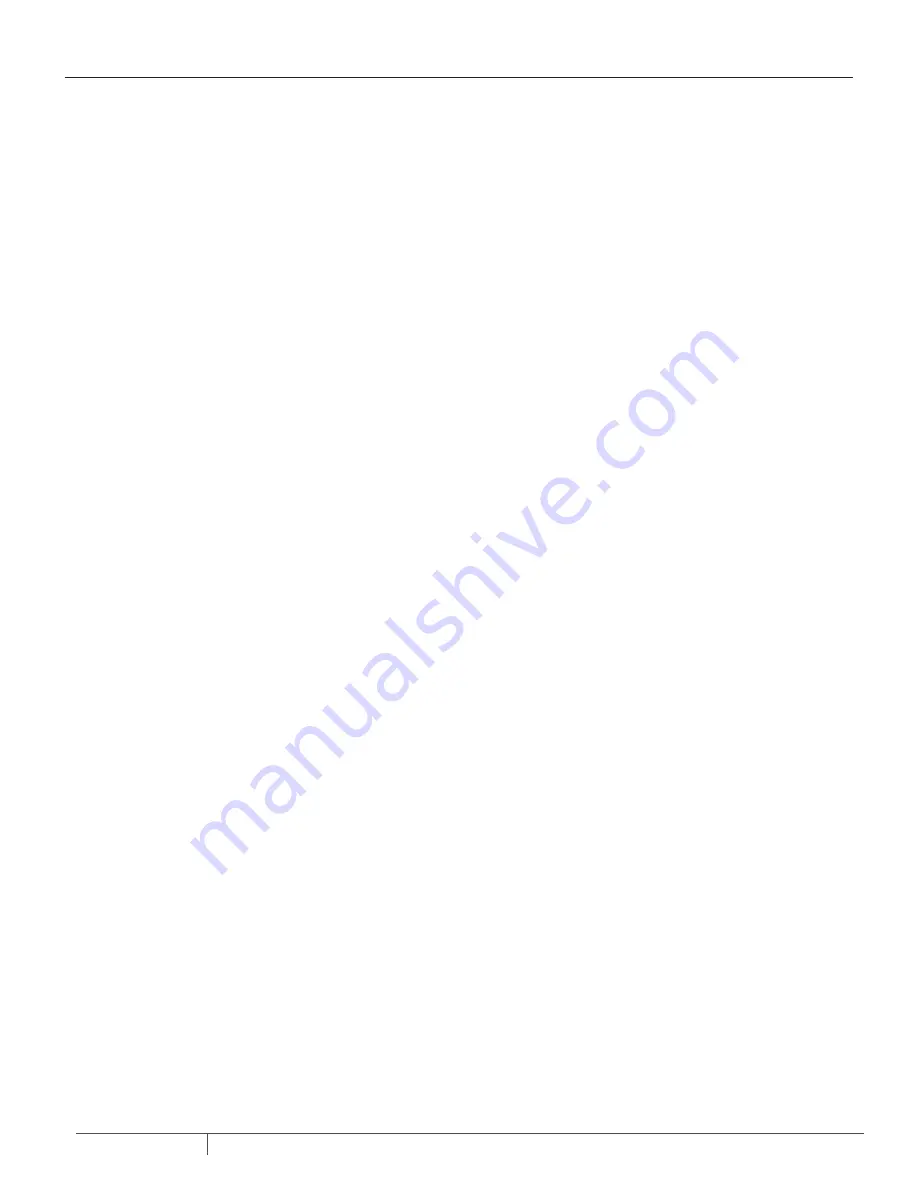
9
HYP1100 (04-08-21)
CANNODE AND PROSTOP-E WIRING
Each cannode can support a total of 32 ProStop-E valves,
which are split between two segments on each cannode.
There are a maximum of 16 ProStop-E valves which can be on
each segment.
1. Divide the total number of nozzle bodies on the machine
by 16 to determine the number of segments that will be
needed.
•
Example: 72 total nozzle bodies/16 = 4.5. With
this fractional value, round up to 5 total segments
required on the machine.
•
Each cannode can support two segments, so three
CanNodes are required for this system. Three
cannodes provides six segments, so the nozzle
bodies can be divided equally among the available
segments or grouped as desired.
2. Starting at the leftmost nozzle body on the machine,
count out the nozzle bodies in the first two segments
and mark the center between the two segments. This is
helpful to visualize where each segment starts and ends.
•
Example: The first cannode will control two
segments of 16 valves. Starting from the leftmost
nozzle body, move towards the center of the boom
and mark in between the 16th and 17th nozzle. This
will be where the cabling will originate and distribute
in opposite directions for segment 1 and segment 2.
•
Segment 1 always connects valves to the left of
the first connection on the segment and segment
2 always connects valves to the right of the first
connection on its segment.
3. Thread the gray end of the M12 cable onto the cannode
port labeled “SEGMENT 1”.
4. Thread the black end of the M12 cable onto the first
ProStop-E identified previously in Step 2.
•
Example: Segment 1 cable would be run from the
cannode to the 16th valve from the left, identified in
Step 2. Typically, this will be a long cable (2520-0259)
(40’/12m) for segments 1 and 2 from the leftmost
cannode, out to the left side of the boom.
5. Connect the GRAY connector from the 2520-0240 or
2520-0265 (for ProStop-E Single/Dual) cable to output
port on this first ProStop-E valve. Wrap the cable around
the boom to take up any slack.
•
Note this is a keyed connector and can only be
installed on the correct threaded port.
6. Connect the BLACK connector to the next ProStop-E to
the left.
•
Note: this is a keyed connector and can only be
installed on the correct threaded port.
7. Repeat this process for all valves to the left on Segment 1.
8. On the last ProStop-E, install a 2300-0067 cap to seal the
unused port.
9. Using the 2520-0241 or 2520-0265 (for ProStop-E Single/
Dual) cables, repeat steps 3-8 for segment 2 on the 1st
cannode, moving to the right along the boom.
10. On the last ProStop-E, install a 2300-0067 cap to seal the
unused port.
11. Starting at the rightmost nozzle on the machine, count
out the nozzles in the first two segments and mark the
center between the two segments.
•
Example: The second cannode will control two
segments of 16 valves. Starting from the rightmost
nozzle, move towards the center of the boom and
mark in between the 16th and 17th nozzle. This will
be where the cabling will originate and distribute in
opposite directions for segment 1 and segment 2.
•
Segment 1 always connects valves to the left of
the first connection on the segment and segment
2 always connects valves to the right of the first
connection on its segment.
12. Thread the gray end of the M12 cable onto the cannode
port labeled “SEGMENT 1”.
13. Thread the black end of the M12 cable onto the first
ProStop-E previously identified in Step 10.
•
Example: Segment 1 cable would be run from the
cannode to the 17th valve from the right, identified
in Step 10. Typically, this will be a long cable (2520-
0259) (40’/12m) for segments 1 and 2 from the
rightmost cannode out to the right side of the boom.
14. Connect the GRAY connector from the 2520-0240 or
2520-0265 (for ProStop-E Single/Dual) cable to output
port on this first ProStop-E valve. Wrap the cable around
the boom to take up any slack.
15. Connect the BLACK connector to the next ProStop-E to
the left.
16. Repeat this process for all valves to the left on Segment 1.
17. On the last ProStop-E, install a 2300-0067 cap to seal the
unused port.
18. Using the 2520-0241 or 2520-0265 (for ProStop-E Single/
Dual) cables, repeat steps 11-15 for Segment 2, moving to
the right along the boom.
19. On the last ProStop-E, install a 2300-0067 cap to seal the
unused port.
20. If there is an additional cannode(s) select the appropriate
length extension cable for the center section (if
necessary) and connect the remaining segment(s) using
Steps 10-18.
•
Optional extension cables: 2520-0242 (3’/1m), 2520-
0243 (6’/2m), 2520-0244 (9’/3m)
•
Optional extension cables for ProStop-E Single/Dual:
2520-0266 (3'/1m), 2520-0267 (6'/2m), 2520-0268
(9'/3m). All have straight connector ends.
INSTALLATION
Summary of Contents for PROSTOP-E
Page 41: ...41 HYP1100 04 08 21 PART NUMBER 2520 0258 WIRINGDIAGRAMS...
Page 42: ...42 HYP1100 04 08 21 PART NUMBER 2520 0250 PART NUMBER 2520 0251 WIRINGDIAGRAMS...
Page 43: ...43 HYP1100 04 08 21 PART NUMBER 2520 0252 PART NUMBER 2520 0253 WIRINGDIAGRAMS...
Page 44: ...44 HYP1100 04 08 21 PART NUMBER 2520 0237 WIRINGDIAGRAMS...