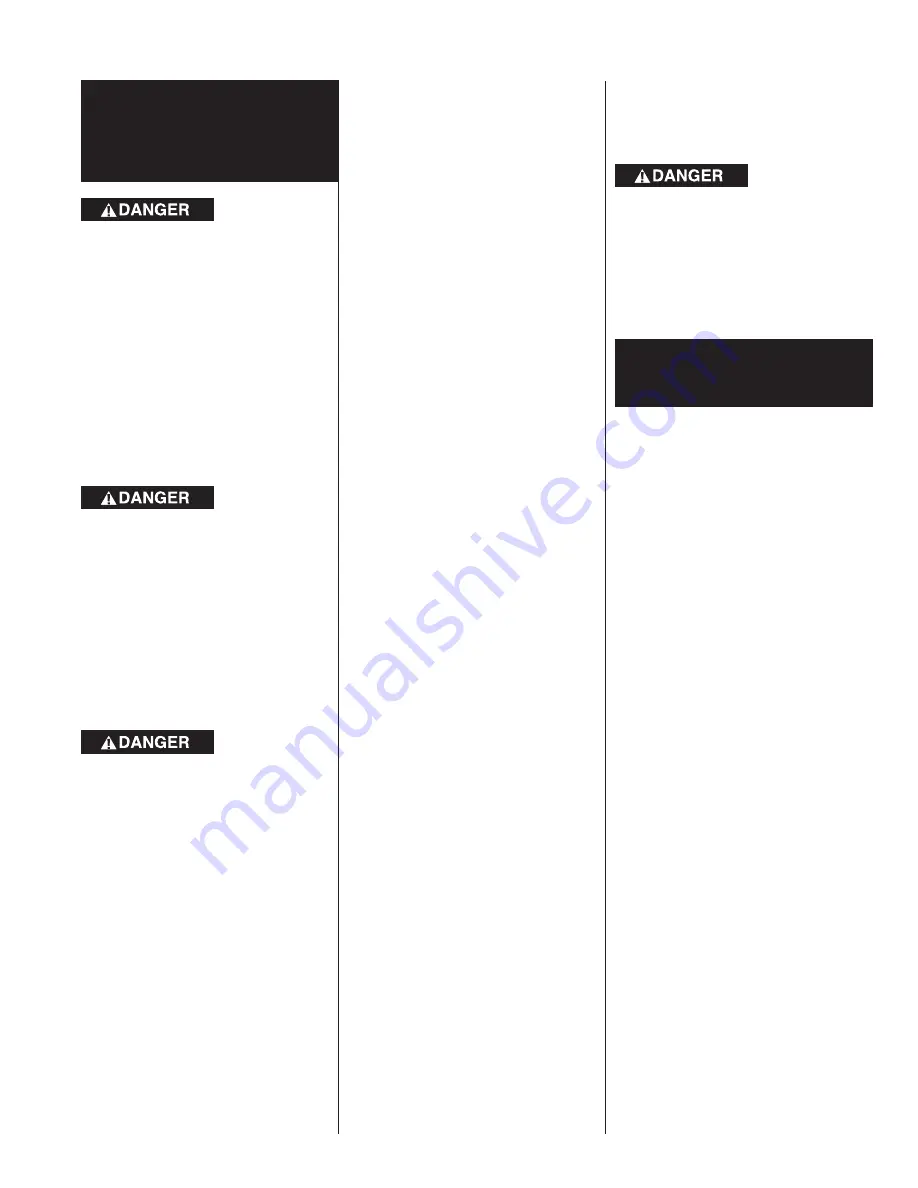
5
Step 3
Attach lifting chain, cable or rope
as supplied to the lifting eye bolts.
Risk of electrical shock or
electrocution. May result
in serious injury or death or
fire hazard. To reduce risk of
electrical shock, do not connect
conduit to pump .
Internal Basin
Connections
Step 1
If the system is supplied with a float
bracket, attach float switches to
the float bracket by clamping
strain relief bushings around the
float cords, then inserting and
twisting the bushings into the float
bracket slots.
Step 2
After grinder pump attachments
have been made, lower the pump
and piping assembly down,
ensuring the discharge valve
union aligns properly. Tighten the
discharge valve union properly
with discharge.
Systems with Junction Box:
Step 1
Ensure power source is off or
dis con nect ed.
Step 2
Push pump power, seal failure/heat
sensor, and float cords through
cord grips in the junction box and
tighten. To prevent corrosion or
electrical short, plug any unused
holes.
Step 3
Remove junction box cover
and make all connections inside
Internal Basin
Installation
Instructions
Risk of electrical shock or
electrocution. May result
in serious injury or death or
fire hazard. Installer must
disconnect all electrical sources
prior to installation. Only
qualified personnel may install
this system. NFPA 70/National
Electric Code (NEC) or local
codes must be followed. System
must be properly grounded
according to NEC or local codes.
Cutting risk. Risk of serious
cutting or amputation exists.
Disconnect all power sources
prior to handling or servicing
pump or grinding mechanism.
Pump may start without
warning. Grinding mechanism
is extremely sharp. Use caution
when handling the grinder
mechanism.
Risk of fire or explosion. Do not
smoke or use open flames in
or around this system. This
system is not intended for use
in hazardous locations per
NFPA/70 National Electric Code.
Consult factory for optional
equipment rated for this use.
Unpacking Pump:
Remove pump from carton.
When unpacking unit, check for
concealed damage. Claims for
damage must be made at the
receiving end through the delivery
carrier. Damage cannot be processed
from the factory.
Systems Description:
Factory built basin systems are
available in 24" diameter basins
with 48" through 96" depths in
one-foot increments. In the system,
the pump and piping assembly is
raised and lowered in the basin
using rope attached to pump with
integral union to facilitate piping
disconnect.
Application:
These pump systems are designed
for pumping effluent or sewage
water with a pH ranging from 5
to 9, specific gravities from 0.9 to
1.1, viscosities ranging from 28
to 35 S.S.U. and temperatures up
to 140°F.
Pump Models:
The basin system may employ any
1 through 2 HP submersible grinder
pump that uses cutter blades to
grind solids into a slurry. Refer
to the pump service manual when
adjusting, dismantling, or repairing
the pump.
Inspection:
Check to be sure that all items for
your particular system are included,
and that the phase and voltage on
the pump nameplate are correct
as ordered. Codes: All local codes
must be observed. Consult the local
inspector(s) before installation to
avoid costly delays or rework.
Grinder Pump Attachments:
Step 1
Attach the stainless steel foot
bracket to bottom of the pump
with bolts and washers provided.
Apply Pipe:
Step 2
Apply thread sealant to pipe
threads and screw the discharge
piping assembly into the pump
discharge.