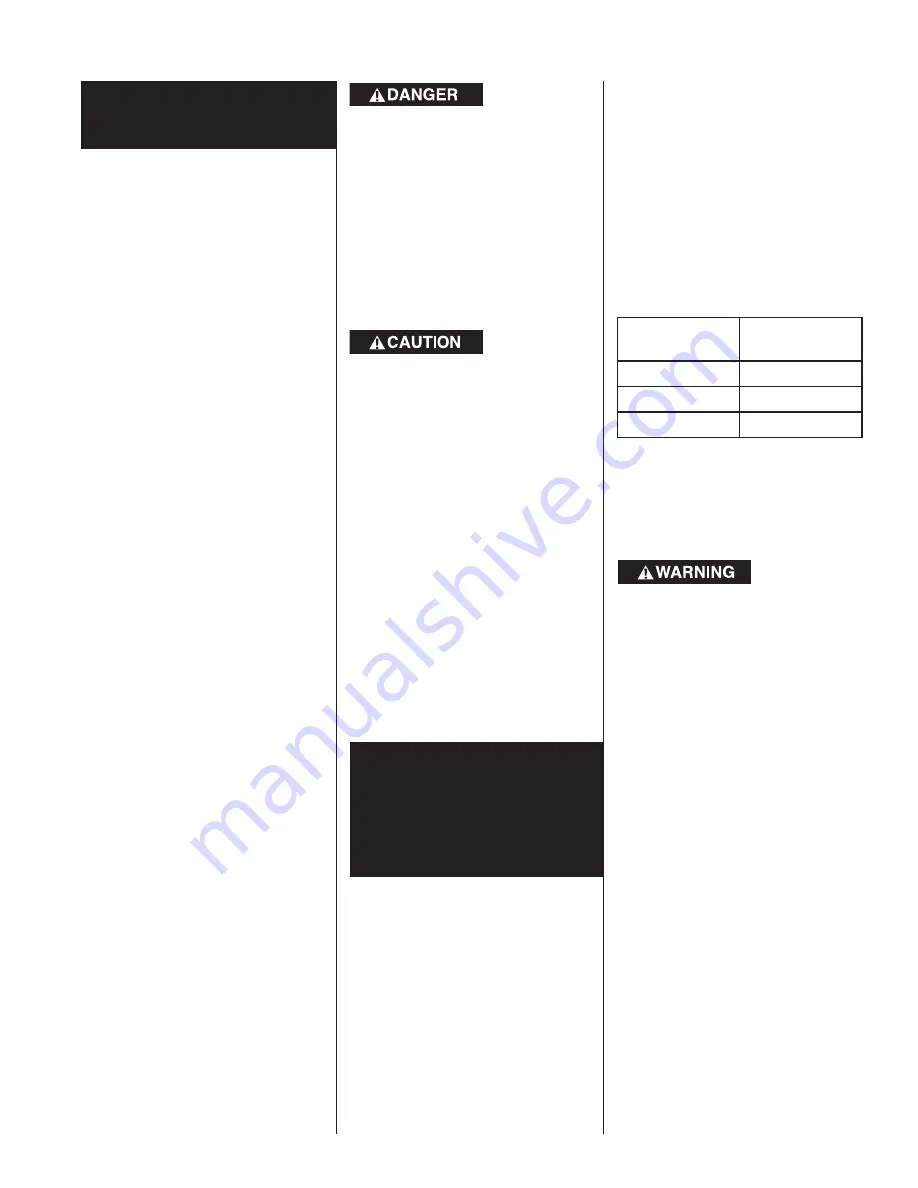
3
Basin Installation
Instructions
Basin System Handling:
Factory built basin systems must
not be dropped, dragged, rolled,
or handled with sharp objects.
Improper handling of basins may
result in damage to the basin,
damage to basin components, or
leaks in the piping assemblies.
Step 1
The pad under the basin requires
4 to 6 inches of appropriate fill.
The ideal basin pad is concrete
in conjunction with antiflotation
tie-down studs. Basin antiflotation
tie-down kits are available from
Hydromatic. If concrete pad is
not used, the aggregate must be
compacted to a minimum 85%
standard proctor density per
ASTM D698, or as required by the
authority having jurisdiction.
Concrete pad or aggregate surface
must be leveled flat and free of
voids to conform to the basin
bottom. Basin bedding depth
should be calculated such that the
basin top will protrude 3" above
the normal grade upon final
installation.
Step 2
Lifting of the basin may be
done with a nylon or other non-
damaging type material sling. Do
not wrap a chain or steel cable
around the basin as damage may
result. The two t-shaped molded-
in lugs (polybasin only) may be
used for lifting the basin. Do not
attach lifting mechanism around
the discharge hub or electrical
hub.
Determine point at which influent
line will enter basin and, using
a properly maintained piloted
hole saw
sized per chart below,
drill a hole through the basin
wall. If using a fiberglass basin,
clean cut hole and apply a sealant
coating to the cut section to
prevent fiberglass deterioration.
Insert the inlet grommet into the
drilled hole.
PIPE SIZE
HOLE SAW
DIAMETER
*
3"
4"
4"
5"
6"**
7"
* Contact the factory for availability of
proper size hole saw if necessary.
** 6" pipe size requires use of a
fiberglass basin.
Failure to use a properly piloted
hole saw may result in damage
to basin which may result in
structural failure or serious
leaks.
Step 2
Lubricate inside lip of inlet
grommet with pipe soap. Clean
outer end of influent pipe and
push pipe through grommet.
Ensure pipe does not protrude
inside basin so as to interfere with
pump removal or float operation.
Step 3
Close shut-off valve and make
discharge line connection. It is
strongly recommended that
an additional shutoff valve and
redundant check valve be located
outside the basin at any force main
entrances – check local codes for
specific requirements.
Risk of electrical shock or
electrocution. May result in
serious injury or death or fire
hazard. Failure to properly
support electrical conduit,
lines and connections may
result in structural failure.
Electrical connections may be
damaged exposing live electrical
connections.
If the basin is not tied down
during installation, rain or
flood conditions may cause the
basin to float upward, causing
damage to the basin or basin
con nec tions. Claims for this type
of damage cannot be processed
by Hydromatic.
Step 3
Lower the basin into excavation,
position and level properly.
Mount basin to base anchor bolts
if an antiflotation tie-down kit
is used. If basin is fiberglass,
inspect basin and seal off any cuts
or scratches to prevent fiberglass
deterioration.
Influent and
Discharge
Connections for
Fiberglass Basins
Step 1
An inlet grommet is the standard
supplied influent connection
device. If another type of inlet
hub is used, refer to the directions
included with the hub.