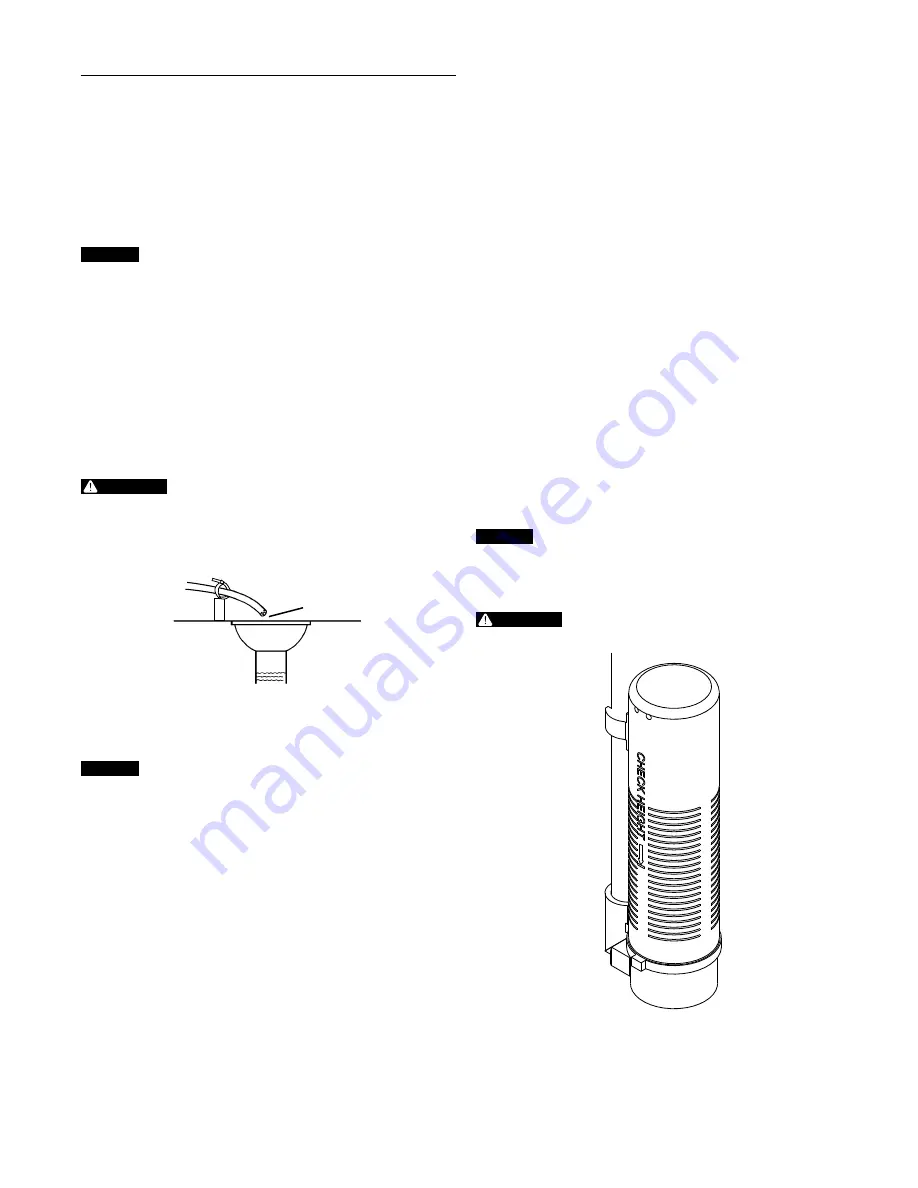
PENTAIR FLECK 5000 Control Valve Service Manual
•
5
INSTALLATION INSTRUCTIONS
Water Pressure
A minimum of 20 psi (1.4 bar) of water pressure is required for
regeneration valve to operate effectively.
Electrical Facilities
An uninterrupted alternating current (A/C) supply is required.
NOTE:
Other voltages are available. Please make sure your
voltage supply is compatible with your unit
before installation.
CAUTION
For dry installation location use only.
Existing Plumbing
Condition of existing plumbing should be free from lime and iron
buildup. Piping that is built up heavily with lime and/or iron should
be replaced. If piping is clogged with iron, a separate iron filter
unit should be installed ahead of the water softener.
Drain Line Connection
Secure the end of the drain line to prevent it from moving.
NOTE:
Waste connections or drain outlet should be designed
and constructed to provide for connection to the
sanitary waste system through an air-gap of 2 pipe
diameters or 1 inch (22 mm), whichever is larger.
WARNING:
Never insert drain line directly into a drain,
sewer line, or trap (Figure 8). Always allow
an air gap between the drain line and the
wastewater to prevent the possibility of sewage
being back-siphoned into the conditioner.
Right Way
Air Gap
Drain
By-Pass Valves
Always provide for the installation of a by-pass valve if unit is not
equipped with one.
CAUTION
Water pressure is not to exceed 125 psi (8.6 bar), water
temperature is not to exceed 110°F (43°C), and the unit
cannot be subjected to freezing conditions.
Installation Instructions
1.
Place the softener tank where you want to install the unit
making sure the unit is level and on a firm base.
2.
During cold weather, the installer should warm the valve to
room temperature before operating.
3.
All plumbing should be done in accordance with local
plumbing codes. The pipe size for residential drain line
should be a minimum of 1/2 inch (13 mm). Backwash flow
rates in excess of 7 gpm (26.5 Lpm) or length in excess of
20 feet (6 m) require 3/4 inch (19 mm) drain line. Commercial
drain lines should be the same size as the drain line flow
control.
4.
Refer to the dimensional drawing for cutting height of the
distributor tube. If there is no dimensional drawing, cut the
distributor tube flush with the top of the tank.
5.
Lubricate the distributor o-ring seal and tank o-ring seal.
Place the main control valve on tank.
NOTE:
Only use silicone lubricant.
6.
Solder joints near the drain must be done prior to connecting
the Drain Line Flow Control fitting (DLFC). Leave at least
6 inches (15 cm) between the DLFC and solder joints when
soldering pipes that are connected on the DLFC. Failure to do
this could cause interior damage to the DLFC.
7.
Plumber tape is the only sealant to be used on the drain
fitting. The drain from twin tank units may be run through a
common line.
8.
Make sure that the floor is clean beneath the salt storage
tank and that it is level.
9.
Place approximately 1 inch (25 mm) of water above the grid
plate. If a grid is not utilized, fill to the top of the air check
(Figure 1) in the salt tank. Do not add salt to the brine tank at
this time.
10. On units with a by-pass, place in by-pass position. Turn on
the main water supply. Open a cold soft water tap nearby and
let run a few minutes or until the system is free from foreign
material (usually solder) that may have resulted from the
installation. Once clean, close the water tap.
11.
Slowly place the by-pass in service position and let water
flow into the mineral tank. When water flow stops, slowly
open a cold water tap nearby and let run until the air is
purged from the unit.
12. Plug unit into an electrical outlet.
NOTE:
All electrical connections must be connected
according to local codes. Be certain the outlet
is uninterrupted.
CAUTION
• Do not exceed 125 psi water pressure
• Do not exceed 110°F (43°C) water temperature
• Do not subject unit to freezing conditions
WARNING:
The system MUST be depressurized before
removing any connections for servicing.
Figure 2
Residential Air Check Valve