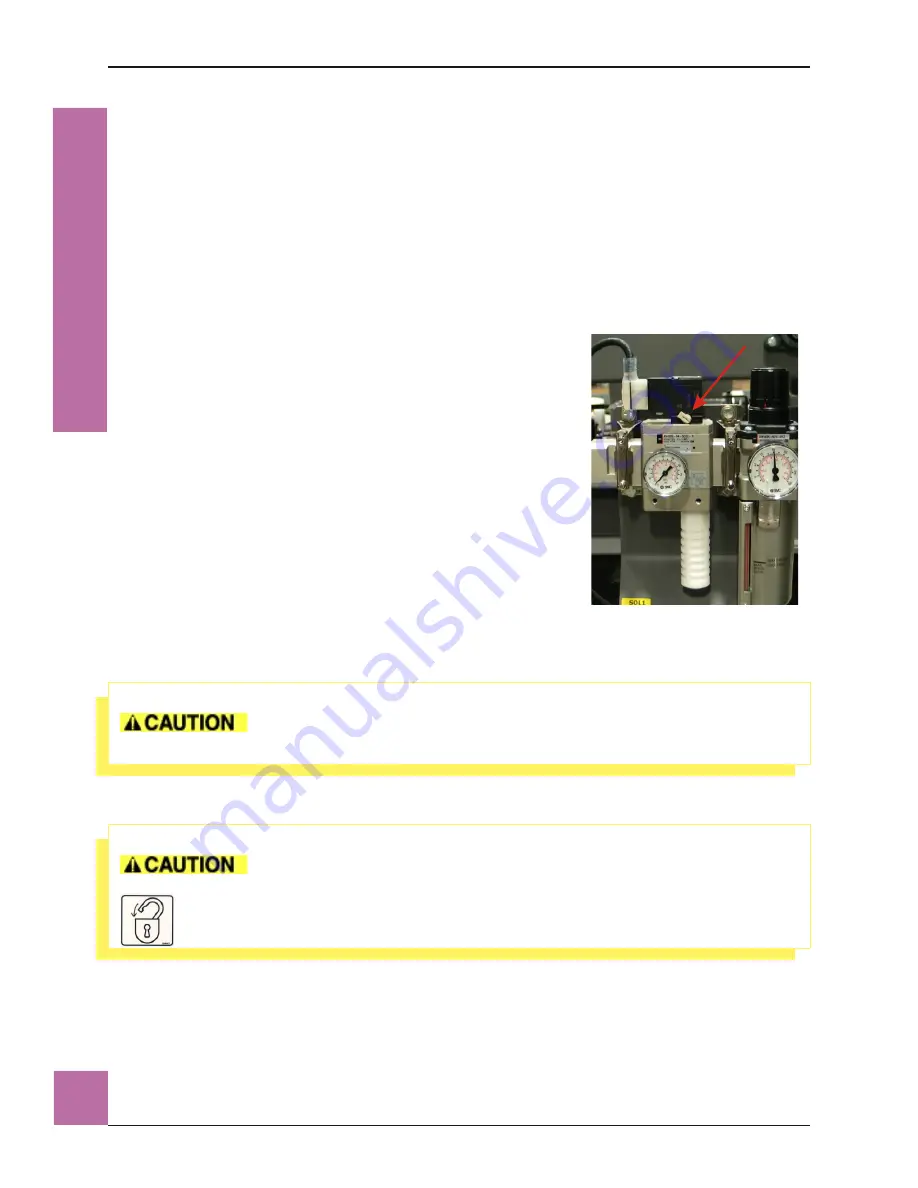
Air Supply
The machine requires a clean, dry air supply with a constant pressure of 80 PSI. The
volume of air required is 0.744 SCF/Cycle at 80 PSI.
Note:
This machine is equipped with an electrical air supply and dump valve. Pressing
the E-stop button exhausts compressed air in the machine circuit. Pulling out the
E-stop button and pushing the Start button re-energizes the system.
1.
Once air is connected, manually lock air (open) onto machine. Check or
perform a pneumatic integrity test of all hoses,
fittings, and cylinders. Correct any
discrepancies found to leak or discharge air
from pneumatic system.
2.
Use a minimum ¾” NPT air line and connect
plant air to the machine.
Note:
Size the air line to match the inlet line on the air
prep unit.
Final Checks
Perform a motor rotation check of the conveyor motor. If the
motor initially runs in the wrong direction, reverse the polarity.
Recheck the motor.
1.
Verify machine and case/tray set up before attempting to run case/tray.
Before making any adjustments to the machine: Turn off main
power; turn off air supply; follow lock out/tag out procedures.
CE35-T Case Erector
Operations Manual
3/2/2010
M-CE35T-2c Horiz Mag
26
n
oi
t
al
l
at
s
nI
Fig. 16: Manual Air Lock
Button