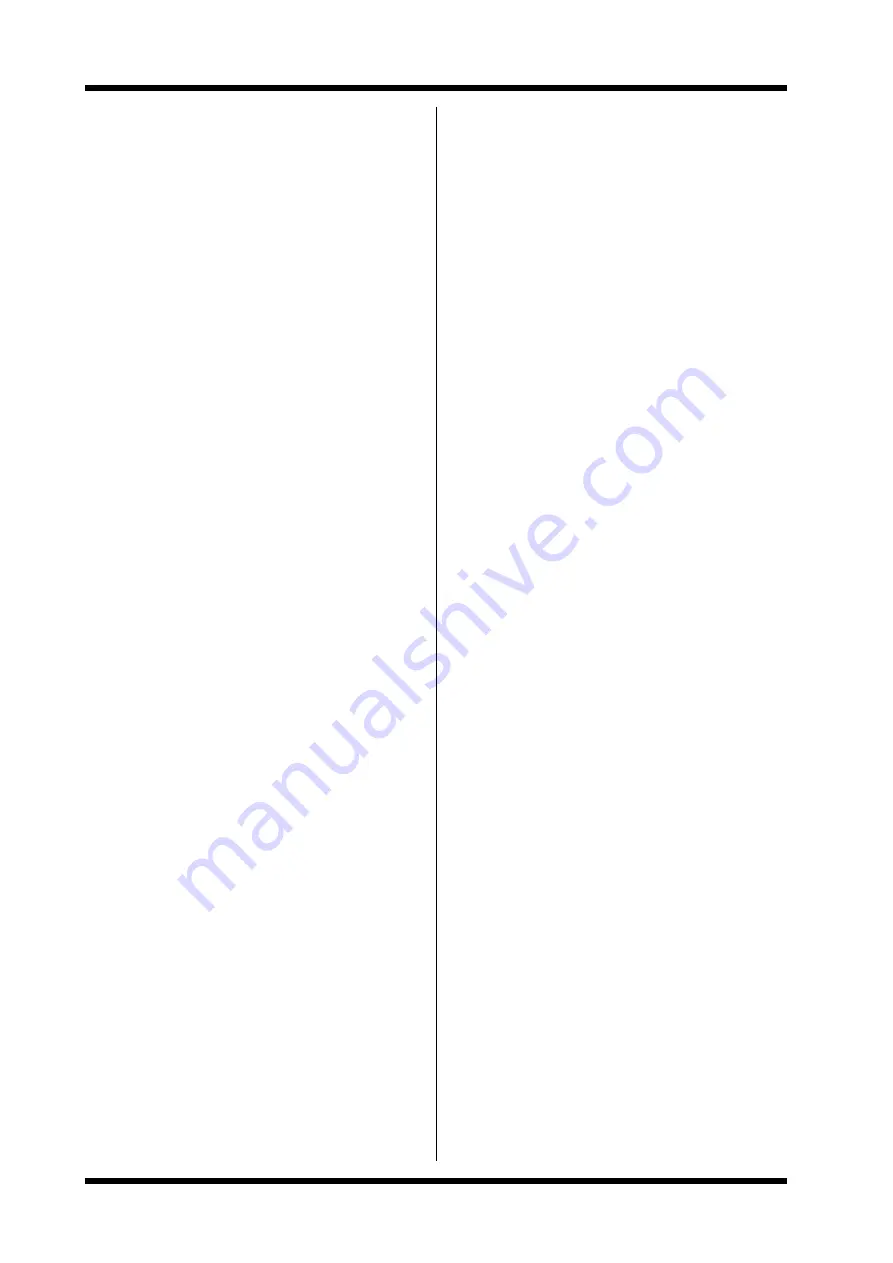
Microdrive Series Instruction Manual
4201-109 Rev I
38
Additional LEDs on Microdrive-i -
LED
GREEN - TRANSISTOR
OVERLOAD U+, U-, V+, V-, W+, W-
Actual Indication
IGBT being driven.
Notes:
This is not the same as transistor
conducting.
LED
RED - TRANSISTOR OVERLOAD
U+, U-, V+, V-, W+, W-
Actual Indication
Extreme current overload of
indicated IGBT.
Implication
Output short circuit or internal IGBT
failure.
LED
+24V SUPPLY
Actual Indication
+24V supply is present.
LED
+17.5V
Actual Indication
+17.5V CT supply present (check
F3, 2A, +24V supply).
LED
-12.5V
Actual Indication
-12.5V CT supply present (check F4,
500mA, -12.5V supply).
LED
SOFT CHARGE
Actual Indication
Soft charge SCR trigger supply is
present (check F5, 5A, SCR gate
supply).
1.7.5 FUSE FAILURE
The Microdrive incorporates electronic protection. The
fuses are for safety back-up.
Refer to the appropriate UD3 or UDi section for fuse details.
Microdrive-3 (UD3):
Supply fuses -
fitted by customer at point of supply.
Possible reason for failure
Wrong fuses; supply surge; age or cyclic
stress failure; fault in supply cable to UD3;
UD3 failure.
Action
Check cable, UD3. Isolate UD3 and replace
fuses. Test. If OK reconnect UD3 and
retest. If failure persists replace UD3 or
request service.
F1 +24V supply fuse
-
fitted on UD3 power board.
Possible reason for failure
Overload of +24V supply or low voltage
supplies derived from +24V; faulty fan; faulty
control PCB.
Action
Check UD3 for obvious faults to low voltage
DC supplies; replace with correct fuse;
check operation; if failure persists replace
UD3 or request service.
F2 2A SMPS DC bus fuse -
fitted on UD3 power board;
UD3-31
to UD3-70.
Possible reason for failure
Fault in switch mode power supply.
Action
WARNING:
This fuse MUST NOT be replaced with a
glass fuse (a glass fuse will rupture and
cause catastrophic damage). Use only the
specified 440Vac 2A ceramic fuse. Replace
fuse. If failure persists replace UD3 or
request service.
Microdrive-i (UDi):
Supply fuses -
at point of input termination to the
Microdrive.
Possible reason for failure
Supply surge; age or cyclic stress failure;
wrong fuses; fault in supply cable to
Microdrive; Microdrive failure.
Action
Check input cables and Microdrive for any
signs of a fault. Isolate Microdrive and
replace fuses. Test. If OK, reconnect
Microdrive and retest. If failure persists
replace Microdrive, or request service.
UDi DC bus fuses
Possible reason for failure
Supply surge; age or cyclic stress failure;
wrong fuses; fault in output cable to motor;
UDi failure.
Action
Isolate UDi. Check output cables; check
UDi. Unless confident fault found and
cured, contact Service Agent. Replace
fuses. Reconnect UDi and test. If failure
persists replace UDi, or request service.
Summary of Contents for D3-2.5
Page 2: ...Microdrive Series Instruction Manual 4201 109 Rev I 4201 003 Rev A Page 2 of 12...
Page 6: ...Microdrive Series Instruction Manual 4201 109 Rev I 4201 003 Rev A Page 6 of 12...
Page 12: ...Microdrive Series Instruction Manual 4201 109 Rev I 4201 003 Rev A Page 12 of 12...
Page 55: ...Microdrive Series Instruction Manual 4201 109 Rev I 55...
Page 74: ...Microdrive Series Instruction Manual 4201 109 Rev I 74...
Page 75: ...Microdrive Series Instruction Manual 4201 109 Rev I 75...
Page 76: ...Microdrive Series Instruction Manual 4201 109 Rev I 76...
Page 77: ...Microdrive Series Instruction Manual 4201 109 Rev I 77...
Page 78: ...Microdrive Series Instruction Manual 4201 109 Rev I 78...
Page 79: ...Microdrive Series Instruction Manual 4201 109 Rev I 79...
Page 80: ...Microdrive Series Instruction Manual 4201 109 Rev I 80...
Page 81: ...Microdrive Series Instruction Manual 4201 109 Rev I 81...
Page 82: ...Microdrive Series Instruction Manual 4201 109 Rev I 82...
Page 83: ...Microdrive Series Instruction Manual 4201 109 Rev I 83...
Page 112: ...Microdrive Series Instruction Manual 4201 109 Rev I 112...
Page 113: ...Microdrive Series Instruction Manual 4201 109 Rev I 113...