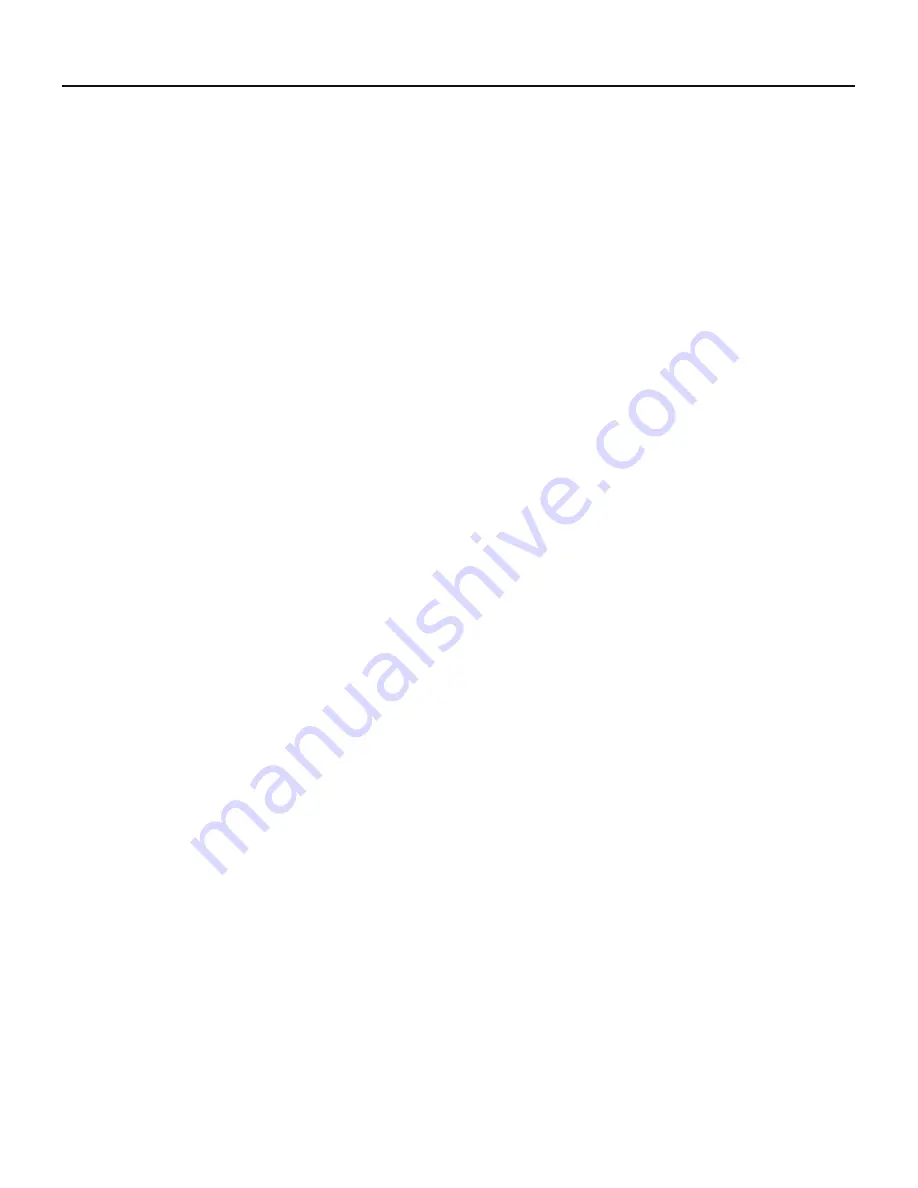
7
TABLE OF CONTENTS
8.6 - Air inlet pipe materials ........................................................................................................................................ 39
8.6.1 - Sealing of Type “B” double-wall or galvanized air inlet pipe material .................................................... 39
8.6.2 - Sealing of PVC, CPVC or ABS air inlet pipe ......................................................................................... 39
8.7 - PVC/CPVC vent piping materials ....................................................................................................................... 40
8.7.1 - Installing PVC/CPVC vent and air piping .............................................................................................. 40
8.7.2 - PVC/CPVC air intake/vent connections ................................................................................................ 40
8.8 - Flue terminal location in compliance with CAN/CSA B149 ................................................................................ 42
8.9 - Single pipe vent (not sealed combustion) .......................................................................................................... 43
8.9.1 - Combustion Air and Ventilation openings ............................................................................................. 43
8.9.2 - Determine location ................................................................................................................................ 44
8.10 - Sidewall termination - Two pipes ...................................................................................................................... 45
8.10.1 - Vent/air termination ............................................................................................................................. 45
8.10.2 - Determine location .............................................................................................................................. 45
8.10.3 - Prepare wall penetrations ................................................................................................................... 47
8.10.4 - Termination and fi ttings ....................................................................................................................... 47
8.10.5 - Multiple vent/air terminations .............................................................................................................. 47
8.11 - Sidewall termination - Concentric vent ............................................................................................................. 48
8.11.1 - Description and usage ........................................................................................................................ 48
8.11.2 - Sidewall termination installation .......................................................................................................... 48
8.11.3 - Multiventing sidewall terminations ....................................................................................................... 49
8.12 - Vertical termination - Two pipes ....................................................................................................................... 50
8.12.1 - Determine location .............................................................................................................................. 50
8.12.2 - Prepare roof penetrations ................................................................................................................... 50
8.12.3 - Termination and fi ttings ....................................................................................................................... 50
8.12.4 - Multiple vent/air terminations .............................................................................................................. 51
8.13 - Vertical termination - Concentric vent .............................................................................................................. 52
8.13.1 - Description and usage ........................................................................................................................ 52
8.13.2 - Determine location .............................................................................................................................. 52
8.13.3 - Vertical termination installation ........................................................................................................... 52
8.13.4 - Multiventing vertical terminations ........................................................................................................ 53
8.13.5 - Alternate vertical concentric venting ................................................................................................... 54
8.14 - Existing vent as a chase .................................................................................................................................. 55
9 - INSTALLATION - Split venting system ................................................................................................................... 56
9.1 - Split system (polypropylene) or AL29-4C (UL 1738/UL C 636) system ............................................................. 56
9.2 - Split system components ................................................................................................................................... 58
9.3 - Split system components ................................................................................................................................... 59
9.4 - Split system: installation examples .................................................................................................................... 60
10 - INSTALLATION - Coaxial venting system ............................................................................................................ 61
10.1 - Coaxial system ................................................................................................................................................. 61
10.2 - Coaxial system components ............................................................................................................................ 62
10.3 - Coaxial system components ............................................................................................................................ 63
10.4 - Coaxial system: installation examples ............................................................................................................. 64
11 - OPERATING ............................................................................................................................................................ 65
11.1 - Operating .......................................................................................................................................................... 65
11.1.1 - User instructions ................................................................................................................................. 65
11.1.2 - Filling the condensate trap .................................................................................................................. 65
11.1.3 - Filling the heating system .................................................................................................................... 65
11.1.4 - Filling the domestic hot water heat exchanger .................................................................................... 66
11.1.5 - Auto-purging the heating system ......................................................................................................... 66
Summary of Contents for Peerless Combi 160
Page 3: ...3 SAFETY INSTRUCTIONS...
Page 97: ...97 13 MAINTENANCE...
Page 105: ...105 NOTES...
Page 106: ...106 NOTES...