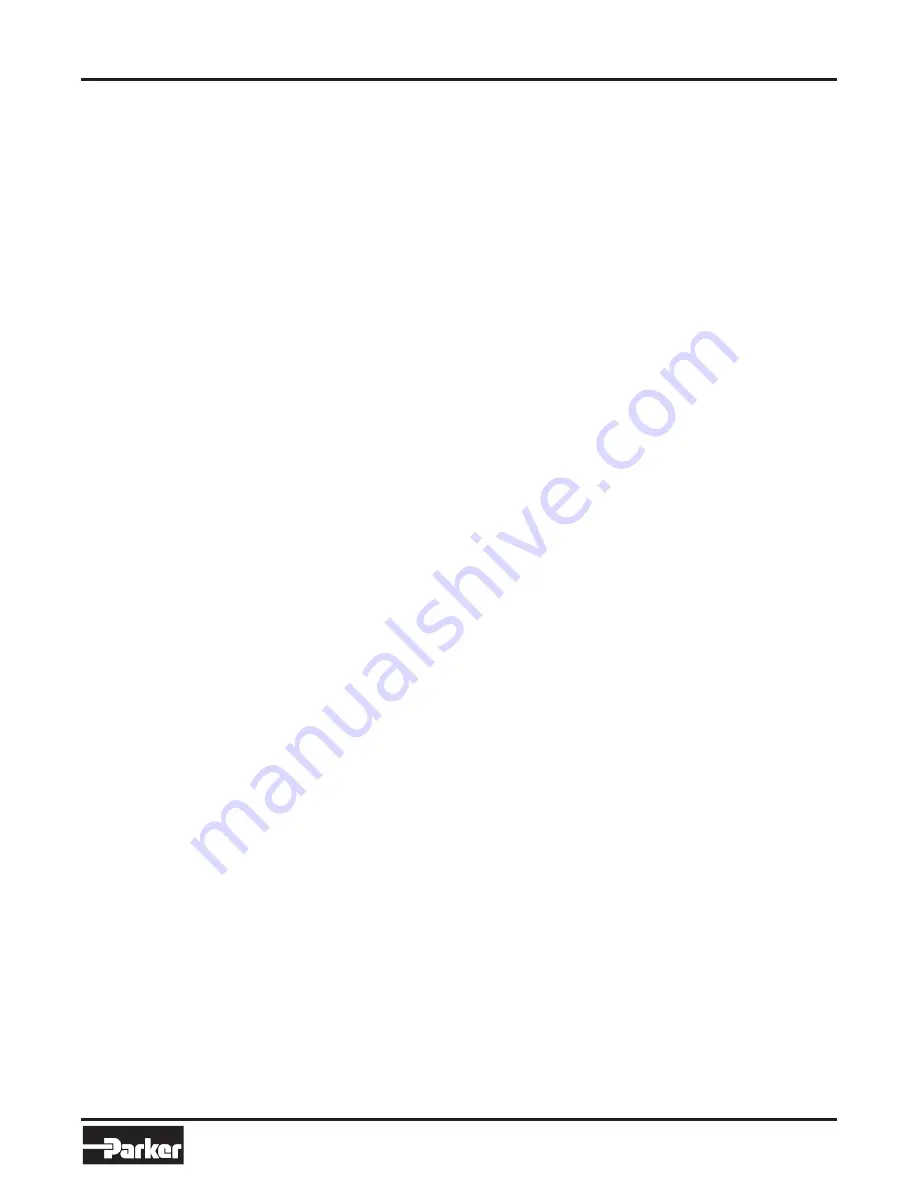
Parker Hannifin Corporation
Gear Pump Division
Kings Mountain, North Carolina USA
14
Petroleum Oils (Mineral-Based)
Viscosity Recommendations
• Optimum operating viscosity is considered
to be about 100 SUS (20 cSt).
• Minimum approximately 50 - 60 SUS ( 7.5 - 10 cSt )
Maximum at start up: approximately 7500 SUS (1600 cSt)
Recommended Viscosity Grades
Viscosity at
Viscosity at
Grade
100°F (40°C)
210°F (100°C)
ISO 32
165 SUS (32 cSt)
44 SUS (5 cSt)
ISO 46
240 SUS (46 cSt)
49 SUS (7 cSt)
SAE 10
150 SUS (32 cSt)
41 SUS (4 cSt)
SAE 20
300 SUS (71 cSt)
51 SUS (7 cSt)
Other Desirable Properties
Viscosity Index: 90 minimum
Aniline Point: 175 minimum
Additives Usually Recommended
Rust and Oxidation (R & O) Inhibitors
Foam Depressant
Note:
Antiwear (AW) additives are not necessarily recom
-
mended. In some instances the presence of zinc compounds
can actually be harmful to copper, bronze, or brass compo-
nents used in the system. The use of AW oil is optional with
our gear units.
General Recommendations
High quality hydraulic oils are essential for satisfactory per-
formance and long life of any hydraulic system. Such oils are
usually prepared from highly refined, turbine oil stocks with
which select additives are compounded. We suggest follow-
ing the manufacturer’s specifications or the recommendations
of a reputable oil supplier for the specific oil requirements on
your machine.
A high viscosity oil will generally give better performance
and life than a thin oil. Oil of around 100 SUS (20 cSt) will
give optimum performance. Your selection should be as near
to optimum as possible at operating temperature but not
so heavy at start-up as to cause cavitation. Cold start-up
procedures which allow the use of heavier oils should prove
worthwhile by increasing pump life. The oil must be clean and
contain less than 0.1% water.
Operating Temperature
The optimum oil operating temperature is in the range of
120°-140°F (49°-60°C). Oil operating temperature should
not exceed 200°F (93°C) with a maximum of 180°F (82°C)
generally recommended. If the oil temperature will be above
180°F (82°C) for significant periods of time, then Viton (FKM)
seals should be used. High temperatures may result in rapid
oil deterioration and may point out the need for an oil cooler
or a larger reservoir. The nearer to optimum temperature,
the longer the service life will be of the oil, pump and other
components.
Cold Weather Operation
Oils for use in cold weather should have a viscosity not
exceeding 7500 SUS (1620 cSt) at the minimum start up
temperature and a pour point of at least 20°F (7° C) below
that temperature. Experience on the Alaskan North Slope has
been satisfactory without using special oils or fluids. Start-up
procedures must allow for a gradual warm-up and equipment
should not be operated at full pressure until the oil reaches a
reasonably fluid state.
Inlet Vacuum
Vacuum measured at the inlet port of the pump generally
should not exceed 5 in. (13 cm) Hg. Higher vacuum can result
in cavitation which may severely damage the pump. A usually
acceptable rule of thumb is that the inlet line velocity should
not exceed 8 fps (2.5 m/s). A long inlet line or the use of
several fittings may necessitate increasing the line size. We
suggest that each inlet port of a tandem pump have its own
line from the reservoir.
Reservoir
Reservoir capacity in gallons should at least equal total
pump output in GPM When filling the reservoir, oil should
pass through a 100-mesh screen. Pour only clean oil from
clean containers into the reservoir. The reservoir should have
a breather to allow air in or out. The filler cap and breather
should be sealed to prevent moisture from entering. A hydrau-
lic oil water content of as little as 0.1% can cause damage to
hydraulic components
Filtration
Good filtration assures improved service life at today’s high
operating pressures. System filtration is recommended that
will maintain a contamination level according to ISO 4406:
21/19/16 for 2000 psi (140 bar), 19/17/14 for 3000 psi (210
bar) and 17/15/12 for 4000 psi (275 bar) The specific filter
recommendation should come from your equipment manufac-
turer or filter supplier
A 100 mesh screen should generally be used in the suc-
tion line leading to the pump. It should be of sufficient size to
handle twice the pump capacity. The screen must be cleaned
and checked regularly to avoid pump and system damage
Oil and filters should be changed on a regular schedule and
the system flushed in accordance with the original equipment
manufacturer’s recommendations. Reservoir air breather
filters should be cleaned periodically
Filtration is not a substitute for practicing cleanliness
and proper preventive maintenance
Catalog HY09-SM500/US
Hydraulic Oil Recommendation
PGP/PGM500 Series
Service Manual