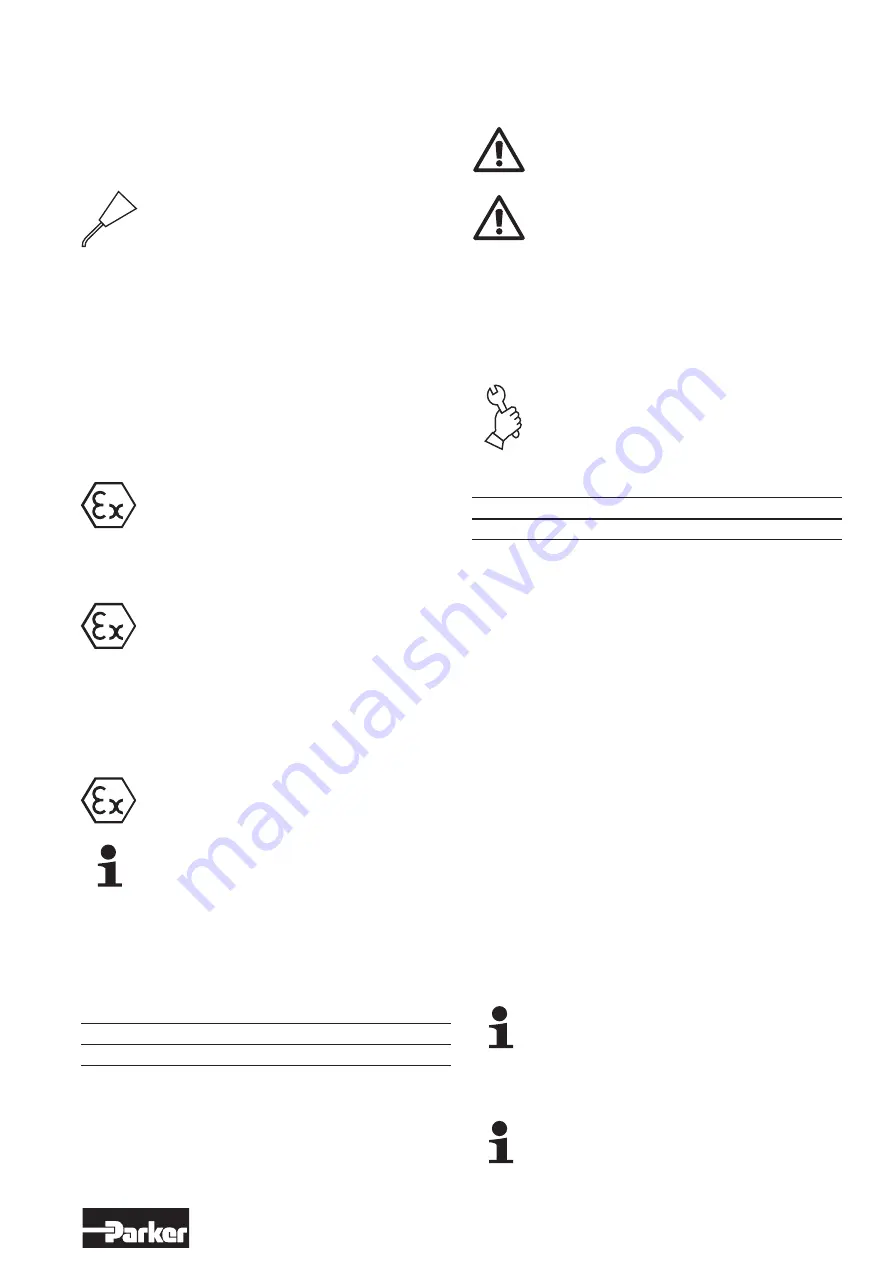
7
www.parker.com/euro_pneumatic
7. Maintenance and Upkeep
The first maintenance should be performed after 500 operating
hours with non-lubricated air and after 1,000 operating hours
with lubricated air. Thereafter, we recommend adjusting the
maintenance intervals to the general usage and wear condition
of the motor as well as the application area.
Lubrication
If the air motor is sufficiently lubricated, it requires little
maintenance. The air motor should be regularly checked
in regards to excessive noise and/or if the gears show an
increased play.
The planetary gears and the bearings have to be
sufficiently greased (see chapter 8.3 “Assembly”).
After every maintenance session, the planetary gears have
to be cleaned and re-greased.
Clean filter of the maintenance unit and bleed water
condensation. If necessary, replace the filter to protect
the motor against blockage caused by dirt particles in the
supply air.
Regularly check the oil-level in the oiler and refill oiler as
needed.
Lubricants
Use only lubricants approved by the manufacturer.
Bearing Exchange
To assure a continued low surface temperature if motor is
used in an Ex-area, observe the following:
• Replace the bearings in the gearing after 10-Million
rotations.
• Replace the bearings in the motor after 8,000 operating
hours.
Worn Vanes
Our experience has shown that the vanes (in a complete
set) have to be replaced latest after 2,000 operating hours.
This interval may be longer or shorter, depending on the air
quality and application area.
Loss of Power
If the motor does not operate correctly, after being used
for a long time, then the flats of the vanes have been
clogged in the rotor-slots by the oils resin residue. In such
cases, it is necessary to clean the motor.
Seal Rings
The failure of a seal ring causes the grease in the gearing
to prematurely dry out. Replace any brittle or damaged
seal ring immediately.
If the motor is maintained on a regular basis, then the wear
and tear on the movable parts is minimal. The wear mainly
depends on the operating speed, the air pressure and the
lubrication. We recommend sending a failed air motor to
us for repair. We have all the necessary special repair tools
for the disassembly, original spare parts and the trained
repair specialists that can adjust the air motor to the
correct gap play. The gap play determines the motors
power, efficiency and life expectancy.
7.1 Wear Parts
Quantity
Description
Please refer to the technical catalog PDE2539TC
8. Disassembly – Assembly
( Spare Part Drawing/s)
Disassembly and assembly of the air motor may
only be performed by Parker or qualified persons /
technical experts.
The air motor may start and cause a hand injury.
Disconnect air motor from the air supply.
After every maintenance session, verify that equipment
runs to the required specifications.
Principally, use only Parker original spare parts. Otherwise,
a reduction of equipment power-output and an increased
maintenance requirement occurs.
If Non-Parker parts are installed, then Parker is justified to
avoid any existing warranty and liability obligations.
Only use original Parker service tools in order to avoid
causing damage.
8.1 Service Tools (Optional Equipment)
Name
No specific tools are required
8.2 Disassembly
1. Unscrew gear housing from motor housing
(AF 32, right-hand thread).
2. Push the motor parts out of the motor housing.
3. Remove support disc and o-ring.
4. Clamp motor on its rotor cylinder into fixing device.
5. Pull off shaft-side bearing cover from rotor.
6. Remove rotor cylinder.
7. Take out the 5 vanes from the rotor.
Basically, replace the vanes.
Exchange only complete sets of vanes (5 pieces).
8. Pull off air-connecting side bearing cover from rotor.
9. Press the two ball bearings from the bearing covers
8.3 Assembly
Lubrication
• Fill space areas of the planetary gear with 1/3rd of
Parker-grease for the use in the food industry.
• Sufficiently grease the bearings.
• Use only lubricants approved by the manufacturer
1. Clean rotor.
2. Press the ball bearings into the two bearing covers.
3. Press the shaft-side bearing cover with the ball bearing
on the rotor.
4. Insert 5 new vanes into the rotor.
5. Put the rotor cylinder over the rotor.
After assembly the bearing covers shouldn’t have
any axial gap. The rotor must turn freely.
6. Press air-connecting side bearing cover with ball
bearing on the rotor.
7. Assemble o-ring and support disc.
8. Slide the motor parts (arranged in correct sequence)
into the motor housing.
Bearing needle must engage into the bore of the
motor housing.
9. Tighten motor housing (right-hand thread) onto gear
housing.