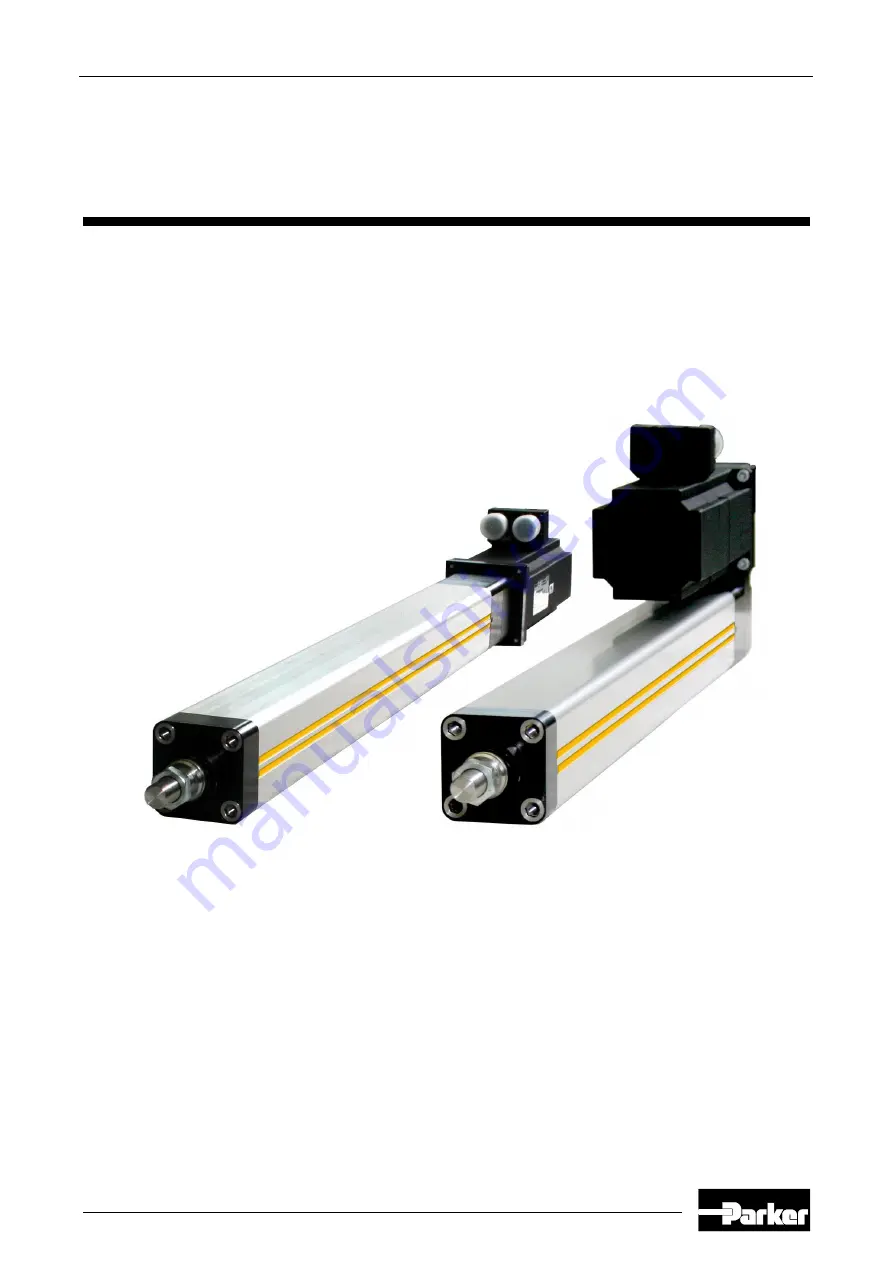
ETH -
Elektrozylinder
Electromechanical
Cylinders
Electromechanical Automation
Technical Changes Reserved
21.11.18 07:42192-550002N2 ETH Mounting instructions March 2011September 2012
Data shown complies with known technical data when printed.
Mounting instructions
ETH Manual - Installation, Commissioning, Maintenance and Repair
ETH - Electro Cylinder
Parker High Force Electro Thrust
Cylinder
192-550002N2.EMN ETH Mounting instructions
Revision: B November 21,2018