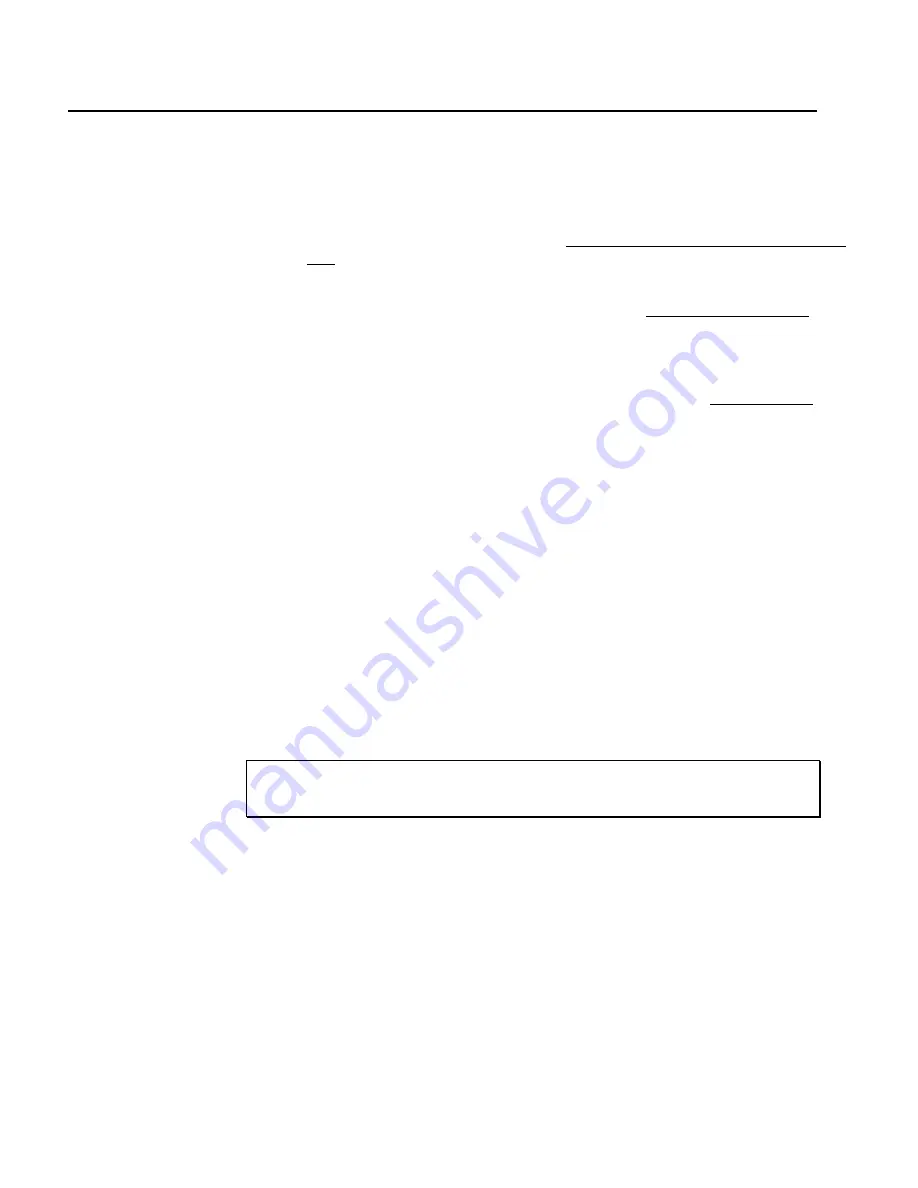
36
ζ
ZETA6xxx Installation Guide
Optimizing System Performance (OPTIONAL)
The ZETA6xxx is equipped with three damping circuits that minimize resonance and ringing,
and thus enhance stepper performance:
For a theoretical discussion about these three circuits and how they minimize resonance and
ringing, refer to Appendix A.
NOTE: You need to "match the motor to the ZETA6xxx” before you can configure active
damping or electronic viscosity. Refer to the matching procedure on page 30.
Configuring Active Damping
Before You Start
• Couple the motor to the load (see pages 33-35 for details). Active damping must be
configured under the normal mechanical operating conditions for your application.
Follow these steps to configure the active damping circuit.
1. Verify Correct Drive/Motor Matching
See Matching the Motor to the ZETA6xxx earlier in this chapter. To be fully effective, the active
damping circuit requires proper matching. If you are replacing a component (new drive or motor in
an existing application), you must rematch your system.
2. Verify Correct DIP Switch Settings
Anti-Resonance
SW2-#2
switch in OFF position
Inductance
SW2-#7 - #8
set for your motor
Static Torque
SW2-#9 - #12
set for your motor
•
Anti-Resonance – General-purpose damping circuit. The ZETA6xxx ships from the factory
with anti-resonance enabled (see page 7 ). No configuration is necessary. Anti-resonance
provides aggressive and effective damping at speeds greater than 3 revolutions per second
(rps). If you are using a high-inductance motor (not applicable to O, R or T motors), you
should disable anti-resonance with the DIP switch SW2-2.
•
Active Damping – Extremely powerful damping circuit at speeds greater than 3 rps. The
ZETA6xxx ships from the factory with active damping disabled. To enable active damping
and optimize it for a specific motor size and load, refer to the Configuring Active Damping
procedure below.
•
Electronic Viscosity – Provides passive damping at lower speeds (from rest to 3 rps). The
ZETA6xxx ships with electronic viscosity disabled. To enable electronic viscosity and
optimize it for a specific application, refer to the Configuring Electronic Viscosity
procedure below.
The ZETA6xxx
automatically
switches between
the damping
circuits, based upon
the motor’s speed.
Artisan Technology Group - Quality Instrumentation ... Guaranteed | (888) 88-SOURCE | www.artisantg.com