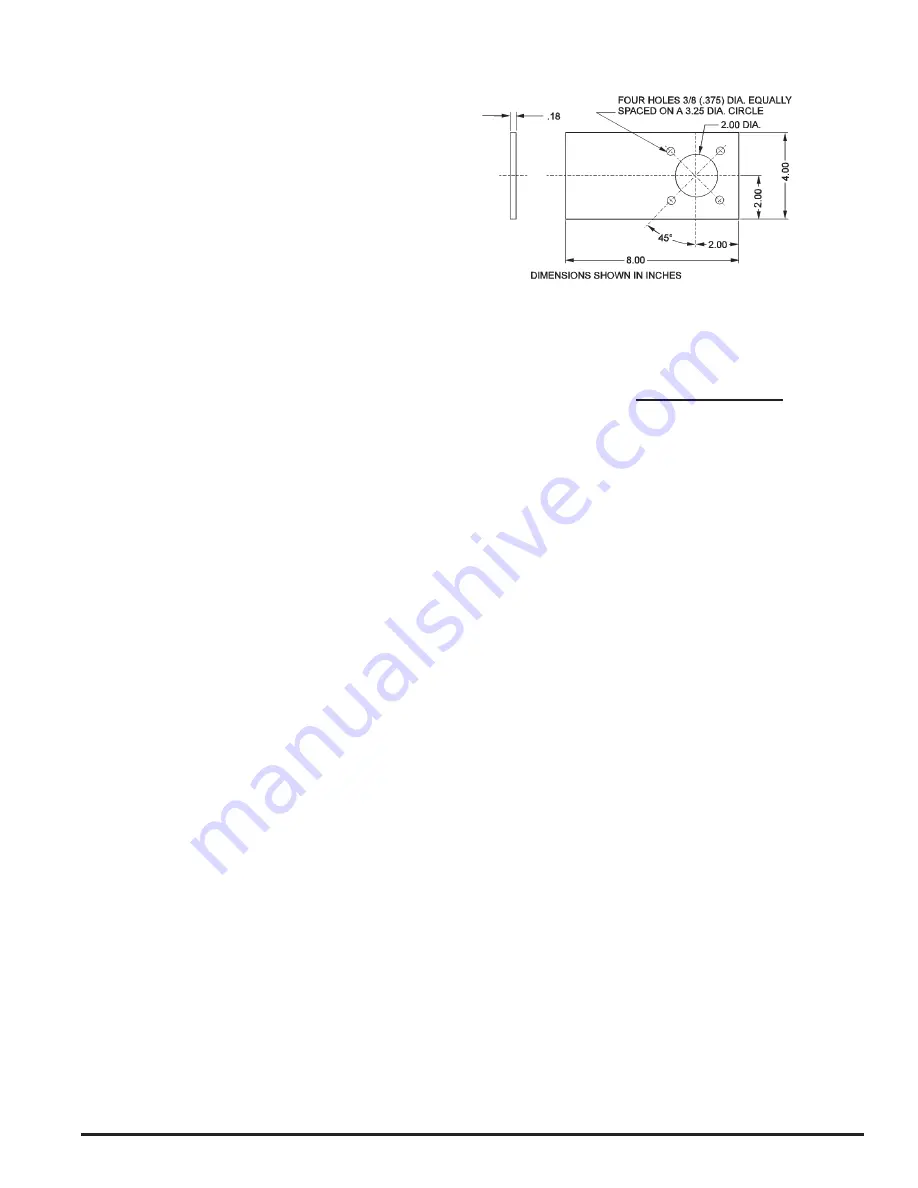
Tools Materials Required for Servicing
HGF Service Manual
HGF service ass'y fixture (See Figure 1)
Clean, petroleum-based solvent
Vise
Pliers
Screw driver
Blunt ended punch
6 pieces of .007 inch (.18 mm) shim stock, approximately
.5 inch (13 mm) wide x 1.5 inch (38 mm) long.
External retaining ring pliers
Tape, plastic electrical
Breaker bar
Sockets: 1/2, 7/8 inch
3/32 inch Allen wrench socket
T-30 Torq socket
Slot type screw driver socket
5/16-24 UNF hex nut (4) required
3/4 inch (19 mm) to 7/8 inch (22 mm) bearing puller
Clean grease
Light weight oil
Torque wrenches: 11–13 in. lb. & 25–35 ft.lb. or Newton Meter
Feeler gauge .003 in. (.08 mm) or .005 in. (.13 mm)
(See disassembly procedure #37)
Electrical continuity checking device
Torque Chart
Exploded View
Part Name
Item Number
Torque
Socket Head Cap Screws
18
11-13 in-lbs. (1.24-1.47 N m)
Plug and O-Ring Ass'y
6, 7
8-12 ft-lbs. (11-16 N m)
Plug and O-Ring Ass'y
6A, 7A
25-35 ft-lbs. (34-48 N m)
Hex Nut 5/16-24
1
18-22 ft-lbs. (25-30 N m)
Jam Nut 5/8-18
41
25-30 ft-lbs. (34-41 N m)
Jam Nut 13/16-20 UNEF
41
30-40 ft-lbs. (41-55 N m)
8
HGF Series Service Procedure
CONVERSIONS
INCHES
mm
0.18
0.375
2.0
3.25
4.0
8.0
4.6
9.5
51.0
82.6
101.6
203.2
Figure 1