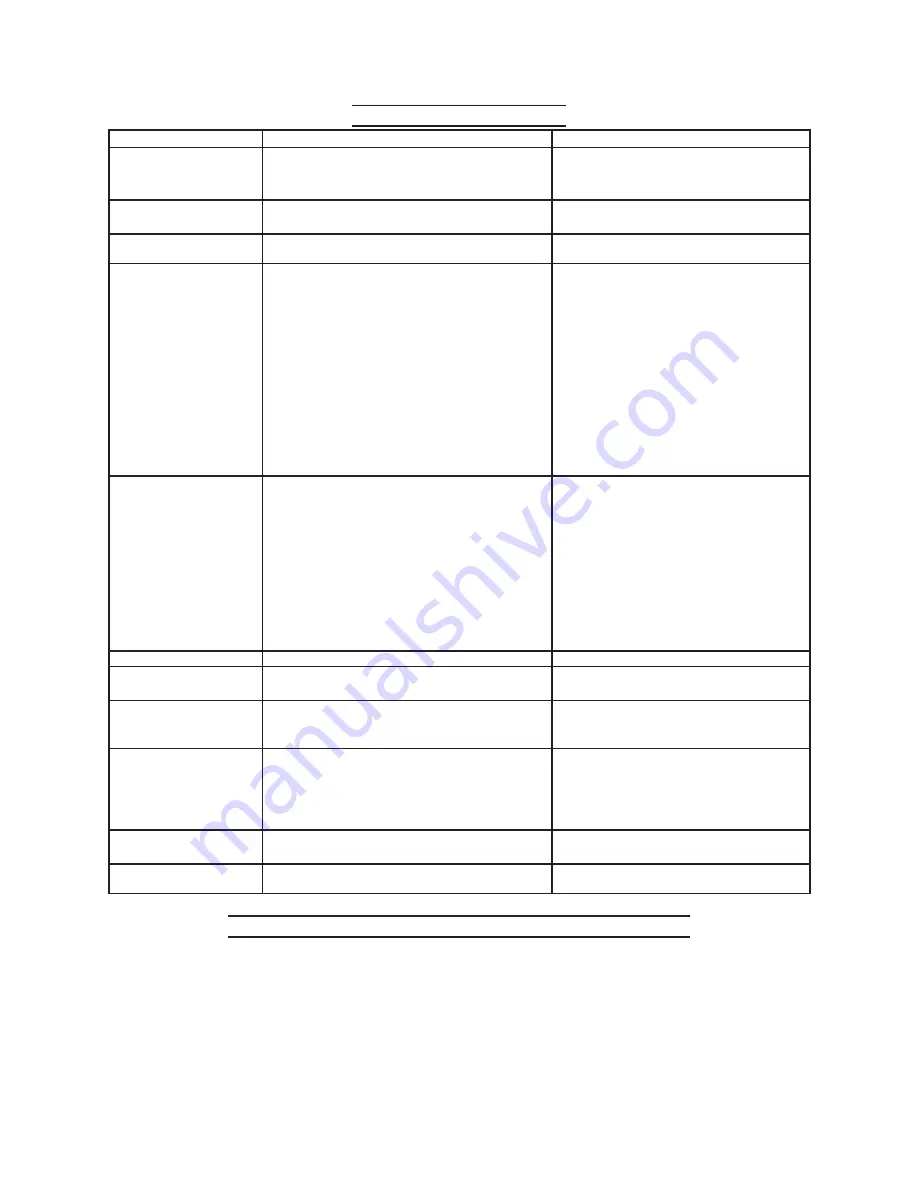
Page 15
SKU 95156
For technical questions, please call 1-800-444-3353.
tROUblESHOOtInG
Problem
Possible cause
Possible Solution
Engine will not stop or
start while operating.
Low oil shutdown.
1.
Engine switch not in the “ON” position.
2.
Pressure build-up in hose.
3.
Fill engine with oil.
1.
Turn switch “ON”.
2.
Squeeze trigger.
3.
Engine is overloaded.
Nozzle partially blocked.
1.
Excessive pressure.
2.
Clean nozzle.
1.
Shorten the spring coil of the reflux valve.
2.
Pressure increases when
gun is closed.
Bypass valve blocked.
Clean the bypass valve.
Engine running but pump
not building maximum
pressure or has irregular
pressure.
Faucet closed.
1.
Unit has been stored in freezing temperatures.
2.
Inadequate water supply.
3.
Water inlet screen clogged.
4.
Kink in garden hose.
5.
Nozzle worn or damaged.
6.
Air in pump.
7.
Adjustable pressure knob not set to maximum
8.
position.
Suction or discharge valves clogged or worn
9.
out.
Bypass valve not operating effectively.
10.
Open faucet.
1.
Thaw out unit completely, including hose
2.
gun and wand.
Provide a minimum 4 GPM @ 20 PSI.
3.
Clean screen.
4.
Straighten hose.
5.
Replace nozzle.
6.
Let run with gun open and wand removed
7.
until steady stream of water is released.
Set to maximum position.
8.
Clean the suction and discharge valves.
9.
Clean the bypass valve.
10.
No intake of chemicals.
Chemical hose not properly inserted into unit.
1.
Tube cracked or split.
2.
Wrong nozzle.
3.
Injector turned off.
4.
Axle of the inner aperture of the three-way cock
5.
is different.
Injection tube strainer clogged.
6.
Nozzle blocked.
7.
Dried chemicals injector.
8.
Push firmly into injector.
1.
Replace tube.
2.
Switch to low pressure nozzle.
3.
Turn collar counterclockwise.
4.
Use a three-way cock with the imbibition
5.
system.
Clean strainer.
6.
Clean nozzle.
7.
Dissolve by running warm water through
8.
the injection tube.
Trigger will not move.
Gun safety lock engaged.
Disengage safety lock.
Water in crankcase.
High humidity.
1.
Worn seals.
2.
Change oil more frequently.
1.
Change the oil seal.
2.
Noisy operation.
Worn bearings.
1.
Air mixed with water.
2.
Change the bearings.
1.
Check inlet lines for restriction and/or
2.
proper size.
Rough/pulsating
operation with pressure
drop.
Inlet restriction.
1.
Unloader faulty.
2.
Air mixed in water.
3.
Check system for stoppage, air leaks,
1.
properly sized inlet plumbing to pump.
Check unloader for proper operation.
2.
Check inlet lines for restriction and/or
3.
proper size.
High crankcase
temperatures.
Wrong grade of oil.
1.
Improper amount of oil in crankcase.
2.
Use recommended oil.
1.
Adjust oil to proper amount.
2.
Engine runs erratically.
Bad fuel.
Drain fuel tank. Drain carburetor bowl. Refill
fuel tank with fresh fuel.
PlEASE REAd tHE FOllOWInG cAREFUlly
THE MANUFACTURER AND/OR DISTRIBUTOR HAS PROVIDED THE PARTS LIST AND ASSEMBLY DIAGRAM IN
THIS MANUAL AS A REFERENCE TOOL ONLY. NEITHER THE MANUFACTURER OR DISTRIBUTOR MAKES ANY
REPRESENTATION OR WARRANTY OF ANY KIND TO THE BUYER THAT HE OR SHE IS QUALIFIED TO REPLACE
ANY PARTS OF THE PRODUCT. IN FACT, THE MANUFACTURER AND/OR DISTRIBUTOR EXPRESSLY STATES
THAT ALL REPAIRS AND PARTS REPLACEMENTS SHOULD BE UNDERTAKEN BY CERTIFIED AND LICENSED
TECHNICIANS, AND NOT BY THE BUYER. THE BUYER ASSUMES ALL RISKS AND LIABILITY ARISING OUT OF
HIS OR HER REPAIRS TO THE ORIGINAL PRODUCT OR REPLACEMENT PARTS THERETO, OR ARISING OUT
OF HIS OR HER INSTALLATION OF REPLACEMENT PARTS THERETO.