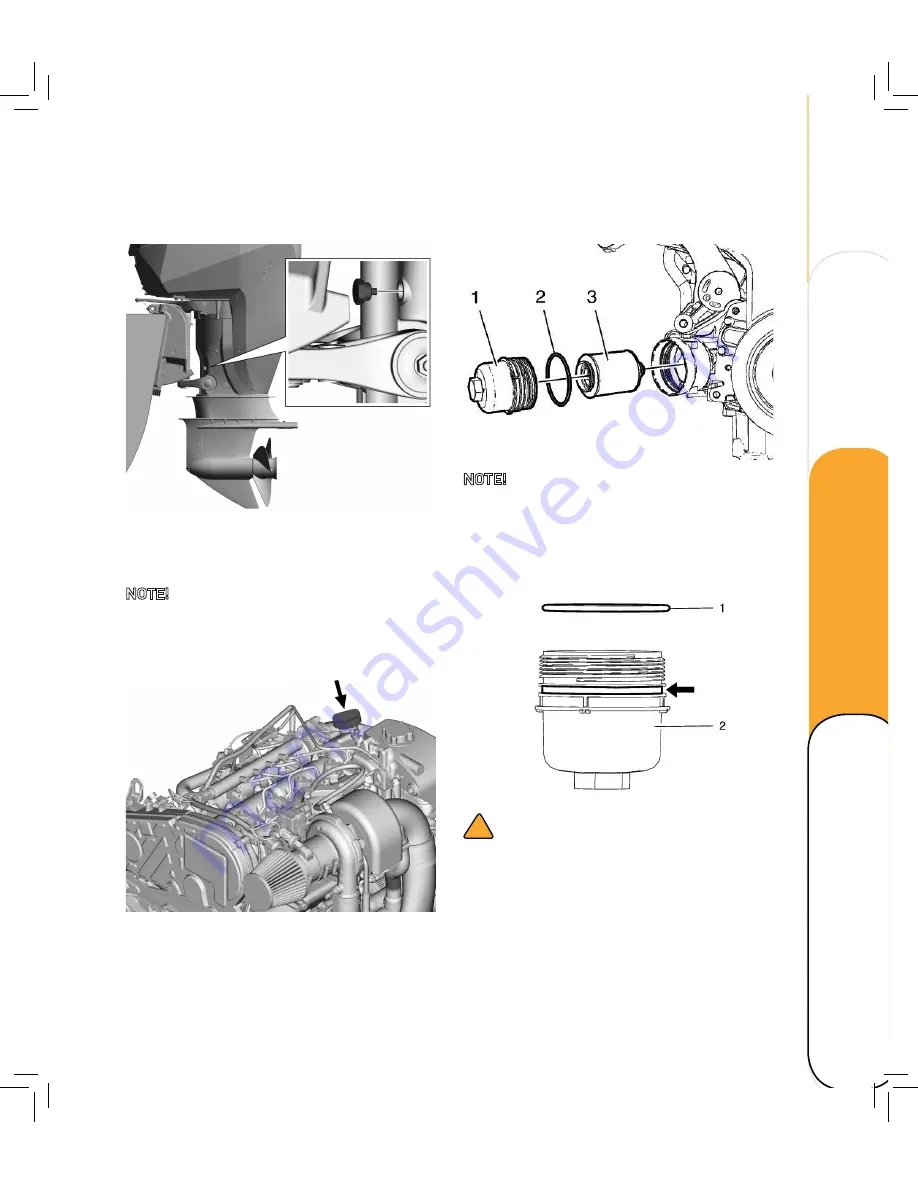
45
Change engine oil
1.
Remove the oil draining plug and washer.
2.
Drain the engine oil into a suitable
container.
NOTE!
Discard used oil according to local
legislation.
3.
Fit a
NEW
washer and tighten the oil
draining plug to
9 Nm (6.6 ft-lb).
4.
Fill up the engine oil through the oil filler
neck.
5.
Check engine oil level.
6.
Close the filling cap and wipe clean.
Replace engine oil filter
NOTE!
DO NOT
use an open end wrench on the
hex on top of the oil filter cap. Use a hex socket!
1.
Remove the oil filter cap
(1)
.
2.
Remove the sealing
(2)
.
3.
Remove the oil filter element
(3)
.
!
CAUTION
Lubricant must be applied to the threads of
the oil filter cap prior to installation. Failure
to lubricate the oil filter cap threads can
hinder later removal and cause possible oil
filter cap damage.
4.
Install the
NEW
seal ring
(1)
with clean
engine oil to the oil filter cap
(2)
.
Te
ch
ni
ca
l d
at
a
M
ai
nt
ena
nc
e
O
per
at
in
g
O
ve
rv
ie
w
Summary of Contents for OXE-200 HP
Page 1: ...USER MANUAL OXE 200 HP ...
Page 3: ...Overview 3 INTRODUCTION Publication No ODM1005 Maintenance Operating Technical data ...
Page 4: ......
Page 34: ...28 OPERATING ...
Page 68: ...62 MAINTENANCE TROUBLE SHOOTING Refer to Service Manual ...
Page 72: ......