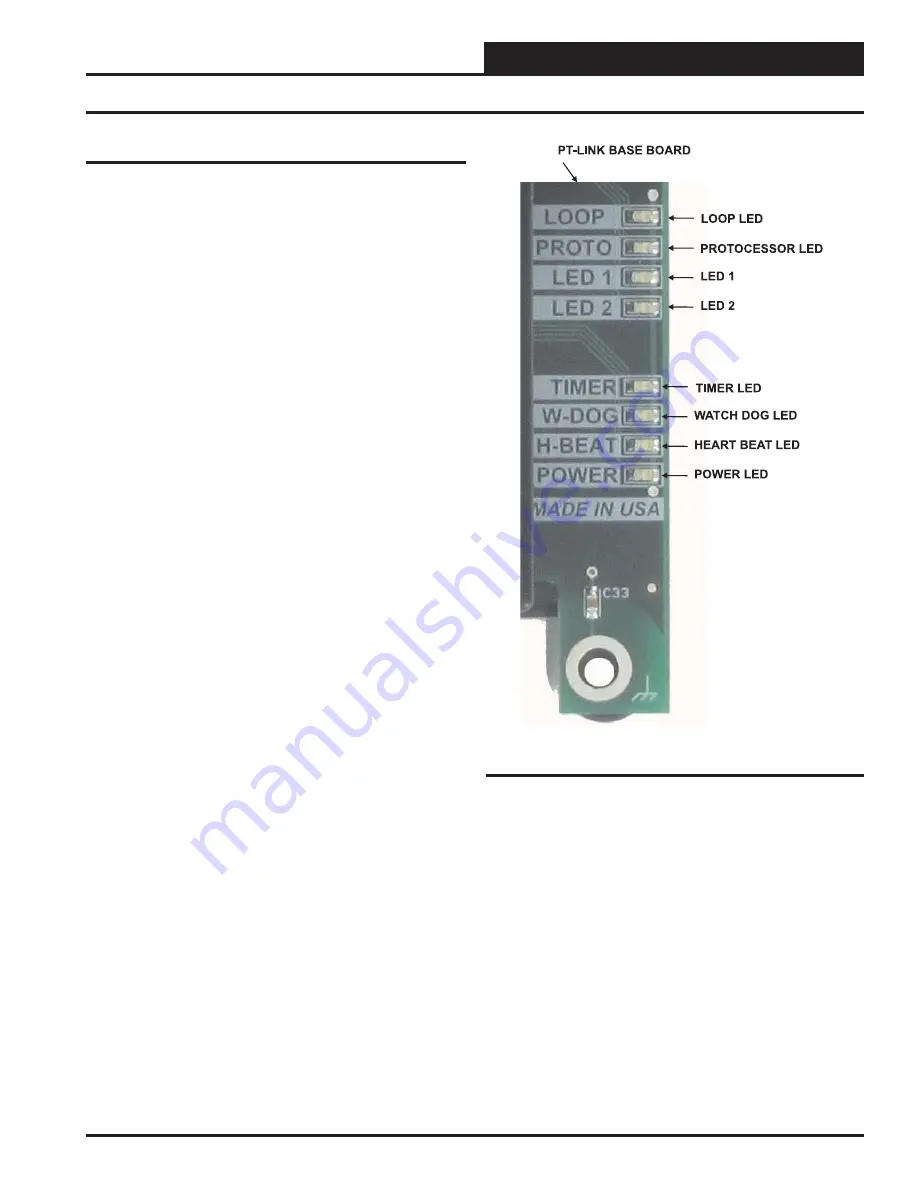
PT-Link II N2-3 Interface
PT-Link II N2-3
®
Technical Guide
13
PT-Link II Board LEDs
The PT-Link II N2
®
is equipped with LEDs that can be used for trouble-
shooting. There are eight LEDs on the PT-Link II board.
See Figure 16
for the locations of the LEDs on the PT-Link II board. The LED descrip-
tions and functions are listed in the following paragraphs.
POWER LED
When the PT-Link II N2
®
is powered up, the “
POWER
” LED should
light up and stay on continuously. If it does not light up, check to be sure
that you have 24 VAC connected to the board, that the wiring connec-
tions are tight, and that they are wired for correct polarity. The 24 VAC
power must be connected so that all ground wires remain common. If
after making all these checks the “
POWER
” LED still does not light
up, please contact WattMaster Controls Technical Support at our Toll
Free number—866-918-1100—for assistance.
LOOP LED
When power is applied to the PT-Link II N2
®,
the “
LOOP
” LED will
also light up. The LED should fl icker rapidly, indicating that the PT-Link
II is trying to communicate with the controllers on the loop. A “
fl icker
”
is defi ned as a brief moment when the LED turns off and back on. If the
“
LOOP
” LED does not operate as indicated above, fi rst power down
the unit and then reapply power. If this does not work, please contact
WattMaster Controls Technical Support at our Toll Free number—866-
918-1100—for assistance.
LED 1
When power is fi rst applied, “
LED 1
” will be off temporarily and then
will blink one time for each controller it is communicating with. For
example, if you have 4 controllers on the loop connected to the PT-Link,
“
LED 1
” will blink 4 times. If the amount of blinks does not match
the number of controllers connected to the loop, it indicates there is a
communications problem. The best way to fi nd out which board is not
communicating is to go to each controller and look at its “
COMM
”
LED. The “
COMM
” LED should be solid and will fl icker occasionally
indicating communication with the PT-Link II N2
®
. If the “
COMM
”
LED does not fl icker, there is no communication with that controller.
LED 2
When power is fi rst applied, “
LED 2
” will be off temporarily and then
will blink slowly indicating that the PT-Link II baseboard is communicat-
ing with the Protocessor Module. If “
LED 2
” does not blink, check that
the Protocessor Module is installed correctly on the PT-Link II baseboard
and that the “
PWR
” LED is lit up on the Protocessor Module.
PROTO LED
When the PT-Link II is fi rst powered up, the “
PROTO
” LED should light
up and stay on continuously. If the LED doesn’t light up, check that the
Protocessor is installed correctly and fi rmly connected to the Base Board.
The “
PWR
” LED should also be lit on the Protocessor Module.
TIMER LED
The “
TIMER
” is used for troubleshooting by WattMaster Controls
Technical Support. The “
TIMER
” LED should always have a steady
blink.
Troubleshooting the PT-Link II Controller
Figure 16: PT-Link II N2
®
LED Locations
WATCH DOG LED
The “
W-DOG
” LED is used for troubleshooting by WattMaster Controls
Technical Support. The “
W-DOG
” LED should always be on solid.
HEARTBEAT LED
The “
H-BEAT
” LED blinks to show there is communication between
the controllers and the PT-Link. If the LED doesn’t light up, and all other
checks have been made, please contact WattMaster Controls Technical
Support at our Toll Free number—866-918-1100—for assistance.